Салон штор в Санкт-Петербурге
Дуговая сварка в защитном газе
Дуговая сварка в защитном газе: описание технологии, режимы, способы
Дуговая сварка в защитном газе представляет собой метод, который значительно повышает качество результата работы. Эта технология имеет ряд особенностей. Прежде чем применять ее, мастер должен ознакомиться с основами дуговой сварки, которая проводится в среде защитных газов. Об особенностях этой технологии будет рассказано далее.
Особенности методики
Одним из подвидов дугового соединения металлических изделий, заготовок является дуговая сварка в защитных газах. ГОСТом регламентирован процесс, во время которого в точку плавления подается газ. Это может быт аргон, кислород, азот или прочие разновидности. Существуют определенные особенности подобного процесса.
Каждый сварщик знает, что качество сварного шва зависит не только от умений мастера, а еще и от условий в точке плавления. В идеальном случае здесь должны присутствовать только электрод и присадочные материалы. Если сюда попадают иные элементы, они способны оказать негативное воздействие на сварку. Место спайки будет из-за этого недостаточно прочным.
Технология ручной дуговой сварки в защитном газе появилась еще в 1920 году. Применение подобных субстанций позволяет сделать швы без шлака. Они характеризуются высокой чистотой, не покрываются микротрещинами. Этот метод активно применяется в промышленности при создании разных элементов из металла.
Особые пропорции защитных газов позволяют снять напряжение в зоне расплава. Здесь не возникают поры, что заметно повышает качество спайки. Шов становится прочнее.
В промышленных условиях в ходе сварочных работ применяют стержни, смешанные с аргоном и диоксидом углерода. Благодаря такой комбинации дуга становится постоянной, оберегая зону расплава от сквозняков. Это позволяет соединить тонкие листы металла.
Если же требуется выполнить глубокую проплавку, смешивают углекислый газ и кислород. Этот состав обладает окислительными свойствами, защищает шов от пористости. Существует множество методик, которые предполагают применять разные газы в ходе сварочных работ. Выбор зависит от особенностей проведения этого процесса.
Техника сварки
Существуют разные режимы дуговой сварки в среде защитного газа. Применяется две основные методики. Первая из них предполагает применение плавящихся шпилей. По ним проходит ток, а стержень из-за этого расплавляется, образуя прочный шов. Этот материал обеспечивает прочное соединение.
Вторая методика предполагает проведение дуговой сварки в защитном газе неплавящимся электродом. В этом случае ток также проходит по стержню, но материал соединяется благодаря расплавлению краев металлических деталей, заготовок. Материал электрода не становится частью шва.
В ходе проведения подобных манипуляций применяются разные газы:
- Инертные. Такие субстанции не имеют запаха и цвета. У атомов присутствует плотная оболочка из электродов. Это обуславливает их инертность. К инертным газам относятся аргон, гелий и т. д.
- Активные. Растворяются в металлической заготовке, вступая с ней в реакцию. К таким средам относятся диоксид углерода, водород, азот и т. д.
- Комбинированные. В ходе определенных процессов нужно применять обе разновидности газов. Поэтому сварка проходит в среде как активных, так и инертных газов.
Чтобы выбрать газовую среду, учитывают состав металла, экономичность самой процедуры, а также свойства спайки. Могут учитываться и прочие нюансы.
В ходе применения инертных газов устойчивость дуги повышается, что позволяет выполнить глубокую расплавку. Подобные вещества подаются в зону расплава несколькими потоками. Если он идет параллельно стержню, это центральный поток. Также есть боковые и концентрические струи. Также газ может подаваться в подвижную насадку, установленную над рабочей средой.
Стоит отметить, что при дуговой сварке, которая происходит в газовой ванне, тепловые параметры приемлемые для производства шва требуемой модели, качества и размера. Выбор режима Чтобы соответствовать требованиям ГОСТ, дуговая сварка в защитных газах может проводиться в разных режимах. Для этого в большинстве случаев требуется применение инверторов полуавтоматического типа. При помощи такой аппаратуры становится возможным регулировать поток электричества, его напряжения.
Инверторные полуавтоматы служат источником питания. Они могут отличаться мощностью, а также опциями. Эксплуатационные качества зависят от модели. Для большинства стандартных операций, в ходе которых не требуется проведение сварки толстых или нечасто используемых сплавов, применяются простые аппараты.
Автоматическая дуговая сварка в среде защитных газов различается массой параметров:
- Радиус проволоки.
- Диаметр проволоки.
- Сила электричества.
- Напряжение.
- Скорость подачи контакта.
- Расход газа.
Существующие полуавтоматические режимы дуговой сварки в защитных газах также разделяют на локальные и общие. В первом случае защитный газ поступает из сопла в зону сварки. Этот вариант применяется чаще. При помощи локальной сварки можно соединить разные материалы, но результат не всегда может быть удовлетворительным.
При использовании локальной подачи газа в зону расплава может попадать воздух. Это снижает качество шва. Чем больше заготовка, которую нужно сварить, тем хуже будет результат при использовании такой методики.
Если нужно сварить крупногабаритные детали, применяются камеры, в которых регулируется атмосфера. Из них откачивается воздух, создается вакуум. Дальше в камеру закачивают нужный по технологии газ. При помощи дистанционного управления производится сварка.
Подготовка к сварке
Чтобы правильно выполнить процедуру соединения металлических заготовок, нужно понимать сущность дуговой сварки в защитном газе. Сварка требует правильной подготовки. Эта процедура всегда одинаковая, независимо от технологии сварки. Сначала кромкам придают правильную геометрию. Это определяется ГОСТом 14771-76.
Механизированная дуговая сварка в защитном газе применяется для полной проварки сплава, что позволяет полностью соединить края заготовки. Зазора между ними не остается. Если же присутствует определенный отступ, разделка краев, проварку можно провести для заготовки, толщина которой не превышает 11 мм.
Для увеличения производительности в процессе автоматической сварки проводится разделка краев заготовок без откосов.
После проведения сварки в углекислом газе потребуется очищать всю плоскость шва от грязи и шлака. Чтобы загрязнение было менее значительным, поверхности обрабатывают особыми составами. Чаще всего это аэрозоли, которые распыляют на металл. Ждать его высыхания не нужно.
В ходе последующей сборки применяются стандартные запчасти, например, клинья, прихватки, скобы и т. д. Конструкция перед началом работы требует тщательного осмотра.
Преимущества и недостатки
Ручная и автоматическая дуговая сварка в защитных газах имеет как преимущества, так и недостатки.
К положительным качествам этого метода относятся:
- Качество шва получается очень высокое. Этого не могут обеспечить иные методики сварки.
- Большинство защитных газов стоит относительно недорого, поэтому процесс сварки не удорожается сильно. Даже дешевые газы обеспечивают качественную защиту.
- Опытный сварщик, который ранее применял иные методики, легко освоит и эту технологию, поэтому поменять специфику маневров сможет даже крупное предприятие с большим количеством сотрудников в штате.
- Процесс универсальный, позволяет сварить как тонкие, так и толстые листы металла.
- Производительность высокая, что положительно сказывается на результатах работы производства.
- Методика применяется не только для сварки черных, но и цветных металлов и сплавов.
- Процесс сварки при использовании газовой защитной ванны легко поддается модернизации. Его можно переделать из ручного в автоматический.
- Процесс сварки можно приспособить ко всем тонкостям производства.
Автоматическая и ручная дуговая сварка в среде защитных газов имеет и определенные недостатки:
- Если сварка производится на открытом участке, нужно обеспечить хорошую герметичность камеры. В противном случае защитные газы могут выветриваться.
- Если же сварка проводится в помещении, здесь обязательно должна быть обустроена качественная система вентиляции.
- Некоторые разновидности газов стоят дорого (например, аргон). Это повышает себестоимость продукции, удорожает весь процесс производства.
Разновидности газов
Дуговая сварка в среде защитных газов производится в разных средах. Они могут быть активными или инертными. К последним относятся такие вещества как Ar, He и прочее. Они не растворяются в железе, не вступают с ним в реакцию.
Инертные газы применяют для сварки алюминия, титана и прочих популярных материалов. Дуговая сварка в защитном газе неплавящимся электродом применяется для стали, которая плохо поддается плавлению.
Активные газы также применяются в ходе проведения подобных работ. Но в этом случае чаще используют дешевые разновидности, например, азот, водород, кислород. Одним из самых популярных веществ, которые применяются в ходе сварки, является двуокись углерода. По цене это самый выгодный вариант.
Особенности газов, чаще всего применяемых в ходе процесса сварки, следующие:
- Аргон не воспламеняется, а также не взрывоопасен. Он обеспечивает качественную защиту сварного шва от неблагоприятных внешних воздействий.
- Гелий поставляется в баллонах с повышенной устойчивостью к давлению, которое здесь достигает 150 атм. Сжижается газ при очень низкой температуре, достигающей -269ºС.
- Двуокись углерода является неядовитым газом, который не имеет запаха и цвета. Это вещество добывают из дымовых газов. Для этого применяется специальное оборудование.
- Кислород является веществом, которое способствует горению. Его получают при помощи охлаждения из атмосферы.
- Водород при контакте с воздухом становится взрывоопасным. При обращении с таким веществом важно соблюдать все требования безопасности. Газ не обладает цветом и запахом, помогает процессам воспламенения.
Особенности сварки в углекислоте, азоте
Дуговая сварка в защитном газе плавящимся электродом проводится при использовании углекислоты. Это самая дешевая методика, которая сегодня пользуется большим спросом. Под воздействием сильного нагрева в зоне плавления СО₂ превращается в СО и О. Чтобы уберечь поверхность от окислительной реакции, в проволоке присутствуют кремний и марганец.
Это также приводит к некоторым неудобствам. Кремний и марганец вступают между собой в реакцию, образуя шлак. Он проступает на поверхности шва, требуя устранения. Это выполнить несложно. На качество сварного шва это обстоятельство никакого воздействия не имеет.
Перед началом работы из баллона удаляют воду, для чего его переворачивают. Это нужно делать с определенной периодичностью. Если не выполнить такую манипуляцию, шов станет пористым. Его прочностные качества будут невысокими.
Дуговая сварка в защитном газе может выполняться при помощи азота. Эта технология применяется для спайки медных заготовок или деталей из нержавейки. С этими сплавами азот не вступает в химическую реакцию. В ходе проведения сварки применяются графитовые или угольные электроды. Если применять для этих целей вольфрамовые контакты, это вызывает их перерасход.
Важно правильно настраивать оборудование. Это зависит от сложности сварки, типа материала и прочих условий. Чаще всего применяется оборудование с напряжением 150-500 А. Оно создает дугу 22-30 В, а расход газа при этом составляет 10 л/мин.
Процесс сварки
Дуговая сварка в защитном газе является эффективной методикой. Но чтобы этого добиться, мастер должен выполнять все требования, выдвигаемые стандартами к этому процессу. Эта методика несколько отличается от иных техник, что мастер должен обязательно учитывать.
Сначала металл готовят для проведения процесса сварки. При использовании такой технологии эта процедура оказывает меньшее воздействие на результат, но проводить ее нужно. Далее проводится настройка оборудования в соответствии с параметрами сварки. Учитывается толщина и тип материала.
Когда оборудование будет готово, производится розжиг дуги. При этом подпаливают пламя горелки. Некоторые разновидности сварки предполагают проведение предварительного прогрева заготовки. Для этого сначала включают горелку, при помощи которой производится предварительная обработка металла.
Когда вокруг дуги начнет образовываться сварочная ванна, начинают подавать проволоку. Для этого оборудование оснащают специальным подающим устройством. Оно поставляет проволоку в зону расплава с определенной скоростью. Если нужно сделать длинный шов, это удобно, так как дугу не придется разрывать. Для этого применяется неплавкий электрод, который поддерживает дугу длительное время.
Если сварка происходит при использовании постоянного тока, его полярность должна быть обратной. Это сокращает вероятность разбрызгивания, но повышается расход металла. Коэффициент наплавления при использовании подобной методики заметно снижается. При прямой полярности он возрастает в 1,5 раз.
Ванну желательно вести слева направо (если мастер правша). Так будет видно процесс формирования шва. Также все действия нужно выполнять по направлению к себе. Шов создается просто, от мастера требуется только ровно вести аппарат на перманентной скорости.
Дуга отрывается от заготовки в обратном направлении относительно движения сварки. В некоторых случаях после такой манипуляции может потребоваться дополнительный прогрев.
Оборудование
Дуговая сварка в защитном газе производится при помощи специального оборудования. Оно применяет стандартные источники электропитания, а также обладает функцией регулировки напряжения.
Агрегаты для сварки оснащаются устройством, передающим проволоку. Также здесь предусмотрены узлы для подачи газов в зону плавления при помощи шлангов из баллонов. Процедура сварки производится при постоянной высокой частотности тока. От правильности регулировки зависит стабильность дуги. Также настраивается скорость подачи проволоки. Наиболее популярными агрегатами для проведения подобной сварки являются:
- «Импульс 3А». Применяется для сварки алюминия, но недостатком является малая функциональность прибора. Его также можно применять для сварки черных металлов, а также создания потолочных швов.
- «ПДГ-502». Применяется для проведения спайки в углекислом газе. Аппарат надежный и производительный. Работает от сети как 220 В, так и 380 В. Электричество может регулироваться от 100 А до 500 А.
- «УРС 62А». Применяется при сварке в полевых условиях. Преимущественно используется для сварки алюминия, но может и обработать титан.
Средства защиты
Сварочные работы при использовании газа отличаются высокой степенью опасности, особенно при использовании взрывоопасных веществ. Поэтому сварщик должен применять в работе индивидуальные средства защиты. Они должны закрывать кожу, глаза, не позволять мастеру вдыхать вредные пары.
Даже если проводится кратковременная сварка в собственном гараже, мастер должен применять специальную маску, респиратор и термоустойчивые краги. В этом случае работа будет выполняться в безопасном режиме, что также сильно отражается на качестве результата.
Дуговая сварка в защитных газах
Оборудование орбитальной сварки из Германии! Низкие цены! Наличие в России! Демонстрация у Вас.
Orbitalum Tools - Ваш надежный партнер в области резки и торцевания труб, а так же автоматической орбитальной сварки промышленных трубопроводов.
Виды сварки - Дуговая сварка в защитных газах
Сварка в защитных газах — один из распространенных способов сварки плавлением. По сравнению с другими способами он имеет ряд преимуществ, из которых главные: возможность визуального, в том числе и дистанционного, наблюдения за процессом сварки; широкий диапазон рабочих параметров режима сварки в любых пространственных положениях; возможность механизации и автоматизации процесса, в том числе с применением робототехники; высокоэффективная защита расплавленного металла; возможность сварки металлов разной толщины в пределах от десятых долей до десятков миллиметров.
Определения, классификация и основные схемы
Сварка в защитных газах (СЗГ) — общее название разновидностей дуговой сварки, осуществляемой с вдуванием через сопло горелки в зону дуги струи защитного газа. В качестве защитных применяют: инертные (Аr, Не), активные (СO2, O2, N2, Н2) газы и их смеси (Аr+СO2+O2, Аr+O2, Аr+ +СO2 и др.).
Разновидности СЗГ можно классифицировать по таким признакам, как: тип защитных газов, характер защиты в зоне сварки, род тока, тип электрода и т. д. (рис. 2.1). По совокупности основных физических явлений процесс дуговой сварки в защитных газах можно классифицировать по двум основным схемам — это сварка неплавящимся (СНЭЗГ) (рис. 2.2, а) и плавящимся (СПЭЗГ) (рис. 2.2,б) электродами.
Сварочная дуга в среде защитных газов характеризуется относительно большим разрядным током (от 5 до 500 А и выше) и низким катодным падением напряжения.
Для сварки неплавящимся электродом применяют в основном инертные газы Аr и Не, а также их смеси в любом соотношении. Эти газы, особенно Не, обладают высокими потенциалами ионизации, что затрудняет первоначальное возбуждение дуги. Однако напряженность электрического поля (E) в столбе дуги в инертных газах имеет сравнительно низкое значение и поэтому дуговой разряд в инертных газах отличается высокой стабильностью. При сварке плавящимся электродом напряжение дуги и стабильность ее существования существенно зависят от состава защитного газа (рис. 2.3).
Повышение напряжения дуги с увеличением концентрации молекулярных газов (Н2, N2, O2 и СO2) объясняется интенсивным охлаждающим действием этих газов в связи с затратами энергии на диссоциацию и отводом теплоты за счет высокой теплопроводности. Увеличение напряжения дуги приводит к снижению ее устойчивости.
Защитные газы
Инертные газы
Практически полностью нейтральными по отношению ко всем свариваемым металлам являются инертные одноатомные газы. Инертные газы применяют для сварки химически активных металлов и сплавов, а также во всех случаях, когда необходимо получать сварные швы, однородные по составу с основным и присадочным металлами.
В сварочном производстве используемый аргон поставляется в газообразном (табл. 2.1) и в жидком состояниях. Газообразный аргон отпускают, хранят и транспортируют в стальных баллонах (по ГОСТ 949—73) или автоцистернах под давлением 15±0,5 или 20±1,0 МПа при 293 К.
При поставке аргона в баллонах (поГОСТ 949—73) вместимостью 40 дм3 объем газа в баллоне составляет 6,2 м3 (при номинальном давлении 15 МПа и 293 К).
Гелий для сварки поставляется по ТУ 51-689—75 трех сортов: марки А, Б и В (табл. 2.2). Транспортируют и хранят гелий в стальных баллонах вместимостью 40 дм3 в газообразном состоянии при давлении 15 МПа или в сжиженном состоянии при давлении до 0,2 МПа. Стоимость гелия значительно выше, чем аргона, поэтому его применяют в основном при сварке химически чистых и активных металлов и сплавов. Применение гелия обеспечивает получение большей глубины проплавления (благодаря высокому значению потенциала ионизации), поэтому его применяют иногда в тех случаях, когда требуется усиление проплавляющей способности дуги или получение специальной формы шва.
Активные защитные газы
В качестве активных защитных газов при сварке широко используют углекислый газ. К активным газам могут быть отнесены также азот и водород, используемые в некоторых сварочных процессах как составная часть защитного газа.
В сварочном производстве азот иногда используют для сварки меди и ее сплавов, по отношению к которым азот является инертным газом. По отношению к большинству других металлов азот является активным газом, часто вредным, и его концентрацию в зоне плавления стремятся ограничить.
Водород в сварочном производстве используют достаточно редко для атомноводородной сварки и дуговой сварки в смеси (Аr+Н2 до 12%). Водород используют только в специальных областях сварки, поскольку он играет важную роль в металлургических процессах сварки. Ввиду возможности образования взрывоопасной смеси между водородом и воздухом при работе с ним следует строго соблюдать требования техники безопасности.
Смеси газов
В ряде случаев для расширения технологических возможностей дуговой сварки целесообразно применять смеси аргона и гелия. Добавка гелия способствует повышению проплавляющей способности дуги.
1. Смесь Аr+(10÷30% N2). Добавка N2 к аргону также способствует повышению проплавляющей способности дуги. Эту смесь применяют при сварке меди и аустенитной нержавеющей стали некоторых марок.
2. Смесь Аr+(1÷5% O2). Примесь кислорода к аргону понижает критический ток, при котором капельный перенос металла переходит в струйный, что позволяет несколько увеличить производительность сварки и уменьшить разбрызгивание металла. Аргонокислородную смесь применяют для сварки малоуглеродистой и легированной стали.
3. Смесь Аr+(10÷20% СO2). Углекислый газ при сварке малоуглеродистой и низколегированной стали способствует устранению пористости в сварных швах. Добавка СO2 к аргону повышает стабильность дуги и улучшает формирование шва при сварке тонколистовой стали.
4. Тройная смесь 75% Аr — 20 % СO2—5% O2 обеспечивает высокую стабильность дуги с плавящимся электродом при сварке стали, минимальное разбрызгивание металла, хорошее формирование шва, отсутствие пористости.
При отсутствии готовых газовых смесей смешивание газов можно осуществлять на сварочном посту. Состав смеси, подаваемой в горелку, регулируется изменением расхода газов, входящих в смесь. Расход каждого газа регулируется отдельным редуктором и измеряется ротаметром типа РС-3.
Способы газовой защиты
По отношению к электроду защитный газ можно подавать центрально или сбоку. Защиту сварочной ванны газом, истекающим из горелки, принято называть струйной. Струйная защита относится к наиболее распространенному способу местной зашиты при сварке. Качество струйной защиты зависит от конструкции и размеров сопла, расхода защитного газа и расстояния от среза сопла до поверхности свариваемого металла. Наилучшая защита расплавленного металла обеспечивается при ламинарном характере истечения газового потока из сопла горелки.
Ориентировочные данные для подсчета расхода аргона на 1 м шва при сварке в нормальных условиях без сносящих потоков приведены в табл. 2.3 и 2.4.
При нормировании расхода газа следует резервировать 15% его количества на продувку газопровода перед началом работы, на неиспользуемый остаток в баллоне (0,3—0,4 МПа), на сварку контрольных образцов и на подварку дефектов сварных швов.
Расход гелия рекомендуется определять по нормативам на расход аргона, вводя поправочный коэффициент 1,3.
Способы сварки
Для расширения диапазона свариваемых толщин, увеличения производительности процесса сварки в защитном газе и повышения качества сварных соединений разработан ряд специальных способов.
Особенности сварки разных металлов и сплавов
Сварка сталей
Сварка малоуглеродистых и низколегированных сталей в инертном газе применяется редко, так как эти стали хорошо свариваются под флюсом и в углекислом газе.
Высокие технологические свойства при сварке сталей обеспечиваются при добавке к аргону до 1—5 % кислорода. Кислород способствует увеличению плотности металла шва, улучшению сплавления, уменьшению подрезов и увеличению производительности процесса сварки.
Для сварки низкоуглеродистых и низколегированных сталей может также применяться аргон с добавкой 10—20 % углекислого газа. Углекислый газ способствует устранению пористости в швах и улучшению формирования шва.
Высоколегированные стали успешно свариваются в инертных газах и их смесях. При этом обеспечивается высокая стабильность дуги и минимальный угар легирующих элементов. Химический состав металла шва регулируется за счет применения проволоки нужного состава. Стали, в состав которых входят элементы с высокой активностью к кислороду (алюминий, титан, цирконий и т. п.), свариваются в среде инертных газов. Ориентировочные режимы автоматической и полуавтоматической сварки стыковых соединений толщиной 4— 10 мм на постоянном токе приведены в табл. 2.11.
Сварка меди и медных сплавов
Медь (Технология сварки меди и ее сплавов) хорошо сваривается в аргоне, гелии и азоте, а также в смеси аргона с гелием и азотом. С целью экономии аргона и повышения производительности целесообразно использовать смесь аргона с азотом (70—80 % аргона и 30—20% азота). Азот способствует увеличению глубины проплавления меди.
Из-за высокой теплопроводности меди для получения надежного провара в начале сварки и хорошего сплавления по кромкам детали подогреваются до 470—770 К. При сварке в аргоне подогрев необходим при толщине меди более 4 мм, а в азоте — более 8 мм. Величину сварочного тока выбирают исходя из диаметра вольфрамового электрода, состава защитной смеси и рода тока. При этом сварка может выполняться как на переменном, так и на постоянном токе обратной полярности.
При сварке латуней, бронз и медноникелевых сплавов предпочтительнее использовать вольфрамовый электрод. При этом испарение цинка и олова будут значительно меньше, чем при сварке плавящимся электродом. Присадочный металл, а иногда и кромки, подлежащие сварке, очищаются травлением. Для этого применяют раствор, состоящий из 75 см3/л HNO3, 100 см3/л H2SO4 и 1 см3/л НСl.
Некоторые режимы сварки стыковых соединений меди в нижнем положении приведены в табл. 2.12.
Сварка алюминиевых и магниевых сплавов
Эти сплавы обладают высокими значениями электропроводности, теплопроводности, а также скрытой теплоты плавления. Трудность сварки этих сплавов заключается в наличии на их поверхности тугоплавкой оксидной пленки, которая препятствует сплавлению металла сварочной ванны с основным металлом и, кроме того, остается в шве в виде неметаллических включений. При сварке на токе обратной полярности происходит катодная очистка свариваемых поверхностей в зоне воздействия дуги. Однако действием разрядного тока может быть разрушена лишь сравнительно тонкая пленка оксида. Толстую пленку оксида алюминия перед сваркой необходимо удалять механическим или химическим путем. Особо важно удалять оксидную пленку с поверхности электродной проволоки малого диаметра (из алюминиевых и магниевых сплавов). Это объясняется тем, что на поверхности оксидной пленки хорошо сорбируется влага, которая, диссоциируя в дуге, приводит к насыщению металла шва водородом и увеличению его пористости. Характер образования пористости зависит также и от химического состава сплава. При сварке алюминий-магниевых сплавов пленка оксидов имеет большую, чем у чистого алюминия, толщину и удерживает больше влаги.
Термически упрочняемые сплавы системы Аl—Mg—Si (марок АВ, АКБ, АКБ) обладают повышенной склонностью к образованию горячих трещин, что определяется наличием легкоплавких эвтектик, расширяющих температурный интервал твердожидкого состояния. Для уменьшения склонности к горячим трещинам этих сплавов целесообразно применять присадки, содержащие 4—6 % Si.
Влияние на качество сварных соединений оказывает выбор конструктивных элементов разделки кромок, которые определены ГОСТ 23949—80.
Накопленный опыт применения сварки конструкций из алюминиевых сплавов позволил отработать режимы, обеспечивающие высокое качество сварных соединений (табл. 2.13 и 2.14).
Сварка химически активных и тугоплавких сплавов
К числу основных затруднений, встречающихся при сварке титановых, циркониевых, молибденовых, никелевых и других тугоплавких сплавов, относится большая химическая активность металла при высокой температуре (особенно в расплавленном состоянии) по отношению к газам (кислороду, азоту, водороду). Поэтому при сварке требуется защита от воздуха не только расплавленного металла, но и участков твердого металла, нагретого до температуры выше 660 К. Обычно это достигается применением специальных приставок длиной до 500 мм и подачей газа с обратной стороны шва через специальные подкладки. При сварке используется аргон только высшего сорта или гелий марки А.
Наиболее надежную и стабильную защиту зоны сварки обеспечивают камеры с контролируемой атмосферой, где в качестве защитной среды используют спектрально чистый или высшего сорта аргон, а также вакуумные камеры, давление в которых не превышает (6—8)*10-2 Па.
Во избежание излишнего перегрева околошовных участков при дуговой сварке, например титана и циркониевого сплава, ограничивают уровень сварочного тока. Максимальная его величина при сварке титана поверхностной дугой вольфрамовым электродом обычно ≤300 А. При этом можно сваривать без разделки кромок за один проход сплавы толщиной 3—4 мм.
Дуговой сваркой в вакууме благодаря высокой концентрации тепловой мощности дугового разряда с полым катодом удается соединять без разделки кромок за один проход титановые сплавы толщиной 8—10 мм. Стыковые соединения титановых сплавов больших толщин выполняют многослойной сваркой с разделкой кромок и подачей присадочной проволоки. Режимы сварки в аргоне стыковых соединений титана приведены в табл. 2,15, 2.16.
Волченко В.Н. "Сварка и свариваемые материалы. том 2"
См. также:
Автоматическая дуговая сварка в защитных газах.
Идея создания сварочного дугового разряда в инертном газе принадлежит Н. Н. Бенардосу; он заявил ее в одном из своих патентов. Однако прошло много времени, прежде чем этот процесс стали широко использовать в технике.
Интенсивное развитие этого вида сварки началось тогда, когда возникла потребность сварки такого активного металла, как алюминий и его сплавы. Ни один из известных видов сварки (электродами, под флюсом) не приводил к положительным результатам, а сварка ацетилено-кислородным пламенем была малопроизводительной и тоже не обеспечивала хорошего качества сварных соединений.
Трудной задачей был выбор газов для создания защиты зоны сварки от воздушной атмосферы.
Металлы при температурах плавления проявляют очень высокую химическую активность, образуя соединения с газами, составляющими атмосферу дугового электрического разряда.
Так, например, азот — инертный газ при обычных температурах — в дуговом разряде начинает реагировать с железом, титаном, алюминием, образуя с ними нитриды, присутствие которых в металле шва резко снижает пластические свойства сварных соединений и способствуют образованию трещин. Только одна медь не реагирует с азотом в этих условиях.
Поэтому чистый азот можно применять как защитный газ при сварке меди.
Не реагируют с металлами в условиях сварки только аргон и гелий, однако это дорогие защитные газы. Аргон содержится в воздухе в количестве менее 1%, его выделяют методами глубокого охлаждения при фракционном испарении жидкого воздуха. Гелия в атмосфере почти нет и его получают из некоторых природных газов.
Применение инертных газов для защиты зоны сварки целесообразно только при. сварке высокоактивных металлов — алюминия и его сплавов, титана и его сплавов и тугоплавких металлов (вольфрам, ниобий, молибден), так как для них других защитных газов подобрать нельзя.
Для сталей можно применять в качестве защитного газа углекислый газ.
По отношению к железу углекислый газ выступает как сильный окислитель:
но ликвидировать последствия окисления сварочной ванны можно, применяя сильные раскислители — марганец и кремний, которые подают через электродную проволоку 10Г2С, содержащую почти 2% Мп и до 1% Si. Соединяясь с кислородом, растворенным в виде закиси железа, они восстанавливают металл сварочной ванны и уходят в шлак в виде окислов (МпО, Si02).
По физическим свойствам углекислый газ подходит для защиты зоны сварки, так как он имеет большую плотность и хорошо вытесняет атмосферу воздуха из зоны сварки С02 легко переходит в жидкое состояние (его критическая температура 31оС) и в баллонах он находится в жидком виде под давлением около 70 ат.
Сварка в углекислом газе плавящимся электродом из легированной проволоки сразу получила широкое применение в промышленности и судостроении. Этот способ позволяет сваривать металл в различных пространственных положениях, обладает высокой производительностью и легко поддается автоматизации.
Кроме того, защитный газ недорогой, его цена определяется степенью его очистки и осушки, так как он получается в качестве побочного продукта энергетических установок (сжигание угля).
За разработку технологии и оборудования, а также за широкое внедрение этого высокопроизводительного и экономичного вида сварки в промышленность авторы были удостоены Ленинской премии.
Для сварки низкоуглеродистой стали в неответственных конструкциях можно применять в качестве защитной среды перегретый водяной пар — наиболее дешевый вид защитного газа (Л. С. Сапиро).
Водяной пар также окисляет металл:
но, применяя легированную проволоку, можно удалить кислород из сварочной ванны так же, как и в случае сварки в углекислом газе. Ухудшение качества сварки вызывает водород, который, частично растворясь в металле, может вызвать образование пор и сильно снизить пластические свойства металла.
Однако из низкоуглеродистой стали он постепенно уходит за счет процессов диффузии, и пластические свойства сварного соединения вновь повышаются («вылеживание»).
Поэтому в перегретом паре нельзя сваривать конструкции и детали, которые сразу воспринимают эксплуатационные нагрузки. Хотя перегретый водяной пар наиболее дешевый защитный газ, его применение весьма ограничено.
Дуговая сварка в защитных газах
Дуговая сварка в защитных газах имеет высокую производительность, легко поддается автоматизации и позволяет выполнять соединение металлов без применения электродных покрытий и флюсов. Этот способ сварки нашел широкое применение при изготовлении конструкций из сталей, цветных металлов и их сплавов. Классификация способов дуговой сварки в защитных газах приведена на рисунке.
Классификация видов дуговой сварки в защитных газах
Дуговая сварка в защитных газах может быть выполнена плавящимся и неплавящимся (вольфрамовым) электродами.
Для защиты зоны сварки используют инертные газы гелий и аргон, а иногда активные газы — азот, водород и углекислый газ. Применяют также смеси отдельных газов в различных пропорциях. Такая газовая защита оттесняет от зоны сварки окружающий воздух. При сварке в монтажных условиях или в условиях, когда возможно сдувание газовой защиты, используют дополнительные защитные устройства. Эффективность газовой защиты зоны сварки зависит от типа свариваемого соединения и скорости сварки. На защиту влияет также размер сопла, расход защитного газа и расстояние от сопла до изделия (оно должно быть 5— 40 мм).
Преимущества сварки в защитных газах следующие:
- нет необходимости применять флюсы или покрытия, следовательно, не требуется очищать швы от шлака;
- высокая производительность и степень концентрации тепла источника позволяют значительно сократить зону структурных превращений;
- незначительное взаимодействие металла шва с кислородом и азотом воздуха;
- простота наблюдения за процессом сварки;
- возможность механизации и автоматизации процессов.
Иногда применяют двойную защиту сварочной дуги (комбинированную). Надежность защиты зоны сварочной дуги зависит от теплофизических свойств и расхода газа, а также от конструктивных особенностей горелки и режима сварки. Подаваемые в зону сварочной дуги защитные газы влияют на устойчивость дугового разряда, расплавление электродного металла и характер его переноса. Размер капель электродного металла уменьшается с увеличением сварочного тока, а увеличение глубины проплавления с увеличением сварочного тока связано с более интенсивным вытеснением жидкого металла из-под электрода вследствие давления сварочной дуги.
При сварке плавящимся электродом дуга горит между изделием и расплавляемой сварочной проволокой, подаваемой в зону сварки. По сварке неплавящимся электродом (вольфрамовые прутки) сварочная дуга может быть прямого или косвенного действия. Разновидностью сварочной дуги косвенного действия может быть дуга, горящая между вольфрамом, и беспрерывно подаваемой в зону дуги сварочной проволокой.
Защитное свойство струи инертного газа зависит от чистоты газа, параметров струи и режима сварки. Одним из наглядных способов оценки защитных свойств является определение диаметра зоны катодного распыления при возбуждении дуги переменного тока между вольфрамовым электродом и свариваемым металлом. В период, когда катодом является свариваемый металл, происходит вырывание частиц металла с поверхности сварочной ванны и соседних зон относительно холодного металла.
Степень катодного распыления зависит главным образом от массы положительных ионов, которые в процессе сварки бомбардируют катод. Например, в среде аргона наблюдается более интенсивное катодное распыление, чем в среде гелия. По убывающей склонности к катодному распылению металлы располагают в следующем порядке: Мg, Аl, Si, Zn, W, Fe, Ni, Рt, Сu, Вi, Sn, Sb, Рb, Аg, Cd.
Сварочную дугу в защитных газах можно классифицировать по следующим основным признакам:
- применяемому для защиты зоны сварки газу — активному или нейтральному;
- способу защиты зоны сварки — одиночным газом, смесью газов или комбинированным;
- применяемому для сварки электроду — плавящемуся или неплавящемуся;
- применяемому току — постоянному или переменному.
Сварка неплавящимся электродом
Условием стабильного горения дуги при дуговой сварке в защитной среде инертных газов на переменном токе является регулярное восстановление разряда при смене полярности. Потенциал возбуждения и ионизации инертных газов аргона и гелия выше, чем у кислорода, азота и паров металла, поэтому для возбуждения дуги переменного тока требуется источник питания с повышенным напряжением холостого хода. Сварочная дуга в среде инертных газов (аргона или гелия) отличается высокой стабильностью и для ее поддержания требуется небольшое напряжение. Высокая подвижность электронов обеспечивает достаточное возбуждение и ионизацию нейтральных атомов при столкновении с ними электронов.
В том случае, когда катодом является вольфрам, дуговой разряд происходит главным образом за счет термоэлектронной эмиссии благодаря высокой температуре плавления и относительно низкой теплопроводности вольфрама, что обусловливает неодинаковые условия горения дуги при прямой и обратной полярности. При обратной полярности (изделие является катодом — минус) напряжение при возбуждении дуги должно быть больше, чем при прямой полярности. Поэтому из-за значительной разницы в свойствах вольфрамового электрода и свариваемого металла кривая напряжения дуги имеет не симметричную форму, а в ней появляется постоянная составляющая, которая вызывает появление в сварочной цепи постоянной составляющей тока. Постоянная составляющая тока в свою очередь создает постоянное магнитное поле в сердечнике трансформатора и дросселя, что приводит к уменьшению мощности сварочной дуги и ее устойчивости. Появление в цепи постоянной составляющей тока не обеспечивает нормального ведения процесса сварки и особенно при сварке алюминиевых сплавов, так как сварочная ванна даже при небольшом содержании кислорода и азота покрывается тугоплавкой пленкой окислов и нитридов, которые препятствуют сплавлению кромок и формированию шва.
Очищающее действие сварочной дуги при сварке переменным током проявляется в те полупериоды, когда катодом является изделие благодаря катодному распылению, так как в этом случае происходит разрушение окисной и нитридной пленок.
При обратной полярности применяют низкие плотности тока, а практически такая дуга не применяется. При прямой полярности тепла выделяется меньше на электроде, так как его значительная часть расходуется на плавление свариваемого металла.
Сварка плавящимся электродом
При дуговой сварке плавящимся электродом в среде защитных газов геометрическая форма сварного шва и его размеры зависят от мощности сварочной дуги, характера переноса металла через дуговой промежуток, а также от взаимодействия газового потока и частиц металла, пересекающих дуговой промежуток, с ванной расплавленного металла.
В процессе сварки на поверхность сварочной ванны оказывает давление столб дуги за счет потока газов, паров и капель металла, вследствие чего столб дуги погружается в основной металл, увеличивая глубину проплавления. Поток газов и паров металла, направляемый от электрода в сварочную ванну, создается благодаря сжимающему действию электромагнитных сил. Сила воздействия сварочной дуги на ванну расплавленного металла характеризуется ее давлением, которое будет тем больше, чем концентрированнее поток газа и металла. Концентрация потока металла увеличивается с уменьшением размера капель, который определяется составом металла, защитного газа, а также направлением и величиной сварочного тока.
Сварочная дуга, образованная в результате плавления электрода в среде инертных газов, имеет форму конуса, столб которой состоит из внутренней и внешней зоны. Внутренняя зона имеет яркий свет и большую температуру.
Во внутренней зоне происходит перенос металла, и ее атмосфера заполнена святящимися парами металла. Внешняя зона имеет менее яркий свет и представляет собой ионизированный газ.
Металлургия сварки в защитных газах
Газы по защитному свойству расплавленного металла сварочной ванны от воздействия азота и кислорода воздуха подразделяются на инертные и активные.
К инертным газам относятся аргон и гелий, которые практически не взаимодействуют с расплавленным металлом сварочной ванны.
К активным газам относятся углекислый газ, азот, водород и кислород.
Активные газы по своему химическому взаимодействию с расплавленным металлом сварочной ванны могут быть нейтральными и реагирующими. Например, азот по отношению к меди является нейтральным газом, т. е. не образует с медью никаких химических соединений. Активные газы и продукты их распада в процессе дугового разряда, т. е. во время сварки, могут соединяться с расплавленным металлом сварочной ванны и растворяться в нем, из-за чего резко снижаются механические свойства сварного шва, а его химический состав не будет соответствовать установленным требованиям стандартов. Однако следует отметить, что некоторые растворимые в металле активные газы не всегда бывают вредными примесями.
Например, азот в углеродистых сталях является вредной примесью (образуются нитриды), из-за чего резко снижаются механические свойства сварного шва и стойкость к старению, тогда как в сталях аустенитного класса азот является полезной добавкой. При аргонодуговой сварке углеродистых сталей для поддува можно применять не только аргон или углекислый газ, но и азот, если в сварочную ванну будут введены элементы-раскислители в виде кремния и марганца. Поэтому выбор газа и присадочного материала должны обеспечивать заданные механические свойства, химический состав и структуру сварного шва. При сварке в защитной среде инертных газов расплавленный металл сварочной ванны изолирован от воздействия кислорода и азота воздуха; поэтому металлургические процессы могут происходить между элементами, содержащимися только в расплавленном металле сварочной ванны.
Так, например, если в сварочной ванне содержится некоторое количество кислорода в виде закиси железа РеО, то при наличии достаточного количества углерода будет образовываться нерастворимая в металле окись углерода [C] + [O] = CO,
Вследствие того, что расплавленный металл сварочной ванны кристаллизуется, а газ выйти не успевает, то в нем будут образовываться поры.
Расплавленный металл сварочной ванны может насыщаться кислородом, находящимся в инертном газе, в виде Свободного кислорода и паров воды. Поэтому для подавления реакции окисления углерода в период кристаллизации расплавленного металла сварного шва в сварочную ванну через присадочный материал должны быть введены элементы-раскислители в виде кремния и марганца. При сварке легированных сталей, имеющих в своем составе необходимое количество раскислителей, реакция образования окиси углерода подавляется. Таким образом, при сварке в защитных газах для подавления образования окиси углерода, способной образовывать поры в сварном шве и устранения азотирования сварного шва, необходимо в сварочную ванну ввести элементы-раскислители.
При сварке в защитной среде углекислого газа последний, защищая расплавленный металл сварочной ванны от кислорода и азота воздуха, сам в свою очередь, разлагаясь в дуговом разряде, является окислителем металла
где FеО — закись железа, растворяющаяся в железе.
Таким образом, как и при сварке в защитной среде инертных газов, в этом случае образуется окись углерода, которая в процессе кристаллизации металла сварочной ванны создает в нем поры. Для подавления образования окиси углерода (СО) через присадочную проволоку в расплавленный металл сварочной ванны вводятся элементы-раскислители — кремний и марганец.
Ручная дуговая сварка в защитном газе (аргоне)
Ручная дуговая сварка в защитном газе (аргоне) должна производиться неплавящимся (вольфрамовым) электродом на постоянном токе прямой полярности. [c.133]Ручную дуговую сварку в защитных газах (аргоне) выполняют с использованием неплавящихся (вольфрамовых) электродов на постоянном токе прямой полярности. Полуавтоматическую и автоматическую сварку производят электродом, находящимся в углекислом газе, на постоянном токе обратной полярности. [c.113]
Ручную дуговую сварку трубопроводов из меди, латуни, алюминия, титана и их сплавов в защитных газах неплавящимся электродом производят на постоянном токе прямой полярности. Трубопроводы из титана сваривают с поддувом аргона. [c.233]
РУЧНАЯ ДУГОВАЯ СВАРКА В ЗАЩИТНОМ ГАЗЕ (АРГОНЕ) [c.116]
Перед сборкой под сварку все детали промывают в специальных моечных камерах бензином до полного удаления следов грязи и масел. Карты для обечаек корпусов имеют продольные и поперечные стыки, к которым прихватывают сваркой технологические планки размером 30 X 60 мм, толщиной, соответствующей толщине свариваемого металла, с разделкой кромок, аналогичной разделке кромок свариваемого стыка. Непосредственно перед сваркой кромки и металл околошовной зоны тщательно протирают тканью, смоченной этиловым спиртом. Карты сваривают ручной аргоно-дуговой сваркой, причем обратную сторону шва зачищают от окисления в приспособлении, представляющем собой секционный короб с газораспределителем и сетками для создания ламинарного потока защитного газа. [c.183]
Дуговая сварка в среде защитных газов может проводиться как ручным, так и механизированным способами. Ручная сварка должна проводиться неплавящимся (вольфрамовым) электродом в среде аргона на постоянном токе прямой полярности. Полуавтоматическая и автоматическая сварка должна проводиться плавящимся электродом в среде углекислого газа на постоянном токе обратной полярности, Ручную сварку неплавящимся электродом в среде аргона следует выполнять присадочной проволокой диаметром 1,6—2 мм. В труднодоступных местах первый (корневой) слой стыков труб допускается выполнять без применения присадочной проволоки при условии, если зазор и смещение кромок не превыщает 0,5 мм, а притупление кромок не превышает 1 мм. Механизированную сварку в среде углекислого газа следует осуществлять проволокой диаметром 1 —1,2 мм. [c.119]
Сварка Электродуговая сварка ручная. Электродуговая сварка полуавтоматическая. Электродуговая сварка автоматическая. Электрошлаковая сварка. Аргоно-дуговая сварка. Сварка в среде защитных газов. Газовая сварка. Стыковка прихватками. [c.150]
На коррозионную стойкость сварного соединения оказывает влияние способ соединения (внахлестку, в угол, встык на медной подкладке или флюсовой подушке, односторонняя или двухсторонняя встык, двухсторонняя многопроходная и т. д.) разделка кромок (V-, Х-, и-образная, ступенчатая с притуплением и др.) толщина свариваемых листов симметричность массы металла относительно шва остающиеся подкладки и пр. Как указывалось, на коррозионную стойкость металла и, следовательно, сварных швов влияет время пребывания при так называемых критических или опасных температурах в процессе сварочного цикла назрев— охлаждение. Это время при разных видах сварки различно. Например, при ручной газовой (ацетилено-кислородной), дуговой в защитном газе (аргоно-дуговой) и дуговой (покрытым электродом) способах сварки для образования сварного соединения необходимы различные затраты погонной энергии (табл. 4). [c.43]
Временная инструкция по ручной аргоно-дуговой сварке технологических трубопроводов из высоколегированных сталей с поддувом защитных газов Временная инструкция по ручной дуговой сварке и контролю сварных стыков трубопроводов из стали 1X13 электродами ферритного класса при ведении монтажных работ [c.479]
В качестве защитной среды при дуговой сварке применяют газы и шлаки, а чаще — комбинированную шлакогазовую защиту. К чисто газовым защитам относятся аргон, гелий, углекислый газ или их смеси между собой или с кислородом к шлаковым, точнее, к шлако-газовым защитам — покрытия ручных металлических электродов, флюсы. [c.51]
Для дуговой сварки применяют угольные или графитовые электроды, имеющие форму стержней длиной 200—700 м,м и диаметром 6—25 мм. Ручная дуговая сварка металлическим обмазанным электродом в настоящее время находит незначительное применение. Дуговую сварку в среде защитных газов применяют для труб из алюминия и его сплавов с толщиной стенки от 1 и выше. Этот способ сварки высокопроизводителен и позволяет сваривать трубы в любом пространственном положении. В качестве защитных газов. при дуговой сварке трубопроводов из алюминия и его сплавов используют аргон. Сварку выполняют неплавящимся (вольфрамовым) электродом на переменном токе и плавящимся электродом на постоянном токе обратной полярности. Сварку неплавящимся электродом труб с толщиной стенки до 8 мм можно осуществлять вручную или механизированным способом (автоматами типа АТВ и полуавтоматами). Для сварки целесообразно применять вольфрамовые электроды ВТ-5, ВТ-10 и ВТ-15, содержащие 1,5—2% окиси тория, или цирконизированные электроды. [c.159]
Примечания 1. При сварке в среде углекислого газа рекомендуется фимеиять осушенную пищевую углекислоту tio ГОСТу 8050—64. Содержание примесей в углекислоте должно быть ограничено воды аргоно-дуговой сварке неплавящимся электродом рекомендуется применять польф-рамовые прутки по СТУ 45-ЦМ-1150 —63 и торированную или лантанировакную проволоку по ВТУ № Вл. 24 — 5 — 62. В качестве защитных газов рекомендуется аргон марок Л, Б н В по ГОСТу 10157—62 или гелий высокой чистоты сорта А или Б по МРТУ 54-04-23—62. [c.227]
ММСС СССР по ручной аргоно-дуговой сварке технологических трубопроводов из высоколегированных сталей и поддувом защитных газов. спецстрой СССР, 1965 г. [c.214]
Автоматическая и полуавтоматическая сварка в защитных газах
Автоматическая и полуавтоматическая сварка в защитных газах
Сущность способа сварки в защитных газах заключается в том, что дуга горит в струе защитного газа, оттесняющего воздух из зоны сварки и защищающего расплавленный металл от вредного воздействия газов, содержащихся в атмосфере.
Основными преимуществами сварки в среде защитного газа перед другими способами являются: надежная защита расплавленного металла от окисления кислородом окружающего воздуха; отсутствие обмазок и флюсов при сварке, усложняющих и удорожающих этот процесс; высокая производительность; простота процесса и возможность его механизации при сварке в различных пространственных положениях с помощью простых приспособлений; возможность сварки цветных металлов, сплавов и разнородных металлов; хороший внешний вид сварного шва и высокие механические свойства соединения; возможность качественной сварки труб без внутренних подкладных колец или ручной подварки.
К недостаткам сварки в защитных газах следует отнести осложнения при проведении сварки на открытом воздухе, особенно в ветреную погоду из-за возможности отдува защитного газа струей воздуха, а также большие выделения вредного газа на рабочем месте сварщика.
В качестве защитного газа используют инертные газы: аргон и азот, не взаимодействующие с расплавленными металлами, а также активные газы и смеси газов: водород, смесь водорода и азота, углекислый газ, смесь аргона и углекислого газа, смесь аргона и кислорода, взаимодействующие в большей или меньшей степени с расплавленным металлом. Защитный газ выбирают в зависимости от свариваемых материалов.
Сваривать в защитных газах можно плавящимся или неплавящимся электродом. При сварке плавящимся электродом электрическая дуга горит между электродной проволокой, подаваемой в зону сварки, и изделием. Дуга расплавляет электродную проволоку и основной металл. При сварке неплавящимся электродом электрическая дуга горит между неплавящимся угольным или вольфрамовым электродом и изделием. Передвигаясь вдоль кромок соединения, дуга оплавляет их. Для сварки неплавящимся электродом используют вольфрамовые стержни диаметром от 0,8 до 10 мм. Диаметр прутка выбирают с учетом требуемой величины сварочного тока.
Способ сварки в струе, аргона плавящимися и неплавящимися электродами нашел применение при изготовлении трубопроводов из нержавеющих и жаропрочных сталей, цветных металлов (алюминий, медь, титан) и их сплавов.
Промышленность выпускает аргон технический, чистый первого и второго сорта. Хранят и транспортируют аргон в стандартных стальных баллонах емкостью 40 л при давлении 150 кгс/см2в газообразном состоянии. Баллоны для хранения технического аргона окрашивают в черный цвет, на верхнюю часть баллона наносят белую поперечную полосу. Баллон имеет надпись «Аргон технический». Баллоны для хранения чистого аргона окрашивают в нижней части в черный, а в верхней части— в белый цвет, на верхней части черными буквами пишут «Аргон чистый».
Источником постоянного тока служат стандартные сварочные генераторы с падающей внешней характеристикой—ПС-300, ПС-500. Величину сварочного тока регулируют балластными реостатами РБ-200 от 10 до 200 а и РБ-300 от 20 до 300 а.
Источником тока при сварке на переменном токе являются стандартные сварочные трансформаторы с дросселями.
Для ручной аргонодуговой сварки неплавящимся электродом используют установку УРСА-600, предназначенную для сварки на переменном токе от 50 до 600 а. В комплект установки входят сварочные горелки, источник питания и аппаратура управления. Кроме того, промышленность выпускает установки УДАР-300 и УДАР-500. Установка УДАР-300 предназначена для сварки вольфрамовым электродом диаметром от 1,5 до 7 мм при силе тока до 300 а, а УДАР-500 — при силе тока до 500 а. В комплект установки входят две горелки, источник питания (трансформатор и дроссель насыщения) и аппаратный ящик.
В последние годы разработано значительное количество различных горелок: ГРАД-1, ГРАД-2, ГРАД-3, ЭЗР-1-54, ЭЗР-2-54. Хорошим качеством отличаются горелки АР-9 и РГС-1.
Автоматическую аргонодуговую сварку применяют для соединения поворотных и неповоротных стыков труб диаметром до 219 мм. Автоматическую сварку неповоротных стыков труб выполняют с помощью специализированных автоматов АТВ (рис. 83), AT и АГН с неплавящимся вольфрамовым электродом. Для сварки поворотных стыков труб применяют полуавтоматы с плавящимся электродом: ПШП-9, ПША-10, ПДА-300 и автоматы АДСП, АДПГ, АДСВ. Кроме указанной аппаратуры в промышленности работает большое количество специализированных установок.
В среде инертного газа — азота сваривают в основном медь и ее сплавы.
Азотно-дуговую сварку меди осуществляют только неплавящимся электродом с подачей в зону дуги присадочного материала. В качестве неплавящегося электрода можно применять угольные или торированные вольфрамовые стержни. Неторированные вольфрамовые стержни частично плавятся при сварке в азоте и загрязняют металл шва вольфрамом.
В среде углекислого газа можно сваривать трубы диаметром от 10 до 1000 мм с толщиной стенки от 0,5 до 30 мм.
Применение углекислого газа позволяет механизировать сварку швов, расположенных в любом пространственном положении, в том числе и в потолочном. Преимуществом сварки в защитных газах является небольшая стоимость углекислого газа. Углекислый газ в 12 раз дешевле аргона.
Жидкую углекислоту, предназначенную для сварки, транспортируют в стальных баллонах при давлении 50—60 кгс/см2. Баллоны должны быть окрашены в черный цвет и иметь надпись «Углекислота». В обычный стандартный баллон емкостью 40 л заливают 25 кг углекислоты. При испарении 25 кг жидкой углекислоты образуется 12 600 л газа.
Рис. 83. Автомат АТВ для аргонодуговой сварки неповоротных стыков труб
Рис. 84. Головка ТСГ-7 для автоматической сварки поперечноколеблющимся электродом поворотных стыков труб
Для сварки можно использовать жидкую «пищевую» углекислоту.
Для сварки труб в среде углекислого газа плавящимся электродом применяют малоуглеродистую проволоку с повышенным содержанием марганца и кремния марок СВ-08ГС и СВ-08Г2С. Сварку в среде углекислого газа ведут на постоянном токе обратной полярности. Устойчивость процесса возможна только при использовании специальных сварочных генераторов с жесткой или возрастающей внешней характеристикой, а также выпрямителей. В качестве источников питания используют сварочные преобразователи ПСГ-350 или ПСГ-500 или универсальные преобразователи ПСУ-500.
Сварку неповоротных стыков труб, приварку фланцев и штуцеров выполняют с помощью полуавтоматов А-547 и А-607. Для сварки поворотных стыков труб могут быть также использованы автоматы АСП-60, А-537, АДСП-2, головка ТСГ-7, ранцевый полуавтомат А-765. Для полуавтоматической сварки в углекислом газе применяют полуавтомат ПДПГ-500 и подающие механизмы полуавтоматов ПШ-5, ПШ-54, ПДШП-500, используемых при сварке под флюсом. Полуавтоматическую сварку труб применяют для выполнения первого слоя шва (с учетом сварки последующих слоев под флюсом) или для полной заварки стыка в два-три слоя.
Головка ТСГ-7 (рис. 84) предназначена для сварки поворотных стыков труб с условным проходом 50—1000 мм при толщине стенки 2 мм и более одной поперечно колеблющейся электродной проволокой. Поперечно колеблющаяся электродная проволока позволяет сваривать стыки труб и деталей с повышенными зазорами и смещением кромок.
1. В чем преимущества и недостатки сварки труб в среде защитных газов по сравнению со сваркой под флюсом?
2. Что такое неплавящиеся электроды, из какого металла их изготовляют?
3. Для каких сталей применяют аргонодуговую сварку?
4. Какое оборудование и какие приспособления используют для ручной аргонодуговой сварки?
5. Укажите область применения сварки в среде углекислого газа.
6. Какое оборудование применяют для сварки в среде углекислого газа?
Все материалы раздела «Сварка труб» :
● Способы сварки трубопроводов и виды сварных соединений
● Подготовка труб под сварку
● Технология газовой сварки и резки
● Кислородно-флюсовая и дуговая резка
● Технология ручной электродуговой сварки, электроды
● Источники питания сварочной дуги
● Автоматическая и полуавтоматическая сварка под флюсом
● Автоматическая и полуавтоматическая сварка в защитных газах
● Сварка трубопроводов из легированной стали
● Сварка трубопроводов высокого давления, термообработка сварных соединений
● Сварка трубопроводов из алюминия и его сплавов, из меди и ее сплавов
● Пайка трубопроводов, дефекты сварных швов
● Контроль качества сварных швов
● Виды сварки и применяемое оборудование
● Сварка и склеивание винипластовых труб
● Сварка полиэтиленовых трубопроводов
● Правила техники безопасности при резке и сварке трубопроводов
Полуавтоматическая сварка в среде защитных газов (MIG/MAG) – Осварке.Нет
Полуавтоматическая сварка — механизированная дуговая сварка металлическим плавящимся электродом (проволокой) в среде защитных газов. Способ также известен как MIG/MAG сварка. В зависимости от типа используемого защитного газа различают сварку в инертных газах (MIG) и активных (MAG). В качестве активных газов преимущественно используют сварку в среде углекислого газа. В отличии от ручной дуговой сварки покрытыми электродами при механизированной сварке подача электрода в зону сварки выполняется с помощью механизмов, а сварщик перемещает горелку вдоль оси шва и выполняет колебательные движения электродом по необходимости.
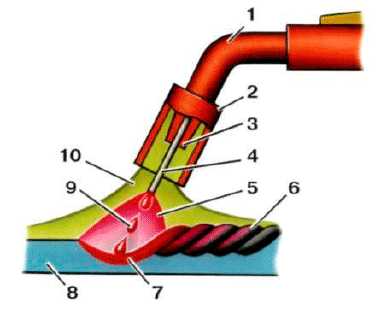
Рис. 1. 1 – горелка, 2 – сопло, 3 – токоподводящий наконечник, 4 – электродная проволока, 5 – дуга, 6 – шов, 7 – ванна, 8 – основной металл, 9 – капля металла, 10 – газовая защита.
Сущность метода и общие принципы полуавтоматической сварки
Механизированная сварка, как и другие виды дуговой сварки, осуществляет за счет большей тепловой энергии сварочной дуги сконцентрированной в месте ее горения. Температура дуги больше температуры плавления металлов, поэтому под ее воздействием кромки сварного изделия плавятся, образуя сварочную ванну из жидкого металла. Дуги при этом горит между основным металлом и сварочной проволокой, которая выполняет функции подвода дуги к зоне сварки и является присадочным металлом для заполнения зазора между кромками.
Сварочная проволока с кассеты непрерывно подается в зону сварки при помощи подающего механизма, который проталкивает ее по каналу в рукаве к соплу сварочной горелки.
Сварочная дуга, расплавленный металл, конец сварочной проволоки, околошовная зона находятся под защитой газа, выходящего с горелки. Для получения более качественного шва, иногда выполняют подачу защитного газа дополнительно с обратной стороны шва.
В отличии от ручной сварки, отсутствие покрытых электродов позволяет механизировать процесс или полностью автоматизировать.
Оборудование для полуавтоматической сварки
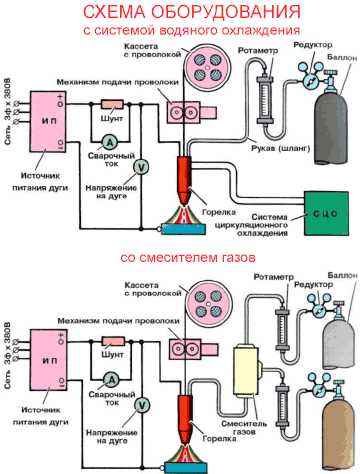
В комплект оборудования для механизированной сварки входят источник питания сварочной дуги, подающий механизм, газовое оборудование, горелка. Для повышения производительности и избежания перегрева горелки при серийном производстве могут использоваться системы охлаждения.
Источники питания сварочной дуги
Для сварки в среде защитных газов изготавливают источники питания с жесткими внешними вольт-амперными характеристиками. Сварка производится на источниках постоянного тока — сварочные выпрямители, преобразователи, инверторы или специальные установки, содержащие в себе источник питания и подающий механизм, а также блок управления. Источники питания переменного тока практически не используются.
Многопостовые источники питания
Для организации работы в цехах на производстве со стационарными сварочными постами целесообразно использовать многопостовые источники питания. Для этих целей можно использовать преобразователи и выпрямители. Существует две схемы организации многопостовой сварки.
Первая схема используется когда сварка производиться одинаковыми режимами на каждом посте с частыми замыканиями сварочной цепи (возбуждение дуги). При такой схеме в цепь каждого сварочного поста включают дроссель, который способствует снижению влияния постов друг на друга при одновременной работе.
Вторая схема может быть использована для регулирования режимов сварки индивидуально на каждом посте с минимальным влиянием постов друг на друга. В таком случае напряжение холостого хода многопостового источника питания устанавливают на максимум, а снижение силы тока (регулирование) выполняется с помощью балластного реостата на каждом посте.
Механизмы подачи проволоки
Механизмы подачи проволоки используются для стабильной подачи проволоки и регулирования скорости подачи в сварочную горелку. Обычно подающий механизм состоит из электродвигателя, редуктора, тормозящего устройства, подающих и прижимных роликов, а также кассеты с проволокой. Существуют различные варианты исполнения подающих механизмов — закрытого и открытого типа.
В зависимости от числа роликов различают двухроликовые и четырехроликовые подающие механизмы. Последние более надежные и рекомендуется использовать для проволоки большего сечения или при сварке порошковой проволокой.
Для увеличения радиуса проведения сварочных работ и обеспечения стабильной подачи сварочной проволоки могут применяться промежуточные механизмы подачи. Это позволяет увеличить зону проведения сварочных работ от 10 до 20 метров. Промежуточные механизмы синхронизируются с основным что позволяет значительно удалятся от источника питания или полуавтомата и газового оборудования.
Механизмы подачи проволоки
Механизмы подачи проволоки используются для стабильной подачи проволоки и регулирования скорости подачи в сварочную горелку. Обычно подающий механизм состоит из электродвигателя, редуктора, тормозящего устройства, подающих и прижимных роликов, а также кассеты с проволокой. Существуют различные варианты исполнения подающих механизмов — закрытого и открытого типа.
В зависимости от числа роликов различают двухроликовые и четырехроликовые подающие механизмы. Последние более надежные и рекомендуется использовать для проволоки большего сечения или при сварке порошковой проволокой.
Для увеличения радиуса проведения сварочных работ и обеспечения стабильной подачи сварочной проволоки могут применяться промежуточные механизмы подачи. Это позволяет увеличить зону проведения сварочных работ от 10 до 20 метров. Промежуточные механизмы синхронизируются с основным что позволяет значительно удалятся от источника питания или полуавтомата и газового оборудования.
Сварочные полуавтоматы
Сварочные полуавтоматы — специальные установки для механизированной сварки в среде защитных газов содержащие в себе источник питания, подающий механизм, горелку и блок управления процессом. Дополнительно полуавтомат может иметь дистанционный пульт управления, включать схемы позволяющие выполнять сварку в импульсно-дуговом режиме и т.д.
Сегодня чаще используется схема сварки от сварочного полуавтомата, чем источник питания + подающий механизм.
Сварочная горелка
Выполняет несколько функций, среди которых: направление проволоки в зону сварки, подвод тока к сварочной проволоке, подача защитного газа, управление процессом при помощи кнопки управления. Все это возможно благодаря использованию специального шланга внутри которого находится сразу несколько элементов — сварочные кабеля, управляющие провода, спиралеобразный канал для направления проволоки, трубка для подачи газа, а иногда и для подачи воды.
Газовое оборудование для полуавтоматической сварки
В состав газового оборудования для сварки полуавтоматом входят: баллон, редуктор, ротаметр, подогреватель, осушитель, смеситель газов, рукава (шланги).
Баллоны
В баллонах хранят и транспортируют сжатые газы. Содержащийся в баллоне газ можно распознать по цвету и надписи на баллоне.
Редуктор (регулятор давления)
Редуктор присоединяется к вентилю баллона, предназначен для понижения давления от баллонного до рабочего и постоянного его поддер
жания. Для регулирования расходов газа (давления) вращают маховик на редукторе.
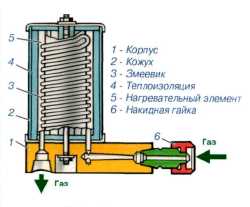
Подогреватель
При сварке в среде углекислого газа редуктор дополнительно комплектуется подогревателем газа, чтобы избежать замерзания редуктора.
При большем расходе углекислого газа наблюдается резкое снижение температуры, что приводит к замерзанию в редукторе влаги содержащейся в углекислоте. Работает подогреватель от постоянного (20 В) и переменного (36 В) тока.
Баллоны
В баллонах хранят и транспортируют сжатые газы. Содержащийся в баллоне газ можно распознать по цвету и надписи на баллоне.
Редуктор (регулятор давления)
Редуктор присоединяется к вентилю баллона, предназначен для понижения давления от баллонного до рабочего и постоянного его поддержания. Для регулирования расходов газа (давления) вращают маховик на редукторе.
Подогреватель
При сварке в среде углекислого газа редуктор дополнительно комплектуется подогревателем газа, чтобы избежать замерзания редуктора.
При большем расходе углекислого газа наблюдается резкое снижение температуры, что приводит к замерзанию в редукторе влаги содержащейся в углекислоте. Работает подогреватель от постоянного (20 В) и переменного (36 В) тока.
Осушитель
Для поглощения влаги находящейся в углекислом газе в состав газового оборудования иногда включают осушитель большего или низкого давления. Осушитель высокого давления устанавливается перед редуктором, а низкого — после редуктора. Поглощает влагу специальное вещество — алюмогликоль или силикагель. Свойства обеих веществ можно восстановить путем прокалывания при температуре 250-300 ºC.
Ротаметр
Ротаметры используются для определения расходов защитного газа, когда на редукторе нет предустановленного расходомера.
Рукава (шланги)
Гибкие трубки изготавливаемые из вулканизированной резины усиленные льняной тканью. С их помощью защитный газ транспортируется к горелке и другим частям газового оборудования.
Смеситель газов
Смеситель газов предназначенный для приготовления смеси газов при подаче из нескольких баллонов.
Техника полуавтоматической сварки
Сварка стыковых соединений полуавтоматом
Детали не большей толщины 0,8-4 мм сваривают без разделки кромок закрепленными в сборочно-сварочных приспособлениях.Сваривают тонкий металл на подкладках из того же металла что и изделие или на медных и нержавеющих съемных подкладках. Металл толщиной свыше 4мм можно сваривать как на весу, так и на подкладках.
Тонкий металл при сварке полуавтоматом гораздо легче сваривается при в вертикальном положении. Сварку ведут углом назад, а горелку передвигают в направлении сверху-вниз. При этом сварщику хорошо видно формирование шва и зону сварки.
Для сварки толстого металла лучше использовать газы повышающие тепловую мощность дуги — гелий или смеси гелия и аргона. При этом нужно следить за положением горелки относительно шва. Небольшое отклонение горелки от вертикали способно привести к несплавлению кромок сварных деталей.
Сварка угловых и тавровых соединений полуавтоматом
Сварку угловых предпочтительней вести при расположении сварных деталей в лодочку. При этом выпуск электродной проволоки увеличивают на 10-15% по сравнению со сваркой стыковых швов в нижнем положении.
Сварка угловых и тавровых швов усложняется плохим наблюдением за формированием шва из-за сопла горелки. Расстояние e = 0, при толщине металла до 5 мм, и e = 0,8-1,5 при толщине металла свыше 5 мм.
Сварка нахлесточных соединений
Сварка нахлесточных соединений при толщине металла меньше 1,5 мм выполняется на медной или стальной подкладке за один проход.
Сварка деталей толщиной более 1,5 мм выполняется на весу за несколько проходов.
Сварка горизонтальных швов полуавтоматом
Сварка горизонтальных швов ведется «углом вперед» без поперечных колебательных движений горелкой. Металл толщиной более 6 мм сваривают за несколько проходов.
Сварка деталей до 3 мм ведется под прямым углом горелки оси горелки относительно сварных деталей, без разделки кромок.
Сварка деталей более 3 мм в горизонтальном положении сваривается с разделкой верхней кромки, а горелка наклоняется относительно верхней детали под углом примерно 70º.
Сварка вертикальных швов
Сварку вертикальных швов рекомендуется выполнять проволокой диаметра 0,8-1,2 мм со свободным формированием шва. Можно применять технику частых коротких замыканий или использовать источники с импульсной дугой. Детали толщиной до 4 мм лучше сваривать способом сверху-вниз без колебательных движений. Если предполагается выполнять сварку односторонним швом, лучше собирать детали с зазором.
Сварка потолочных швов
Потолочные швы толщиной более 6 мм лучше сваривать за несколько проходов. Сварку алюминия и его сплавов полуавтоматом рекомендуется вести углом вперед, а сварку сталей, меди, титана и других металлов — углом назад.
Преимущества и недостатки полуавтоматической сварки
К преимуществам сварки полуавтоматом относят:
- Возможность сравнительно легко получить качественное сварное соединение, в том числе для тонкостенных сварных конструкций.
- Высокая производительность сварки данным методом по сравнению с ручной дуговой сваркой, газовой сваркой и др.
- Механизированную сварку в среде защитных газов можно выполнять во всех пространственных положениях: нижнем, горизонтальном, вертикальном и потолочном.
- Отсутствие флюсов и покрытий, а соответственно операций по очистке шва от шлака.
- Дуга при сварке в защитных газах более сконцентрированная, поэтому зона термического влияния минимальная.
- Сварка сопровождается незначительными напряжениями и деформациями.
- Возможность полной автоматизации процесса сварки.
Недостатки способа:
- При сварке на открытом воздухе или сквозняке повышается вероятность нарушения газовой защиты.
- Разбрызгивание электродного металла во время сварки, особенно при использовании углекислого газа.
- При сварке на режимах с повышенной мощностью возникает потребность в использовании систем водного охлаждения из-за сильного нагрева оборудования.
Методы сварки - MIG, MAG, TIG, MMA, GAS
Сварка является наиболее распространенным методом соединения металлов. Выделите следующие виды сварки:
- GAS
- электроды с покрытием
- 0
- 0
- в газовые щитки 4000310
- 10
- 10 Plasma
- Electronic
Каждый из методов сварки, сварки плавлением или пайки имеет свой уникальный номер по классификации PN-EN ISO 4063.
Функциональное описание
Этот метод сварки заключается в расплавлении кромок соединяемых металлов путем нагрева горящего газа пламенем в атмосфере подаваемого кислорода. В качестве топливного газа в основном используется ацетилен.
Использовать
Газовая сварка применяется для всех видов стали и цветных металлов.
Функциональное описание
Этот метод сварки заключается в сплавлении металлов в месте их соединения с помощью электрической дуги между заготовкой и покрытым электродом.Для дуговой сварки применяют постоянный или переменный ток, но первый предпочтительнее. Для сварки используются покрытые электроды:
- кислая (А)
- рутил (R)
- основание (В)
- Рутиловая кислота (РА)
- целлюлоза (С)
- Рутилцеллюлоза (RC)
- прочие
Использование
Сварка ММА применима ко всем нелегированным, низколегированным и высоколегированным сталям, стальному литью, чугуну и цветным металлам.
Функциональное описание
Метод MAG (Metal Active Gas) представляет собой процесс дуговой сварки плавящимся электродом в среде химически активных газов или газовых смесей. Расходуемый электрод представляет собой сплошную или порошковую проволоку, которая также выполняет роль связующего. В процессах сварки МАГ в качестве защитных газов используется углекислый газ или газовые смеси, содержащие аргон, кислород, углекислый газ и другие.
Применение
Метод МАГ применяется для сварки нелегированных, низколегированных и высоколегированных сталей.
Функциональное описание
Метод MIG (Metal Inert Gas) представляет собой процесс дуговой сварки плавящимся электродом в виде сплошной проволоки в среде инертного газа. Как и в методе МАГ, в качестве связующего выступает проволока (так называемая электродная проволока). В процессе сварки MIG используются благородные защитные газы, такие как аргон и гелий, а также их смеси.
Применение
Метод MIG используется для сварки цветных металлов.
Функциональное описание
Метод TIG представляет собой процесс дуговой сварки неплавящимся электродом в среде инертного газа. Газы, используемые для покрытия зоны сварки в методе TIG: аргон, гелий или их смесь (аналогично методу MIG).
Применение
Сварка ВИГ применяется для соединения низколегированных и высоколегированных сталей и цветных металлов (меди, алюминия, магния и их сплавов, а также никеля).Метод TIG малопроизводителен, но дает высокое качество и точность соединения.
.Сварка TIG, MIG/MAG - EWM AG
Защитный газ TIG
Как видно из названия метода, при сварке TIG обычно используются инертные газы. Защитные газы определены в DIN EN 439. В соответствии с ним они называются l1, l2 и l3.
В качестве защитного газа, наиболее часто используемого при сварке TIG, используется аргон (l1). Степень чистоты должна быть не менее 99,95%. В металлах с высокой теплопроводностью, таких как алюминий и медь, также используется гелий (I2).При использовании гелия в качестве защитного газа дуга имеет более высокую температуру. Однако, прежде всего, распределение тепла между сердцевиной и краем дуги является более равномерным. Использование чистого гелия при сварке TIG в настоящее время редко и ограничено особыми случаями, в то время как смеси аргон/гелий (I3) с содержанием гелия 25, 50 или 75% в последние годы все чаще используются. В результате, например, в случае более толстых алюминиевых конструкций температура предварительного нагрева, необходимая для достижения адекватного плавления, может быть снижена.Кроме того, можно многократно увеличить скорость сварки. В случае сварки ТИГ хромоникелевых нержавеющих сталей для этой цели также применяют смеси аргона и водорода (Р1), но содержание водорода не должно значительно превышать 5 % во избежание образования пор.
Количество потока защитного газа зависит от диаметра газового сопла и окружающего воздушного потока. В случае аргона можно принять ориентировочное значение объемного расхода 5-10 л/мин.В просторных помещениях Рис. 4, могут потребоваться более высокие скорости потока. Для смесей аргон/гелий следует устанавливать более высокие скорости потока из-за низкой плотности гелия.
Группа Р
Группа R содержит смеси аргона и водорода с восстановительным эффектом. Газы группы Р1, кроме аргона и гелия, используются при ТИГ и плазменной сварке, а газы подгруппы 2 с высоким содержанием водорода (Н) - при плазменной резке и для защиты корня (формовочные газы).
Группа I
В группе I сосредоточены инертные газы. Он содержит аргон (Ar) и гелий (He) и смеси аргона и гелия. Они используются для TIG, MIG и плазменной сварки, а также для защиты корня.
Группа М
В обширной группе М, разделенной на подгруппы М1, М2 и М3, сосредоточены газовые смеси для сварки МАГ. Опять же, каждая группа делится на 3 или 4 подгруппы. Газы от M1.1 до M3.3 упорядочены в соответствии с их окислительными свойствами, т.е.M1.1 — слабоокисляющий газ, а M3.3 — наиболее окисляющий газ. Основным компонентом этих газов является аргон, активные компоненты смешиваются с кислородом (O) или углекислым газом (CO2) соотв. кислород и углекислый газ (тройные газы).
Группа С
Ряд газов MAG в группе C содержат чистый диоксид углерода и смесь диоксида углерода и кислорода. Последний случай неприменим в Германии. Газы группы C обладают самыми сильными окислительными свойствами, поскольку CO2 разлагается при высокой температуре дуги с образованием большого количества кислорода в дополнение к монооксиду углерода.
В дополнение к окислительным реакциям состав газа также изменяет электрические и физические свойства в дуговом пространстве и, следовательно, сварочные свойства. Например, при добавлении гелия к аргону теплопроводность и теплоемкость атмосферы дуги улучшаются. Оба эти фактора способствуют получению дуги с более высокой плотностью энергии и, следовательно, лучшими свойствами плавления. Примесь действующих веществ в газовых смесях приводит, в том числе, к к образованию более мелких капель при плавлении проволочного электрода.Кроме того, улучшается теплопередача в дуге. Это также позволяет улучшить оперение.
Требуемый расход защитного газа можно рассчитать на основе эмпирического правила, а именно, в литрах в минуту он должен в 10-12 раз превышать диаметр проволоки.
В случае MIG-сварки алюминия из-за высокой склонности материала к окислению расход устанавливают несколько за пределами этого диапазона, в газовых смесях Ar/He, также значительно выше из-за малой плотности гелия.Давление газа, вытекающего из баллона или кольцевой трубки, сначала снижается. Установленный расход можно прочитать на манометре, откалиброванном вместе с измерительной насадкой, или на расходомере с поплавком.
MAG 135 136 - Интеркастор
Методы сварки MAG 135, 136
11 января 2018 г.
Сварка методом MAG заключается в сварке электрической дугой, производимой между плавящимся электродом и свариваемым материалом. Расходуемый электрод представляет собой постоянно подаваемую проволоку. Дуга и расплавленный металл защищены защитным газом. В качестве защитных газов используются активные газы - углекислый газ или его смесь с аргоном.
Так почему же проводится различие между методами 135 и 136 ?
Чтобы понять основные различия между методами сварки MAG 135 и MAG 136 , необходимо на первом этапе обратиться к применимым стандартам.Основную информацию по этому вопросу можно найти в стандарте PN-EN ISO 4063 «Сварка и родственные процессы – названия и номера процессов»:
МАГ 135 - Дуговая сварка твердым электродом в активной газовой защите.
MAG 136 - Сварка MAG порошковой электродной проволокой
Таким образом, разница в обозначениях методов МАГ 135/136 заключается в сварочной проволоке, используемой в процессе сварки. Упомянутые способы сварки, помимо различий в применяемой сварочной проволоке, характеризуются также различиями в применяемых технологиях сварки и применяются в различных отраслях промышленности.
Преимущества метода MAG 136
• свариваемый материал не должен быть идеально чистым, как в методе MAG-135,
• использование порошковой проволоки ускоряет процесс сварки,
• большая прочность соединений и более глубокое проникновение в материал - сварка с более высокими параметрами.
Недостатки метода МАГ 136
• качество сварного шва зависит от квалификации сварщика,
• после сварки покрытие остается как в методах 111,
• смена валков в питателе.
Применение метода MAG 136
Преимуществом сварки MAG-136 является то, что свариваемый материал не должен быть идеально чистым.Сварка МАГ-136 ускоряет процесс сварки и приближается по прочности к электросварке. Сварка МАГ используется практически во всех отраслях сварочной промышленности, включая тяжелую промышленность и машиностроение, включая судостроение, производство металлоконструкций, резервуаров, трубопроводов, а также ремонтно-эксплуатационные производства.
W Inter-Castor используем следующие методы электросварки:
- электрод с покрытием MMA (111),
- металлический электрод в среде инертного газа MIG (131),
- металлический электрод в среде активного газа MAG (135)
- проволока порошковая в защите активных газов MAG (136),
- вольфрамовый электрод: TIG (141).
Имеем аттестованную технологию сварки листов из никелевого сплава Inconel 600 методами MIG (131) и MMA (111) согласно PN-EN ISO 15614-1 «Спецификация и квалификация технологии сварки. Испытания технологии сварки. Часть 1 : Дуговая сварка и сварка ММА, газовая сварка стали и дуговая сварка никеля и никелевых сплавов».
Нужна помощь специалиста?
Мы прилагаем все усилия, чтобы наши клиенты были полностью удовлетворены как заказами, так и информацией, которую они могут получить, направляя нам свои вопросы.Мы в вашем распоряжении с понедельника по пятницу с 7:00 до 15:00.
Контакт
.МИГ (131) / МАГ (135) - Интеркастор
Сварка МИГ (131) / МАГ (135)
20 сентября 2017 г.
Сварка методом MIG/MAG заключается в сварке электрической дугой, производимой между плавящимся электродом и свариваемым материалом. Расходуемый электрод представляет собой постоянно подаваемую проволоку. Дуга и расплавленный металл защищены защитным газом.
Мы различаем следующие специальные термины для процесса сварки плавящимся электродом в газовой защите:
- MIG - (Metal Inert Gas) - это название используется для описания процесса сварки, когда в качестве защитного газа используется химически инертный газ. , напримераргон, гелий.
- MAG - (Metal Active Gas) - это название используется для описания процесса сварки, когда в качестве защитного газа используется химически активный газ, например CO2.
Краткий обзор процесса сварки MIG/MAG?
Сварочная проволока плавно выходит из держателя и непрерывно плавится в электрической дуге. Расплавленный материал проволоки смешивается с расплавленным материалом, подлежащим склеиванию, с образованием жидкой сварочной ванны. После движения дуги сварочная ванна затвердевает, образуя неразъемное соединение.Через сварочную горелку непрерывно подается защитный газ, который защищает расплавленный металл от атмосферы и охлаждает горелку.
Особенности метода сварки MIG/MAG:
Преимущества:
- универсальный метод - можно сваривать различные металлы и их сплавы во всех положениях,
- высокая эффективность сварки - намного выше, чем покрытыми электродами,
- относительно низкая стоимость сварочных материалов - общие затраты ниже примерно на 20% чем стоимость сварки покрытыми электродами,
- хорошее качество сварных швов,
- возможность механизации и автоматизации способа.
Недостатки:
- качество сварных швов во многом зависит от квалификации сварщика,
- относительно высокие затраты на приобретение приборов и оборудования,
- сварка МАГ более склонна к прилипанию и пористости сварных швов.
Применение метода MIG/MAG
Метод МАГ применяется для соединения, в том числе, нелегированных, низколегированных и высоколегированных конструкционных сталей, а метод МИГ – для сварки алюминия, магния, меди и других цветных металлов и их сплавов.
W Inter-Castor используем следующие методы электросварки:
- электрод с покрытием MMA (111),
- электрод металлический в среде инертного газа MIG (131),
- электрод металлический в среде MAG (135) )
- проволока порошковая в защите активных газов MAG (136),
- вольфрамовый электрод: TIG (141).
Имеем аттестованную технологию сварки листов из никелевого сплава Inconel 600 методами MIG (131) и MMA (111) согласно PN-EN ISO 15614-1 «Спецификация и квалификация технологии сварки. Испытания технологии сварки. Часть 1 : Дуговая сварка и сварка ММА, газовая сварка стали и дуговая сварка никеля и никелевых сплавов».
Нужна помощь специалиста?
Мы прилагаем все усилия, чтобы наши клиенты были полностью удовлетворены как заказами, так и информацией, которую они могут получить, направляя нам свои вопросы. Мы в вашем распоряжении с понедельника по пятницу с 7:00 до 15:00.
Контакт
.Сварщики металлов и операторы сварочного оборудования - Сертификаты - Польский институт сертификации
Правовая / нормативная база для сертификации сварщиков:
Польский институт сертификации - орган по сертификации Люди, в том числе персонал неразъемных соединений - сварщики, соответствуют ряду требований, установленных органом по сертификации, таких как:
- Соответствует требованиям PN-EN ISO/IEC 17024:2012,
- Внедрена, продвигает, поддерживает и управляет системой сертификации в соответствии с PN-EN ISO/IEC 17024:2012 и PN-EN ISO 9712:2012 ,
- Опубликованные спецификации к курсам обучения, включая учебные планы,
- Проводит первичные и периодические надзорные проверки уполномоченного(ых) лица(ов) классификатор(ы) для обеспечения его (их) соответствия спецификациям,
- обучение соответствующим образом оснащенным оборудованием и персоналом, которые периодически контролируются,
- Создана адекватная система ведения записей, которые хранятся в течение одного сертификационного цикла (3 лата) ,
- Она отвечает за выдачу всех сертификатов и ведет их реестр,
- Она отвечает за определение области сертификации.
Выполнение всех вышеперечисленных требований делает сертификацию персонала, выполняющего неразъемные соединения - сертификация сварщиков, проводимая в Польском институте сертификации, адаптирована к международным стандартам и требованиям.
Аттестация сварщиков:
Вначале аттестация сварщиков может показаться достаточно сложным этапом оценки квалификации работников, но наш большой опыт позволяет применять соответствующие решения и соответствующие методы оценки для оптимизации этого процесса.
Аттестация сварщиковсостоит из нескольких переменных областей квалификации - мы представляем их ниже:
- ОБЛАСТЬ КВАЛИФИКАЦИИ В СВЯЗИ С БАЗОВЫМ МАТЕРИАЛОМ
Основной материал | По стандарту |
сталь | PN-EN ISO 9606-1: 2017 |
Алюминий и алюминиевые сплавы | PN-EN ISO 9606-2: 2007 |
Медь и медные сплавы | PN-EN ISO 9606-3: 2001 |
Никель и никелевые сплавы | PN-EN ISO 9606-4: 2001 |
Титан и титановые сплавы | PN-EN ISO 9606-5: 2002 |
- ДИАПАЗОН КВАЛИФИКАЦИИ В ОТНОШЕНИИ ПРОЦЕССОВ СВАРКИ ПО PN-EN 4063: 2011
Первые две цифры определяют группу методов (серая метка в таблице), а третья цифра описывает детали методов сварки.Необходимо выбрать полное описание из трех цифр.
ТАБЛИЦА Обозначение процессов сварки согласно PN-EN ISO 4063: 2011
11 | Дуговая сварка металлическим электродом без газовой защиты |
111 | Ручная дуговая сварка, дуговая сварка электродом ММА завернутый |
112 | Гравитационная сварка MMA |
114 | Дуговая сварка самозащитной порошковой проволокой |
12 | Поддуговая сварка |
121 | Дуговая сварка под флюсом одной проволокой |
122 | Поддуговая сварка ленточным электродом |
123 | Многопроволочная дуговая сварка под флюсом |
124 | Дуговая сварка металлическим порошком под флюсом |
125 | Дуговая сварка порошковой проволокой |
13 | Дуговая сварка в среде защитного газа |
131 | Дуговая сварка в среде инертного газа; сварка методом MIG 9000 4 |
135 | Сварка металлическим электродом в среде активных газов; сварка методом MAG |
136 | Дуговая сварка в активном газе порошковой проволокой |
138 | Дуговая сварка в активном газе порошковой проволокой |
14 | Сварка неплавящимся электродом в среде защитных газов |
141 | Сварка вольфрамовым электродом в среде инертного газа; сварка методом TIG |
142 | Сварка ВИГ без присадочного металла |
143 | Сварка ВИГ проволокой / порошковой проволокой |
145 | Сварка ВИГ с восстановительным газом на твердом связующем |
31 | Газокислородная сварка |
311 | Кислородно-ацетиленовая сварка |
- ОБЛАСТЬ КВАЛИФИКАЦИИ В ОТНОШЕНИИ ДОПОЛНИТЕЛЬНОГО ИЛИ ОСНОВНОГО МАТЕРИАЛА ТАБЛИЦА
Объем квалификации для стали по PN-EN 9606-1:2017 в зависимости от вида связующего по ПН-ЕН ИСО 14171:2016
| СВЯЗАТЕЛЬ | ФМ1 | ФМ2 | ФМ3 | ФМ4 | ФМ5 | ФМ6 |
ФМ1 | Связующее из нелегированных, низколегированных сталей | х | х | - | - | - | - |
ФМ2 | Высокопрочная стальная связка | х | х | - | - | - | - |
ФМ3 | Связующее из Cr ползучести сталей | х | х | х | - | - | - |
ФМ4 | Связующее из жаропрочных сталей 3,75≤Cr≤12% | х | х | х | х | - | - |
ФМ5 | Связующее из нержавеющих и жаропрочных сталей | - | - | - | - | х | - |
ФМ6 | Связующее из никеля и никелевых сплавов | - | - | - | - | х | х |
«Х» - область квалификации; "-" - без квалификации.
Для процессов 142 и 311 (без добавления связующего) группа основного материала, используемая в испытании, представляет собой группу материала, для которой сварщик имеет квалификацию.
Таблица Объем квалификации для алюминия и его сплавов по PN-EN ISO 9606-2:2007 в зависимости от основного материала по ISO/TR 15608:2017
Группа | Тип алюминия и алюминиевых сплавов |
21 | Алюминий с ≤1% примесей или добавок сплав |
22 | Алюминиево-марганцевый сплав |
Алюминиево-магниевые сплавы с Mg ≤ 1,5% 9000 4 | |
Алюминиево-магниевые сплавы с 1,5% | |
Алюминиево-магниевые сплавы с содержанием Mg > 3,5% | |
23 | Сплавы алюминия, магния и кремния |
Алюминиево-цинково-магниевые сплавы | |
24 | Алюминиево-кремниевые сплавы с содержанием Cu ≤ 1%; 5% |
Сплавы алюминия, кремния и магния с содержанием Cu ≤ 1%; 5% | |
25 | Алюминиево-кремниево-медные сплавы с содержанием 5,0% |
26 | Алюминий-медь с содержанием 2% «Все сертификатыСвязаться сСпасибо за интерес к нашему предложению.Если у вас есть какие-либо вопросы, пожалуйста, свяжитесь с нами по электронной почте или телефону.
ул. Wiaduktowa 21 Окружной суд г. Вроцлав Fabryczna во Вроцлаве, 6-й Хозяйственный отдел Государственного судебного реестра, KRS 0000676285, уставный капитал 60 000 PLN 900.000 > Copyright © 2022 Польский институт сертификации Администратором данных является Польский институт сертификации Sp.о.о. ул. Wiaduktowa 21, 52-011 Вроцлав .Цель обработки персональных данных и правовая основа описаны в политике конфиденциальности . Вы должны дать согласие на обработку данных для использования веб-сайта: я согласен Не сейчас |
Сварка TIG/MIG — Руководство по сварке
Введение в сварку
Сварка — это область технологии, связанная со склеиванием, т. е. соединением инженерных пластиков, и процессами, связанными со склеиванием.
Процессы склеивания отличаются друг от друга физическим состоянием основных материалов и металла шва (присадочного материала) в месте склеивания, характером связей, образующих соединение, и типом применяемой тепловой и/или механической энергии для формирования сустава.
Рис. Классификация сварочных процессов.
Целью сварки является создание соединения, состоящего из двух или более частей, путем приложения к ним локальной тепловой энергии, вызывающей их локальное плавление, а затем кристаллизацию, создавая сварной шов, который является неотъемлемой частью соединения. Соединяемые материалы (основные материалы) – это металлы и их сплавы с одинаковыми или близкими физико-химическими свойствами.Сварной шов получают плавлением и смешением основного и дополнительного металлов (связки), но создать сварной шов можно только из расплавленных основных материалов
Рис. Классификация способов сварки.
Способы сварки обозначаются аббревиатурами и цифрами.
E - 111 (MMA) Ручная дуговая сварка покрытым электродом.
MIG-131 (GMAW) Дуговая сварка в среде инертного газа
MAG-135 (GMAW) Дуговая сварка металлическим электродом в активном газе
MAG-136 (FCAW) Сварка порошковой проволокой
MAG-138 (FCAW) Сварка порошковой проволокой в активном режиме газовая защита
TIG - 141 (GTAW) Сварка вольфрамовым электродом в среде инертного газа
Характеристики выбранных методов сварки.
Сварка GMAW, известная как MIG/MAG , заключается в сварке электрической дугой, производимой между плавящимся электродом и свариваемым материалом. Расходуемый электрод представляет собой постоянно подаваемую проволоку. Дуга и ванна расплавленного металла защищены потоком защитного газа.
Следующие термины используются для процесса сварки плавящимся электродом в защитных газах:
MIG - (Metal Inert Gas) - это название описывает процесс сварки, когда в качестве защитного газа используется химически инертный газ, напримераргон, гелий.
MAG - (Metal Active Gas) - это название используется для описания процесса сварки, когда в качестве защитного газа используется химически активный газ, например CO2.
GMAW - (Gas Metal Arc Welding) - аббревиатура, используемая в основном в США, общая для обоих методов: MIG и MAG.
Сварка миграцией, полуавтоматическая сварка, полуавтоматическая сварка - это общие названия процесса сварки, как методами MIG, так и MAG.
Сварка GTAW или TIG (вольфрам в инертном газе) — это производство электрической дуги с использованием неплавящегося вольфрамового электрода в среде инертного газа.Часто встречается обозначение GTAW (Gas Tungsten Arc Welding) (в основном в США).
Сварочная дуга между неплавящимся электродом и заготовкой плавит поверхность заготовки. При сварке TIG нет необходимости использовать какой-либо дополнительный материал. Сварные элементы можно соединять путем переплавки разделки под сварку. Однако если используется дополнительный материал, то он вводится в ванну вручную, а не с помощью сварочного пистолета, как в методе MIG/MAG.Поэтому при сварке TIG сварочная горелка имеет совершенно другую конструкцию, чем горелка, используемая в методе MIG/MAG. Связующее обычно выпускается в виде проволоки (стержня) длиной 1 м и правильно подобранного диаметра.
Процесс сварки TIG происходит в атмосфере химически инертного защитного газа, обычно аргона или гелия, поступающего из сопла электрододержателя. Защитный газ защищает сварной шов и электрод от окисления, но не влияет на металлургический процесс.
Сварка ММА - ММА
ММА (Ручная дуговая сварка) - старейший и наиболее универсальный метод дуговой сварки.
В методе ММА используется электрод с покрытием, который состоит из металлического сердечника, покрытого сжатой оболочкой. Между концом электрода и заготовкой возникает электрическая дуга. Зажигание дуги происходит контактным путем прикосновения конца электрода к свариваемому материалу. Электрод плавится, и капли расплавленного металла электрода переносятся через дугу в расплавленную сварочную ванну, образуя сварной шов после охлаждения. Сварщик перемещает электрод по мере его приплавления к заготовке, чтобы поддерживать дугу постоянной длины и одновременно перемещает ее плавящийся конец по линии сварки.Плавящееся электродное покрытие выделяет газы, защищающие расплавленный металл от влияния атмосферы, а затем застывает и образует на поверхности ванны шлак, предохраняющий застывающий металл шва от воздействия окружающей среды. После укладки одного стежка шлак необходимо удалить механическим способом.
Основное отличие от других методов сварки заключается в том, что в методе ММА электрод укорачивается. В методах TIG и MIG/MAG длина электрода все время остается неизменной, а расстояние между горелкой и заготовкой всегда постоянным.В методе ММА для поддержания постоянного расстояния между электродом и сварочной ванной электрододержатель необходимо постоянно перемещать в сторону заготовки, в связи с чем особую роль играет мастерство сварщика.
.
Методы сварки - газ, MMA, MAG, MIG, TIG
Работа сварщиком — очень ответственная задача. Именно сварщик окончательно соединяет изготовленные элементы, и от качества его работы зависят прочность и безопасность конструкции, а также здоровье и жизнь ее будущих пользователей. Вот почему правильная подготовка, навыки и точность в этой позиции так важны.
Существует столько же видов квалификации сварщиков , сколько существует методов сварки .Каждый из методов имеет свои преимущества и недостатки, и трудно четко определить, какой из них следует считать лучшим и наиболее эффективным, и какие критерии оценки следует использовать. Имеет ли значение качество и прочность сварного шва? А может важна скорость, простота и стоимость внедрения? Давайте подробнее рассмотрим каждый метод.
Мы различаем следующие методы сварки, плавления и пайки. Все они должным образом классифицированы и имеют уникальный номер в соответствии с PN-EN ISO 4063.
Газовая сварка
Сварка ММА
Дуговая сварка под флюсом
Газовая дуговая сварка
Электронная сварка
· Лазерная сварка
Гибридная сварка
Плазменная сварка
Шлаковая сварка
Сварка трением
К наиболее популярным методам относятся: газовая сварка , дуговая сварка покрытыми электродами и сварка в газовой защите: MIG, MAG и TIG.
Газовая сварка - метод 311
Газовая сварка используется для соединения всех сталей и цветных металлов. При газовой сварке различают 3 типа сварных швов: стыковые, угловые и сквозные. Наиболее распространенным газом, используемым в процессе газовой сварки, является ацетилен (С2х3), а сам процесс основан на нагреве пламени горючего газа в атмосфере подаваемого кислорода. Отсюда и название метода 311 - кислородно-ацетиленовый.
Метод 311 обычно используется для сварки, в том числе: сантехнических, отопительных, тепловых, котельных, энергетических и газовых установок , т. е. везде, где свариваются металлические листы толщиной до 10 мм и тонкостенные трубы. Поэтому квалификация сварщика, метод 311, пригодится, в том числе на все работы в жилых домах. Преимуществами газового метода являются: простота эксплуатации устройств, низкая стоимость, универсальность использования горелки (резка, сварка или нагрев), гибкое регулирование подачи тепла или высокий контроль над процессом сварки.
Дуговая сварка ММА - метод 111 / метод ММА
Дуговая сварка MMA , также известная как метод MMA (ручная металлическая дуга), была признана наиболее универсальным и универсальным методом сварки на протяжении лет. Он широко используется в промышленности - производстве, строительстве и судостроении. Но он также популярен для небольших проектов — ремонта установок или даже хобби.Он характеризуется очень высокой гибкостью и возможностью сочетать различные виды и марки металлов и сплавов: легированные и нелегированные стали, чугун, медь или никель. Большим преимуществом также является возможность сварки в труднодоступных местах и различных положениях, на высоте и даже под водой . Сварку ММА покрытыми электродами также выбирают в случае сложных погодных условий , при усилении ветра или дождя. Высокое качество, долговечность и эстетичность сварных швов ценятся, а также высокие механические свойства сварного шва.
Однако у этого метода есть несколько недостатков. Качество сварного шва во многом зависит от опыта и навыков сварщика, низкой производительности труда, низкой скорости сварки, необходимости частого удаления шлака и замены электродов, что удлиняет процесс и затраты. В процессе сварки также выделяется большое количество газов и сварочного дыма.
Сварка в среде защитных газов плавящимся электродом и порошковой проволокой – методы MAG 135 и MAG 136
Методы MAG (Metal Active Gas) состоят из дуговой сварки плавящимся электродом в среде химически активных газов или газовых смесей.Плавкий электрод представляет собой металлическую проволоку или непрерывно подаваемую порошковую проволоку, которая здесь является своеобразной связкой. Применяется для сварки нелегированных, высоколегированных и низколегированных сталей. В качестве защитных газов используются углекислый газ или газовые смеси, аргон, CO2 или кислород. Сварка MAG широко используется в в тяжелой промышленности, машиностроении, судостроении, железной дороге, автомобилестроении, нефтепереработке, а в производстве крупных стальных конструкций или трубопроводов.
Преимуществами метода МАГ являются сварка материалов с широким диапазоном толщин, высокая прочность шва и высокая производительность труда.Этот метод будет хорошим выбором везде, где имеет место серийное производство и где будут соединяться крупногабаритные элементы.
Защита от инертных газов плавящимся электродом - метод MIG 131
Методы MIG (металлический инертный газ) и MAG во многом схожи. Как и в методе МАГ, плавкая проволока действует как связующее вещество, а инертные газы, такие как аргон или гелий, используются в качестве защитных газов. Сварка МИГ , в отличие от сварки МАГ (сварка стали), в основном используется для соединения меди и алюминия, а также других цветных металлов и их сплавов.
Как и в случае метода МАГ, МИГ применяется в тяжелой промышленности - кораблестроении, судостроении, машиностроении, железнодорожном транспорте и в производстве крупногабаритных строительных электродеталей. Этот метод имеет очень широкий диапазон толщин и размеров свариваемых материалов.Он также отличается высокой степенью автоматизации и идеально подходит для использования в непрерывном серийном производстве, где важны скорость и воспроизводимость компонентов.
Сварка в среде инертного газа неплавящимся электродом - метод TIG 141
TIG — еще один метод сварки с использованием электрода в среде защитного газа, на этот раз в среде инертного газа. Это процесс дуговой сварки. Защитными газами в этом методе являются аргон, гелий и их смеси, такие же, как и в методе МИГ.
Метод TIG 141 будет работать везде, где важна эстетика сварного шва , а также высокое качество и точность соединения. Применяется для сварки одиночных элементов или элементов относительно небольших размеров . Мы используем метод TIG для соединения высоколегированной и низколегированной стали, а также цветных металлов, таких как алюминий, медь, никель, магний и их сплавы.
К основным преимуществам метода TIG относятся: высокое качество и чистота соединения, диапазон толщины материала от 1 до 10 мм, высокий контроль над процессом сварки и возможность сварки различных материалов между собой.
-------------------------------------------------- -------------------
Хотите научиться сварке у лучших обучающих специалистов в Гданьске?
Занятия в хорошо оборудованной студии - в небольших группах. Неограниченный доступ к сварочным материалам для студентов. 15 современных вентилируемых станций. Широкий штат сотрудников с высоким уровнем предметных и практических знаний, а также опытом работы в оффшорном, гражданском и судостроении.
См. полное предложение курсов для сварщиков в Инженерном учебном центре в Гданьске
.