Салон штор в Санкт-Петербурге
Минеральный порошок гост
Минеральный порошок МП-1: активированный и неактивированный
МИНЕРАЛЬНЫЙ ПОРОШОК
ГОСТ Р 52129-2003. ГОСТ 32761-2014.
Минеральный порошок производится из осадочных (карбонатных) горных пород (известняка) месторождения «Подкамешек». Мы выпускаем два вида минерального порошка марки МП-1: активированный и неактивированный.
Минеральный порошок производится в соответствии с требованиями ГОСТ Р 52129-2003. ГОСТ 32761-2014.
ИНФОРМАЦИОННАЯ СПРАВКА
Порошок минеральный неактивированный: материал, полученный при помоле горных пород или твердых отходов промышленного производства. Порошок минеральный активированный: материал, полученный при помоле горных пород или твердых отходов промышленного производства с добавлением активирующих веществ, при помоле битуминозных пород, в том числе горючих сланцев. Порошки в зависимости от показателей свойств и применяемых исходных материалов подразделяют на марки: МП-1 - порошки неактивированные и активированные из осадочных (карбонатных) горных пород и порошки из битуминозных пород. МП-2 - порошки из некарбонатных горных пород, твердых и порошковых отходов промышленного производства. |
В качестве активирующего вещества при производстве активированного минерального порошка применяется АЗОЛ 1010 марка В.
ПАСПОРТ БЕЗОПАСНОСТИ ХИМИЧЕСКОЙ ПРОДУКЦИИ
ПАСПОРТ КАЧЕСТВА
ОБЛАСТЬ ПРИМЕНЕНИЯ
Минеральные порошки применяются в дорожном строительстве в качестве компонента асфальтобетонных и других видов органоминеральных смесей (Смеси асфальтобетонные по ГОСТ 9128, Смеси асфальтобетонные щебеночно-мастичные по ГОСТ 31015, Смеси органоминеральные по ГОСТ 30491). Неактивированный порошок также применяется в качестве наполнителя при производстве сухих строительных смесей, в химической промышленности в качестве минерального наполнителя при производстве пресс-порошков, резинотехнических изделий, красок и др.
ПОКУПКА И ДОСТАВКА МИНЕРАЛЬНОГО ПОРОШКА
Купить минеральный порошок в Хакасии или в близлежащих регионах и/или получить дополнительную информацию вы сможете, позвонив нам или отправив письмо на наш электронный адрес.
Доставка минерального порошка осуществляется нашим автотранспортом либо самовывозом с промышленной зоны “ЗАО Карат-ЦМ”. А также железнодорожным транспортом со станции “Ербинская”. Подробно об условиях отгрузки и доставки щебня вы сможете узнать, позвонив нам или отправив письмо на наш адрес.
Минеральный порошок продается и доставляется в МКР по 750-950 кг.
КОНТАКТНЫЕ ДАННЫЕ
Телефон/факс: +7 (39033) 26-556
E-mail: Адрес электронной почты защищен от спам-ботов. Для просмотра адреса в вашем браузере должен быть включен Javascript.
Время работы офиса: Понедельник - пятница с 8.00 до 17.00 обед с 12.00 до 13.00
ДОКУМЕНТЫ О КАЧЕСТВЕ
СЕРТИФИКАТ НА МИНЕРАЛЬНЫЙ ПОРОШОК МП-1
ГОСТ Р 52129-2003
ПРОТОКОЛ ИСПЫТАНИЙ ПО ГОСТ 32761-2014
ДЕКЛАРАЦИЯ О СООТВЕТСТВИИ НА МП-1 ПО ГОСТ 32761-2014
ГОСТ 32761-2014
ПРАЙС-ЛИСТ ООО "СТРОЙМАТЕРИАЛЫ"
СКАЧАТЬ ПРАЙС-ЛИСТ
ООО "Стройматериалы" также реализует: песок, щебень-известняк, отсев, щебеночно-песчаная смесь, муку известняковую, муку известняковую для комбикормов, пыль инертную.
Минеральный порошок - ООО Инко-Балт
Компанией «Инко-Балт» в 2021 г. на промышленной площадке Карьера Борницы построен и запущен в эксплуатацию современный высокотехнологичный комплекс по производству минерального порошка, согласно ГОСТ 32761 – 2014 с поправками в ИУС Н12 2016, ИУС Н12 2019, ГОСТ Р 52129-2003 с производительностью первой очереди до 300 тысяч тонн в год.
После запуска второй очереди запланированной на 2022-23 года, мощность производства увеличится до 550 тыс тон в год.
Минеральный порошок – это материал, который получают путем дробления и тонкого измельчения (помола) карбонатных горных пород (известняков, доломитов). В основном, его применяют при изготовлении искусственного асфальта, где порошок служит заполнителем. Этот заполнитель повышает вязкость и клеящую способность битума. Он имеет адсорбирующую поверхность и поглощает значимую часть нефтяного битума, что придаёт асфальтобетону прочность и устойчивость к деформациям и повышает качество получаемого асфальтобетона.
Также, минеральный порошок широко применяется при изготовлении сухих строительных смесей, бетона и добавок для него, кровельных материалов. Используется для усиления фундаментов, повышения несущей способности конструкций и предотвращения осадки грунта.
Минеральный порошок МП-1 и МП-2 изготавливаются в соответствии с требованиями ГОСТ 32761 – 2014 с поправками в ИУС Н12 2016, ИУС Н12 2019, ГОСТ Р 52129-2003.
Минеральный порошок МП-1
Это активированные или неактивированные минеральные порошки, полученные помолом карбонатных осадочных горных пород . Применяют в качестве компонента асфальтобетонных и других видов органоминеральных смесей.
Минеральный порошок МП-2
Это неактивированный минеральный порошок из карбонатных осадочных горных пород или вторичных отходов промышленного производства. Его применяют так же, как и МП-1.
Что такое минеральный порошок
Минеральный порошок – это остаток, образующийся в процессе дробления известняковых горных пород или отходы промпроизводства, которые затем подвергаются тонкому помолу. Чтобы повысить эксплуатационные характеристики, в них добавляют поверхностно – активные вещества или их содержащие компоненты. Основная сфера применения – это производство асфальтобетона.
Наиболее распространены:
- Каменная мука;
- Доломитовая мука;
Преимущества активированного минерального порошка
- Хорошее смачивание битумом
- Низкая водопроницаемость
- Пониженная пористость
- Отсутствие слеживаемости при перевозке и хранении
Технические характеристики минерального порошка.
Производство продукции способом тонкого помола твердого сырья регламентируется ГОСТом 32761 – 2014 с поправками в ИУС Н12 2016, ИУС Н12 2019, ГОСТ Р 52129-2003. Согласно нормативу, минеральный порошок – это сухое сыпучее вещество без примесей, несанкционированных ГОСТом. Если соблюдаются правила транспортировки и хранения - срок годности материала практически не ограничен, но активированный продукт более требователен к этим условиям.
Различают марки порошка в зависимости от состава:
- МП-1 – может быть активированным и неактивированным. Изготавливается дроблением осадочных горных пород;
- МП-2. Производится помолом карбонатных горных пород и отходов промпроизводства;
По Вашей заявке:
- Изготовим минеральный порошок различной тонкости помола;
- Предоставим образцы для лабораторных исследований;
- Предоставим необходимые консультации по вопросам технологии применения наших минеральных порошков;
- Упакуем в тару, соответствующую ГОСТу;
- Осуществим погрузку, доставку в любой регион РФ;
Проверяя свойства минерального порошка лабораторным путем, определяют:
- Истинную плотность (ρ) – это плотность сыпучего вещества после уплотнения без учета имеющихся в нем пор;
- Среднюю плотность (ρm) – определяется после уплотнения сыпучего вещества под нагрузкой 40 МПа;
- Пористость (Vпор) – величина, определяемая по формуле Vпор = (1 - ρm/ρ)*100
Технология приготовления активированного минерального порошка.
Поверхностно-активные вещества (ПАВ) повышают гидрофобные характеристики минерального порошка. Выбирают ПАВ - добавки со знанием того, какие требования будут предъявлены к конечному продукту.
В процессе активации между свежемолотым минеральным порошком и ПАВ образуются прочные связи. Добавляют ПАВ впрыскиванием в измельчительную камеру, где каждая микрочастица порошка покрывается микропленкой. В результате этого он приобретает гидрофобные свойства, а его взаимодействие с битумом - улучшается.
Виды активаторов в составе минеральных порошков:
- Анионные поверхностно-активные вещества – жировой гудрон, синтетические жирные кислоты, петролатум окисленный;
- Катионные ПАВ – диамины, амины, их производные;
Закрытая структура пор асфальтобетона с карбонатными минпорошками обеспечивает их низкое водопоглощение и высокую морозостойкость.
Преимущества асфальтобетонных смесей с активированными минпорошками, по сравнению с асфальтобетоном с неактивированными сыпучими веществами:
- Снижение расхода битума на 10%;
- Уменьшение числа проходов асфальтных катков, необходимого для нужной степени уплотнения;
- Более низкая температура, при которой может укладываться и уплотняться асфальтобетон
Области применения минерального порошка
Дорожное строительство
Мягкая кровля
Сухие смеси
Комбикорм
С/Х
Прочее
Добавки для бетона
Дорожное строительство
Минпорошки из карбонатных пород – основная часть асфальтобетона, которая обеспечивает конечному продукту прочность, устойчивость к трещинообразованию, сильному давлению, упругость, а также увеличенный рабочий период.
Покрытия с этим составом устойчивы к коррозии. При увеличении содержания битума – повышается устойчивость и себестоимость асфальтобетона, что ухудшает остальные свойства.
Минеральный материал МП-1 широко применяется при сооружении автодорог районного значения и автомобильных трасс на территории России и соседних государств.
Производство сухих строительных смесей
Карбонатные минпорошки часто используются в качестве наполнителей в сухих смесях, которые по технологии наносятся тонким слоем.
Производство бетонных смесей
Карбонатный минпорошок, добавляемый в бетон, положительно влияет на его свойства: увеличивает прочность затвердевшего продукта, деформационную стойкость, устойчивость к высоким температурам и снижает водопоглощение.
Получить все необходимые консультации по вопросам технологии применения наших минеральных порошков или заказать их вы сможете связавшись с нами по указанным телефонам или заполнив форму для обратной связи с вами.
Минеральный порошок для асфальтобетонных смесей
<< МАТЕРИАЛЫ ДЛЯ ДОРОЖНОГО СТРОИТЕЛЬСТВА И ЛАНДШАФТА
.
МИНЕРАЛЬНЫЙ ПОРОШОК ДЛЯ АСФАЛЬТОБЕТОННЫХ СМЕСЕЙ
ГОСТ Р 52129-2003
Минеральный порошок используется в качестве компонента при производстве асфальтобетонных и щебеночно-мастичных смесей, повышая их механическую прочность, способность к упругим и пластическим деформациям. Его использование существенно улучшает качество дорожного покрытия и увеличивает срок его службы, а также дает значительную экономию при производстве асфальта и эксплуатации дорог.
Различают два вида минеральных порошков: активированный и неактивированный.
Активированный минеральный порошок имеет следующие преимущества: гидрофобен, обладает высокой «битумоемкостью», что позволяет равномерно распределяться в битуме. Применение данного продукта приводит к большей плотности и однородности асфальтобетона, предотвращает проникание влаги, снижает водонасыщение асфальтобетона, что положительно сказывается на сроке эксплуатации автодорог. Особое значение приобретает возможность использования его в асфальтобетоне, где присутствуют глинистые частицы. Основные показатели качества минерального порошка: зерновой состав, влажность и гидрофобность.
Требования к минеральным порошкам согласно ГОСТ Р 52129-2003:
Наименование показателя | Значение для порошка марки МП-1 | |
Неактивированный порошок | Активированный порошок | |
Зерновой состав, % по массе:- мельче 1,25 мм- 0,315 - 0,071 | Не менее 100Не менее 90От 70 до 80 | Не менее 100Не менее 90Не менее 80 |
Пористость, %, не более | 35 | 30 |
Набухание образцов из смеси порошка с битумом, %, не более | 2,5 | 1,8 |
Водостойкость образцов из смеси порошка с битумом, %, не более | Не нормируется | |
Показатель битумоёмкости, г, не более | То же | |
Влажность, % по массе, не более | 1,0 | Не нормируется |
.
Упаковывается минеральный порошок в одноразовые мягкие контейнеры (МКР) с полиэтиленовым вкладышем по 1 тонне, либо клапанные контейнеры (МКР). Также, возможна погрузка без упаковки на специализированный транспорт (автоцистерны и цементовозы). Минеральный порошок можно хранить как в складских помещениях закрытого и открытого типа в упакованном виде, так и на открытых территориях (активированный порошок). При соблюдении всех условий транспортировки и хранения, срок хранения минерального порошка не ограничен.
Минеральный порошок МП-1 ГОСТ для асфальтобетона | Минеральный порошок оптом от производителя
ГОСТ Р 52129-2003
Стоимость (с НДС) 1 тонны навалом - договорная +скидка оптовикам
в контейнере Биг-Бег - договорная +скидка оптовикам
В зависимости от обьемов закупки и условий оплаты предоставляются значительные скидки!!!
Порошок минеральный для асфальтобетонных смесей неактивированный.
№ |
Наименование показателя |
Норма |
1 |
Массовая доля влаги, % не более |
1,0 |
2 |
Зерновой состав, % по массе |
|
Мельче 1,25 мм |
100 |
|
Мельче 0,315 мм |
От 90 до 95 |
|
Мельче 0,071 мм |
От 70 до 80 |
|
3 |
Пористость, % не более |
30-35 |
4 |
Гидрофобность |
|
5 |
Набухание образцов из смеси порошка с битумом, % не более |
1,8-2,5 |
6 |
Удельная эффективная активность естественных радионуклеидов, Бк/кг не более |
27 |
Объем отгрузки самовывозом - от 1 тонны,
доставка минерального порошка от 50 тонн!
Отгрузка производится ежедневно (без выходных и праздничных дней) с 8.00 до 20.00 часов МСК.
Готовы предоставить образец продукции, контактный телефон для получения образца: 8-920-902-33-33 (г. Москва), 8-930-031-01-33 (Владимирская область)
Способы отгрузки:
Самовывоз - автотранспорт Покупателя (Владимирская обл., Судогодский район, п. Андреево)
Ж.Д.отгрузка - станция Нерудная Горьковская Ж.Д.(Хопперы-цементовозы, п/вагоны Покупателя, либо Перевозчика - собственные, либо арендованные).
В случае вашей заинтересованности готовы обсудить любые вопросы о дальнейшем взаимовыгодном сотрудничестве.
Минеральный порошок – один из самых востребованных видов продукции в дорожном строительстве на сегодняшний день. Он выступает в роли важнейшего компонента асфальтобетонных смесей и придаёт им необходимые характеристики. У нас вы сможете приобрести лучшие минеральные порошки для дорожно-строительных работ.
В составе бетона и асфальтобетона этот продукт выступает в качестве заполнителя и усилителя свойств, поскольку повышает клейкость и вязкость битума. Благодаря своему составу и своей структуры, порошок впитывает нефтяной битум в себя, и результатом такой реакции становится привычный нам клейкий, вязкий и быстро схватывающийся состав – бетон или асфальтобетон.
Классификация минерального порошка ведётся в основном по одному ключевому признаку – по его происхождению. Так, минеральный порошок МП-1 считается более качественным, поскольку производится из первичного сырья – например, карбонатных пород. Именно такой минеральный порошок мы производим и предлагаем приобрести.
Поскольку в последнее время дорожное строительство во многих городах идёт полным ходом, то все компоненты асфальтобетонных смесей пользуются популярностью и широким спросом. Очень важно понимать, почему вам предлагается приобретать именно качественный минеральный порошок. ГОСТ определяет эту продукцию как пористую на 30 – 35%, гидрофобную, со стопроцентным составом зёрен мельче 1,25 мм.
Наши минеральные порошки соответствуют ГОСТу, так что вы можете не сомневаться в их качестве. На основе наших порошков получаются самые лучшие асфальтовые и асфальтобетонные смеси. Транспортировка осуществляется специальным автотранспортом. Позаботьтесь о том, чтобы обеспечить надёжное хранение минерального порошка, предохраняйте от попадания влаги и сторонних примесей. Тогда вы сможете использовать наши минеральные порошки по назначению и создать лучшие смеси для дорожно-строительных работ.
Минеральный порошок (известняковый) неактивированный марки МП-1 ГОСТ Р 52129-2003
Минеральный порошок МП-1 неактивированный ГОСТ Р 52129-2003 - каменная мука, пыль, ключевой материал при строительстве дорог. Порошок минеральный является важной активной структурной составной частью асфальтобетона. Благодаря своей развитой поверхности, адсорбирующей на себя большую часть битума, минеральный порошок придаёт асфальтобетону необходимые свойства, т.е. механическую прочность, способность к упругим и пластическим деформациям, что существенно улучшает качества дорожного покрытия, увеличивает срок его службы и дает значительную экономию при эксплуатации. Срок годности минерального порошка не ограничен. Производство минерального порошка основано на дроблении и тонком измельчении известняков и доломитов, а так же твёрдых отходов промышленного производства. Основная область применения минерального порошка – изготовление искусственного асфальта на асфальтобетонных заводах, где минпорошок служит в качестве заполнителя, повышающего вязкость и клеящую способность битума.
Минеральный порошок, благодаря адсорбирующей поверхности поглощает в себя существенную часть нефтяного битума, придавая асфальтобетону требуемые характеристики: прочность и устойчивость к деформациям. Благодаря этому, качество получаемого асфальтобетона, а по сути и всего будущего дорожного покрытия, существенно повышается.
Минеральный пророшок производится в соответствии с ГОСТ 512129-2003 Стандарт распространяется на активированные и не активированные минеральные порошки, изготовляемые из известняков, доломитов, доломитизированных известняков и других карбонатных горных пород и применяемые для производства асфальтобетонных смесей. Стандарт не распространяется на минеральные порошки, получаемые из некарбонатных пород и порошкообразных отходов промышленности (пыль уноса цементных заводов и золы уноса ТЭЦ), используемых в качестве минеральных порошков для асфальтобетонных смесей, как это указано в ГОСТ 9128-76.
Паспорт качества
Зерновой состав, % по массе: мельче 1.250 мм 0.315 мм 0.071 мм |
100 95 80 |
Пористость, в % | 16,6 |
Набухание образцов из смеси порошка с битумом | 1,0 |
Показатель битумоемкости, % | 56,3 |
Влажность, % по массе | 0,5 |
Истинная плотность, гр/м3 | 2,71 |
Средняя плотность, гр/м3 | 2,26 |
Минеральный порошок для асфальтобетонных и органоминеральных смесей ГОСТ Р 52129-2003
Насыпью -
Железнодорожным транспортом:
- хоппер-цементовоз (загрузка 57 т).
Автотранспорт (самовывоз).
Фасовка (полипропиленовый клапанный мешок) -
Железнодорожным транспортом:
- крытый вагон (загрузка 64 т).
Автотранспорт (самовывоз).
Наши партнеры
ЗАО «Коккомякки»
ЗАО «КП-Габбро»
ЗАО «Карьер «Голодай Гора»
ООО «Дорпромгранит»
ООО «Прионежский габбро-диабаз»
ООО «Карелприродресурс»
ОАО «Ленстройматериалы-Техностром»
ООО «ОСТгранит»
ООО «Карелинвест»
ООО «Евро-цемент»
ООО «Муезерский гранит»
Наши клиенты
ЗАО «Инжтрансстрой»
ООО «Аэродром Трансстрой»
ООО «Трансстройинвест»
ООО «Инертсервис»
ООО «РР- 1»
ООО «Евро-Строй»
ООО «Алнстрой-тротуар»
ООО «Торговый дом «Цемент»
ООО «Эталон»
ООО «Речная торговая компания»
ООО «Баррикада»
ЗАО «БУЕР»
ООО «СМУ-115»
ЗАО «АБЗ-Магистраль»
ООО «ТК-Технострой»
ООО «Штрабаг»
ООО «Лемминкяйнен»
ОАО «Силовые машины Завод «Электросила»
Методика подбора состава асфальтобетонной смеси. Расчет состава асфальтобетонной смеси Подбор гранулометрического состава асфальтобетонной смеси тяжелой
Состав асфальтобетонной смеси подбирается в соответствии с заданием, составленным на основании проекта дороги. Задание определяет вид, вид и марку асфальтобетонной смеси, а также конструктивный слой дорожной одежды, для которого она предназначена. Подбор состава асфальтобетонной смеси включает испытания и по их результатам подбор составляющих материалов, а затем установление между ними рационального соотношения, обеспечивающего получение асфальтобетона со свойствами, соответствующими требованиям стандарта. .Минеральные материалы и асфальты испытывают в соответствии с действующими стандартами, а после всего комплекса испытаний определяют пригодность материалов для асфальтобетонной смеси заданного типа и марки в соответствии с положениями ГОСТ. Рациональное соотношение между составляющими материалами начинается с расчета гранулометрического состава. Минеральный состав смесей крупнозернистого и мелкозернистого асфальтобетона при наличии крупного или среднего песка и дробящих грохотов рекомендуется подбирать по сплошному зерновому составу, при наличии природного мелкозернистого песка - по прерывистому. состав, где щебеночный или гравийный каркас заполнен смесью, практически не содержащей зерен размером 5 - 0,63 мм.
Минеральный состав горячих и теплых песчаных смесей и всех видов холодных асфальтобетонных смесей выбирают только по сплошному зерновому составу. Для удобства расчетов рекомендуется использовать предельные кривые размера зерна, построенные в соответствии с требованиями ГОСТ (рис.). Смесь щебня (гравия), песка и минерального порошка подбирают таким образом, чтобы кривая гранулометрического состава располагалась в зоне, ограниченной граничными кривыми, и была максимально плавной.При подборе зернового состава смесей на дробленых песках и гравийном щебне, а также материалов из грохотов дробления горных пород, характеризующихся высоким содержанием мелких зерен (мельче 0,071 мм), количество последних в общем составе минерального порошка следует принимать во внимание. При использовании материалов из грохотов изверженных пород допускается полная замена минеральной муки их тонкодисперсной частью в смесях для плотных горячих асфальтобетонов III класса, а также в смесях для пористых и высокопористых асфальтобетонов марки.I и II. В смесях для горячего, теплого и холодного асфальтобетона I и II классов допускается только частичная замена минерального порошка; при этом масса зерен мельче 0,071 мм, содержащихся в смеси, должна содержать не менее 50 % известнякового минерального порошка, соответствующего требованиям ГОСТ
При использовании материалов из отсевов дробления карбонатных пород в составе горячих и теплых смесей для плотных асфальтобетонов II и III марок, а также холодных смесей маркиI и II, и смесей для пористого и высокопористого асфальтобетона I и II, минеральный порошок допускается не использовать, если содержание в ситах зерен мельче 0,071 мм обеспечивает соответствие зернового состава требованиям ГОСТ, а свойства зерен мельче 0,315 мм в отсевах соответствуют требованиям ГОСТ на минеральный порошок. Рис. Сплошной зерновой состав минеральной части горячих и теплых мелкозернистых (а) и песчаных (б) смесей плотного асфальтобетона, используемых в верхних слоях дорожной одежды.
При применении продуктов дробления полиминерального гравия в асфальтобетоны в дорожно-климатических зонах IV-V также не допускается внесение минерального порошка в асфальтобетонные смеси II марки, если масса зерен мельче 0,071 мм содержит не менее 40 % кальция и карбонаты магния (CaCO3 + MgCO3). В результате подбора зернового состава определяется весовое процентное соотношение между минеральными компонентами асфальтобетона: щебнем (гравием), песком и минеральной мукой.Содержание битума в смеси выбирают заранее в соответствии с рекомендациями приложения 1 ГОСТ и с учетом требований стандарта на величину остаточной пористости асфальтобетона для конкретного климатического района. Так, в дорожно-климатических зонах IV-V допускается применять асфальтобетон с более высокой остаточной пористостью, чем в I-II, поэтому содержание битума в асфальтобетоне для этих зон назначают ближе к нижним рекомендуемым пределам, а в I -II - к верхним.
В лаборатории готовят три образца из асфальтобетонной смеси с выбранным количеством битума и определяют: среднюю плотность асфальтобетона, среднюю и фактическую плотность минеральной части, пористость минеральной части и остаточную пористость асфальтобетона по ГОСТ. Если остаточная пористость не соответствует выбранной, необходимое содержание рассчитывается исходя из полученных свойств асфальтобетона В (%) по формуле: В, где V°поп - пористость минеральная часть, % по объему; Vпор - выбранная остаточная пористость, % к объему, принимается по ГОСТу для данного климата и дорожной зоны; ГБ - фактическая плотность битума, г/см 3 ; гб = 1 г/см3; r°m - средняя плотность минеральной части, г/см 3 .
После расчета необходимого количества битума снова готовят смесь, изготавливают из нее три образца и определяют остаточную пористость асфальтобетона. Если остаточная пористость совместима с выбранной, принимается расчетное количество битума. Лаборатория готовит асфальтобетонную смесь с выбранным составом: крупнозернистая кг, мелкозернистая кг и песчаная кг. Из смеси изготавливают образцы и определяют соответствие их физико-механических свойств ГОСТу.Если асфальтобетон выбранного состава не соответствует требованиям стандарта по некоторым показателям, например, прочности при 50°С, рекомендуется увеличить (в допустимых пределах) содержание минерального порошка или использовать битум с более высоким вязкость; при неудовлетворительных показателях прочности при 0°С следует уменьшить содержание минерального порошка, уменьшить вязкость битума или добавить полимерную добавку.
При недостаточной водонепроницаемости асфальтобетона целесообразно увеличить содержание минерального порошка или битума; с другой стороны, остаточная пористость и пористость минерального основания должны оставаться в пределах, указанных в вышеупомянутом стандарте.Поверхностно-активные вещества и активированные минеральные порошки наиболее эффективны для повышения водостойкости. При определении содержания битума в холодных асфальтобетонных смесях следует принимать дополнительные меры для предотвращения слеживания смеси при хранении. Для этого после определения необходимого количества битума готовят образцы для испытания на слеживаемость. Если показатель слеживаемости превышает требования ГОСТ, содержание битума уменьшают на 0,5% и повторяют испытание.Количество битума следует уменьшать до получения удовлетворительных результатов спекания, однако следить за тем, чтобы остаточная пористость холодного асфальтобетона не превышала требований ГОСТ.После корректировки состава асфальтобетонной смеси выбранную смесь следует испытал снова. Подбор состава асфальтобетонной смеси можно считать законченным, если все показатели свойств образцов асфальтобетона соответствуют требованиям указанного выше ГОСТа.
Пример подбора состава асфальтобетонной смеси Необходимо подобрать состав горячей мелкозернистой асфальтобетонной смеси типа Б II марки для плотного асфальтобетона, предназначенного для устройства верхнего слоя покрытия в автомобильной дороге климатическая зона III.В наличии следующие материалы: - гранитный щебень, фракция 5-20 мм; - известняковый щебень фракции 5-20 мм; - речной песок; - материал из гранитных дробильных грохотов; - материал из грохотов дробления известняка; - неактивированный минеральный порошок; - битум нефтяной марки БНД 90/130 (по паспорту). Характеристики испытанных материалов приведены ниже. Гранитный заполнитель: класс цилиндрической прочности на раздавливание, класс стойкости к истиранию - I-I, класс морозостойкости - Мрз 25, фактическая плотность - 2,70 г/см3; щебень известняковый: класс прочности на раздавливание цилиндрический - 400, класс сопротивления истиранию - I-IV, класс морозостойкости - Мрз 15, фактическая плотность - 2,76 г/см3; песок речной: содержание илистых и глинистых частиц - 1,8 %, глины - 0,2 % по массе, фактическая плотность - 2,68 г/см3; материал из отсевов дробления гранита, сорт1000:
Содержание пылеватых и глинистых частиц - 5 %, глины - 0,4 % по массе, фактическая плотность - 2,70 г/см3; материал из решет известняковых дробилок класса 400: содержание пылеватых и глинистых частиц - 12 %, глины - 0,5 % по массе, фактическая плотность - 2,76 г/см3; неактивированный минеральный порошок: пористость - 33 % по объему, набухание образцов из смеси порошка и битума - 2 % по объему, фактическая плотность - 2,74 г/см3, индекс емкости асфальта - 59 г, влажность - 0,3 % по массе; битум: глубина проникновения иглы при 25°С - 94×0,1 мм, при 0°С - 31×0,1 мм, температура размягчения - 45°С, относительное удлинение при 25°С - 80 см, при 0°С - 6 см, по Фраасу температура хрупкости - минус 18°С, температура вспышки - 240°С, выдерживает сцепление с минеральной частью асфальтобетонной смеси, индекс пенетрации - минус 1.По результатам исследований гранитный щебень можно считать пригодным для приготовления смеси типа Б класса II, речного песка, материала гранитных дробилок, минеральной муки и битума марки БНД 90/130.
Известковый заполнитель и материал из грохотов для дробления известняка не соответствуют требованиям табл. 10 и 11 ГОСТ по прочности. Зерновой состав отдельных полезных ископаемых приведен в таблице. Расчет минеральной части асфальтобетонной смеси начинают с определения соотношения масс щебня, песка и минеральной муки, при котором гранулометрический состав смеси этих материалов удовлетворяет требованиям табл.6 Таблица ГОСТ
Расчет количества щебня По ГОСТ и рис. 2, а содержание частиц щебня крупнее 5 мм в асфальтобетонной смеси типа Б составляет 35-50%. При этом принимаем содержание щебня Ш = 48%. Так как зерен крупнее 5 мм в щебне содержится 95%, потребуется щебень Ш = Полученное значение заносим в таблицу. 7 и рассчитать содержание в щебеночной смеси каждой фракции (брать по 50 % от количества каждой фракции щебня).Расчет количества минерального порошка по ГОСТу и рис. 2, а содержание частиц мельче 0,071 мм в минеральной части асфальтобетонной смеси типа Б должно быть в пределах 6-12%. Для расчетов принимаем содержание частиц, например, ближе к нижнему пределу требований, т.е. 7%. Если количество этих частиц в минеральном порошке 74 %, то содержание минерального порошка в смеси равно MP =
Однако для наших условий следует брать 8% минерального порошка, так как в песке и материале гранитных решеток уже имеется небольшое количество частиц мельче 0,071 мм.Полученные данные заносят в таблицу 7 и рассчитывают содержание минерального порошка каждой фракции (берут 8%). Расчет количества песка каждого из них в отдельности. Соотношение речного песка Пр и гранитного отсева можно определить по содержанию в них зерен мельче 1,25 мм, что согласно ГОСТ и рис. 2, а в асфальтобетонной смеси типа Б должно быть 28-39%. Мы принимаем 34%; из которых 8%, как рассчитано выше, составляют долю минерального порошка. Тогда доля песка остается 34-8=26% зерен мельче 1,25 мм.Учитывая, что массовая доля таких зерен в речном песке составляет 73 %, а в материале из гранитных дробильных грохотов - 49 %, для определения массовой доли речного песка в минеральной части асфальтобетонной смеси дополним пропорция:
Для расчетов принимаем Pr = 22%; тогда количество материала с отсева гранитного дробления будет = 20%. Рассчитав, как и в случае со щебнем и минеральной мукой, количество отдельных фракций в песке и материале, из отсевов гранитного щебня, полученные данные заносим в таблицу.7. Суммируя количество частиц мельче заданного размера в каждом вертикальном столбце, получаем общий гранулометрический состав смеси минеральных материалов. Сравнение полученного состава с требованиями ГОСТ показывает, что он им соответствует. Аналогично рассчитываем минеральную часть асфальтобетонной смеси с прерывистым зерновым составом. Определение содержания битума Щебень, песок, гранитные грохоты и минеральный порошок смешивают с 6% битума. Это количество битума является средним, рекомендуемым при применении.1. ГОСТ для всех дорожных и климатических зон. Из полученной смеси готовят три образца диаметром и высотой 71,4 мм.
Поскольку щебня в асфальтобетонной смеси содержится 50 %, то уплотнение смеси производится комбинированным способом: вибрация на виброплощадке в течение 3 минут под нагрузкой 0,03 МПа (0,3 кгс/см 2 ) и дополнительное уплотнение на прессе до 3 минут под нагрузкой 20 МПа (200 кгс/см 2 ). Через ч определяют среднюю плотность (насыпную плотность) асфальтобетона (образцов), определяют фактическую плотность минеральной части асфальтобетона (r°) и по этим данным определяют среднюю плотность и пористость минеральной части образцов рассчитываются.Зная реальную плотность всех материалов и выбрав остаточную пористость асфальтобетона Vпор = 4% по ГОСТ, рассчитывают примерное количество битума. Средняя плотность испытанных образцов асфальтобетона с содержанием битума 6,0 % (более 100 % минеральной части) составляет 2,35 г/см3.
Г/см3; Из контрольной смеси с содержанием битума 6,2 % были изготовлены три образца и определена остаточная пористость. Если она находится в пределах 4,0±0,5 % (как это было обычно для мелкозернистого асфальтобетона из смесей типа Б), готовят новую смесь с таким же количеством битума, формируют 15 образцов и испытывают их по требованиям ГОСТ. (по три образца для каждого вида испытаний).Если параметры свойств образцов, приготовленных из выбранной смеси, отклоняются от требований ГОСТ, необходимо скорректировать состав смеси и провести повторное испытание.
Зерновой состав минеральной части асфальтобетонных смесей и асфальтобетонов должен соответствовать приведенному в таблице. Показатели физико-механических свойств асфальтобетона, применяемого в определенных дорожно-климатических зонах, должны соответствовать указанным в таблице.
90 100
90 120
90 132
90 140
Состав, рецептура и свойства Объективная оценка пригодности порошка для использования в асфальтобетоне возможна только на основании результатов испытаний, проведенных на образцах асфальтобетона.Учет этого важного обстоятельства позволяет использовать в некоторых видах литого асфальтобетона даже неадекватные порошки, такие как лёсс, молотый мергель, гипс или гипс, отходы фильтр-прессов сахарной промышленности, отходы содовых заводов, феррохромные шлаки и др. Песок играет важную технологическую и экономическую роль в производстве асфальтобетонных смесей. При выборе песка предпочтительнее природный песок. Чем плотнее и крупнее зерно, тем подвижнее и плотнее минеральная смесь и тем меньше требуется битума.В отличие от минерального порошка, большинство природных морских, речных и озерных кварцевых песков не вступают в химическую реакцию с битумом. Для большинства литейных смесей можно рекомендовать пески, соответствующие требованиям стандарта и табл.
90 160
Состав, рецептура и свойства Не рекомендуется применять дробильные грохоты, содержащие повышенное количество пылевидных частиц, для смесей I и II типов во избежание ухудшения подвижности смесей и увеличения расхода асфальта.Дробленые пески рекомендуется использовать только как добавку к природному окатанному песку при производстве смесей I и II типа. в чистом виде их можно использовать только в смесях типов III, IV и V. Практически все свойства литого асфальтобетона значительно улучшаются при добавлении в затравочную смесь 3-5 мм фракции труднополируемых пород . Соотношение фракции 3-5 мм и фракции 5-10 в смеси следует принимать как 2:1 или 1,5:1. Щебень (гравий) в случае смесей, отлитых из заполнителя (гравия), должен соответствовать требованиям и табл.3. Не рекомендуется использовать щебень, полученный дроблением слабых (классы дробления ниже 600) и пористых горных пород. Пористый щебень быстро впитывает битум, и для обеспечения необходимой подвижности смеси содержание битума следует увеличить.
Состав, рецептура и свойства. Смеси для поверхностного слоя требуют использования плотного труднополируемого скального щебня кубической формы размером не более 15 (20) мм.При этом для смесей I типа рекомендуется дробить фракции 3-15 с соотношением размеров частиц 3-5, 5-10 и мм как 2,5:1,5:1,0. Для смесей V типа максимальный размер зерна может достигать 20 мм, а для III типа – 40 мм. В последнем случае прочность исходной породы может быть снижена на %.
90 170
Состав, рецептура и свойства Без особого ущерба для асфальтобетона из смесей типов II, III и V, но с высокой производственной выгодой, можно снизить требования к дроблению зерен щебня.Дробление зерен в этих асфальтобетонных смесях маловероятно, так как формирование структуры в монолит происходит под действием силы тяжести или вибрации и без тяжелых катков. Гравий можно успешно использовать в литейных смесях типа II, III и V. Благодаря округлой форме и очень кислому характеру поверхности зерна смесь обладает повышенной подвижностью при меньшем расходе битума. Асфальт определяет фазовый состав битумного вяжущего в асфальтобетоне, претерпевает наибольшие изменения по сравнению с другими компонентами смеси, влияет на теплостойкость дорожной одежды.Поэтому в основном ориентируются на клейкие виды со свойствами, указанными в таблице. 4.
Состав, рецептура и свойства Если битум не обладает комплексом этих свойств, его улучшают добавлением природного битума, битуминозных пород, эластомеров и др. К высокоэффективным добавкам относится природный битум, который хорошо совместим с сырой нефтью и удобен в применении. . Природные асфальты создавались из сырой нефти в верхних слоях земной коры в результате выпадения легких и средних фракций - естественной деасфальтизации сырой нефти, а также процессов взаимодействия ее компонентов с кислородом или серой.В нашей стране природные асфальты встречаются в различных битуминозных породах и редко бывают в чистом виде. Состав, рецептура и свойства Битумные отложения встречаются в виде пластов, линз, прожилок и на поверхности. Наибольшее количество битумов содержится в слоистых и линзовидных отложениях. Жильные месторождения в нашей стране встречаются редко. Значительное количество природных битумов находится в поверхностных отложениях. По своему химическому составу эти битумы аналогичны нефтяным битумам. Природный битум бывает твердым, липким и жидким.Твердые битумы (асфальтиты). Плотность битума кг/м3, температура размягчения °С. Битум содержит в среднем 25% масел, 20% смол и 55% асфальтенов. Асфальтиты обладают повышенными адгезионными свойствами за счет высокого содержания в их составе природных ПАВ – асфальтогеновых кислот и их ангидридов. Битум устойчив к старению под воздействием солнечной радиации и кислорода воздуха.
Состав, рецептура и свойства. Положительные результаты получены при добавлении в литейную смесь измельченного полиэтилена и порошка тонкоизмельченного каучука (ТИРП) в количестве 1,5% по массе.минеральные материалы. В качестве добавки, повышающей термостойкость мастичного асфальтобетона, рекомендуется использовать серу дегазированную в комковом, гранулированном (размер гранул до 6 мм) или жидком виде. Сера вводится в смеситель для горячих минеральных материалов, т. е. до подачи битума. Количество серы назначается в пределах 0,25-0,65 от содержания битума. При этом количество битума с серой составляет 0,4-0,6 от содержания минерального порошка.
Состав, рецептура и свойства Подводя итог сказанному, следует помнить, что большая часть упомянутых «ноу-хау» требует преодоления серьезных технических и технологических проблем, а также дополнительных финансовых затрат, которые не все организации могут решить.Увеличивая себестоимость продукции, они не всегда улучшают технологические свойства смесей и эффективность покрытия, а также здоровье людей и окружающую среду. Рецепт смесей рекомендуется подбирать по специальной методике. Расчет содержания компонентов начинают после определения гранулометрического состава всего минерального сырья и построения кривой рассева. Кривая должна находиться в рекомендуемых пределах для данного типа смеси. 53 Состав, рецептура и свойства Если кривая просеивания выходит за рекомендуемые пределы, следует отрегулировать содержание отдельных зерен, изменив их количество в минеральной смеси.При расчете количества минерального порошка следует делать поправку на содержание песчаной пыли и щебня в минеральной смеси. При этом вслед за численными значениями фазового состава асфальтового вяжущего (Б/МП) и его количества (Б+МП) для соответствующего вида литейной смеси вводят дозу битума (полимерного битума или другого битумного вяжущего). и определяются имущественные показатели. Основными показателями свойств образцов литой смеси и асфальтобетона, при заданных значениях которых подобран состав, являются следующие виды: I и V - подвижность, глубина полости пуансона и водонасыщенность; II - подвижность, прочность на сжатие при температуре +50°С и глубине полости пуансона; III - подвижность и водонасыщенность; IV - водонасыщение и прочность на сжатие при +50°С.
Компоненты, состав и свойства Необязательные предел прочности при растяжении и модуль упругости при изгибе при 0°С и коэффициент трещиностойкости определяются как отношение значений указанных показателей. При полном соответствии свойств смеси и асфальтобетона требуемым (таблица) выбор считается успешным. Таблица – Физико-механические свойства литого асфальтобетона
Асфальт, наиболее широко используемый в строительстве дорог в 20 веке, делится на множество видов, видов и типов.В основе разделения лежит не только и не столько перечень исходных компонентов, содержащихся в асфальтобетонной смеси, сколько соотношение их массовых долей в составе, а также некоторые особенности компонентов - в частности размер фракции песка и щебня, степени очистки минерального порошка и все того же песка.
Асфальтовая композиция
Все виды и марки асфальта содержат песок, щебень или гравий, минеральный порошок и битум. Однако, если речь идет о щебне, то его не используют для подготовки некоторых видов дорожных покрытий - но если асфальтирование участков производится с учетом высокой проходимости и сильных кратковременных нагрузок на дорожное покрытие, то щебень необходим камень (или гравий) – как защитный элемент, создающий каркас.
Минеральный порошок - обязательный исходный элемент для приготовления асфальтобетона всех марок и типов. Как правило, массовая доля порошка - а он получается при дроблении горных пород с высоким содержанием углерода (т.е. известняка и других органических ископаемых отложений) - определяется задачами и требованиями к вязкости материала. Большой процент минеральных порошков позволяет использовать его в таких работах, как асфальтирование дорог и площадей: липкий (т.е. прочный) материал успешно гасит внутренние колебания мостовых конструкций, не давая трещин.
Большинство видов и марок асфальта используют песок - исключением, как мы уже сказали, являются виды дорожного покрытия, где массовая доля гравия высокая . Качество песка зависит не только от степени очистки, но и также о способе добычи: песок открытым способом обычно требует тщательной очистки, а вот искусственный песок, полученный дроблением горных пород, считается готовым «к работе».
Наконец, битум является основой индустрии дорожного покрытия.Продукт переработки сырой нефти, битум содержится в смеси любой марки в очень незначительном количестве - его массовая доля в большинстве разновидностей едва достигает 4-5 процентов. Асфальтовая мастика широко используется в таких областях, как асфальтирование в тяжелых условиях бездорожья и дорог, но она содержит 10 и более процентов битума. Битум придает такому полотну большую гибкость после застывания и текучесть, что облегчает растекание готовой смеси на месте.
Асфальты марок и типов
В зависимости от процентного содержания в составе перечисленных компонентов различают три асфальта марки ... Технические характеристики, область применения и состав смеси разных марок описаны в ГОСТ 9128-2009, в котором учтена, в том числе, возможность введения дополнительных добавок, повышающих морозостойкость, гидрофобность, эластичность или износостойкость стойкость покрытия.
В зависимости от процентного содержания наполнителя в дорожно-строительной смеси ее делят на следующие виды:
- А - 50-60% щебня;
- Б - 40-50% щебня или гравия;
- Б - 30-40% щебня или гравия;
- Г - до 30 % песка с грохотов дробления;
- Д - до 70 % песка или смеси с дробящими грохотами.
Битум 1 класс
Под этой маркой выпускается широкий ассортимент различных видов покрытий - от плотных до очень пористых, со значительным содержанием щебня. Сфера их применения - дорожное строительство и благоустройство: только пористые материалы совершенно не подходят на роль собственно покрытия, верхнего слоя земляного полотна. Их гораздо лучше использовать для обустройства оснований, выравнивания грунта для укладки более плотных видов материала.
Битум класса 2
Диапазон плотностей примерно одинаков, но содержание и процентное содержание песка и гравия могут значительно различаться. Это тот же «средний» асфальт, с очень широким спектром применения: без него не обойтись и строительство автомобильных дорог и их ремонт, а также обустройство площадок под автостоянки и дворы.
Битум 3 класса
Покрытия 3 класса отличаются тем, что в них не используется щебень или гравий - их заменяют минеральные порошки, особенно качественный песок, получаемый дроблением твердых пород.
Соотношение песок/гравий
Соотношение песок/гравий является одним из важнейших показателей, определяющих область применения того или иного вида покрытия.В зависимости от распространенности конкретного материала маркируется буквами от А до D: А – более чем наполовину состоит из мелкого щебня или гравия, а Д – около 70%. песок (однако в основном используется песок из щебня).
Соотношение битума и минералов
Не менее важно - ведь именно оно определяет прочностные характеристики дороги. Высокое содержание минеральных порошков значительно увеличивает его хрупкость. Таким образом, песчаный асфальт можно использовать только в ограниченных пределах: парк или тротуар.А вот покрытия с повышенным содержанием битума - желанный гость в любых работах: особенно в дорожном строительстве в сложных климатических условиях, при минусовых температурах, если темп работ такой, что дорожная техника через сутки выйдет на новую дорогу , а когда дорога будет готова, по ним поедут большегрузные автомобили.
Расчет основан на подборе рациональных пропорций между материалами, входящими в состав асфальтобетонной смеси.
Метод расчета плотных смесей по кривым стал обычным явлением.Наибольшая прочность асфальтобетона получается при максимальной плотности минерального скелета, оптимальном количестве битума и минерального порошка.
Существует прямая зависимость между гранулометрическим составом минерального материала и его плотностью. Оптимальными будут составы, содержащие разноразмерные зерна, диаметр которых в два раза меньше размера.
где D 1 - наибольший диаметр зерна, устанавливаемый в зависимости от вида смеси;
D 2 - наименьший диаметр зерна, соответствующий пылевидной фракции и минеральному порошку (0,004... 0,005 мм).
Размер зерна как на предыдущем уровне
(6.6.2)
Количество размеров определяется выкройкой
(6.6.3)
Количество фракций NS На единицу меньше числа размеров T
(6.6.4)
Соотношение смежных фракций по массе
(6.6.5)
, где от до — коэффициент эвакуации.
Величина, показывающая, во сколько раз количество следующей дроби меньше предыдущей, называется коэффициентом выхода.Наиболее плотная смесь получается с коэффициентом скольжения 0,8, но такую смесь трудно выбрать, поэтому по Н.Н. Иванова коэффициент ускользания КО принимался от 0,7 до 0,9.
В России наиболее распространен выбор минерального состава асфальтобетонных смесей по зернограничным кривым. Смесь щебня, песка и минерального порошка подбирают таким образом, чтобы кривая гранулометрического состава располагалась в зоне, ограниченной граничными кривыми, и была максимально плавной.Фракционный состав минеральной смеси рассчитывается в зависимости от содержания выбранных компонентов и их зернового состава по следующей формуле:
j - номер компонента;
n – количество ингредиентов в смеси;
При подборе зернового состава асфальтобетонной смеси, особенно при использовании песка с дробильных грохотов, следует учитывать содержащиеся в минеральном материале зерна размером менее 0,071 мм, которые после нагрева в сушильном барабане выдуваются и оседают в система обеспыливания.
Эти частицы пыли можно удалить из смеси или добавить в смеситель вместе с минеральным порошком. Порядок применения пылеуловителя указывается в технологическом регламенте приготовления асфальтобетонных смесей с учетом качества материала и свойств асфальтобетонной смеси.
При этом в соответствии с ГОСТ 12801-98 определяют среднюю и фактическую плотность асфальтобетона и минеральной части и по их значениям рассчитывают остаточную пористость и пористость минеральной части.Если остаточная пористость не соответствует нормированному значению, рассчитывают новое содержание битума В (мас.%) по следующей формуле:
После расчетного количества битума снова готовят смесь, формируют из нее образцы и снова определяют остаточную пористость асфальтобетона. Если оно соответствует требуемому, за основу берется рассчитанное количество битума. В противном случае процедуру подбора содержания битума повторяют исходя из приближения к нормируемому объему пор в уплотненном асфальтобетоне.
Изготавливают серию образцов из смеси асфальтобетона с определенным содержанием битума стандартным методом уплотнения и определяют весь комплекс показателей физико-механических свойств, предусмотренных ГОСТ 9128-97. Если асфальтобетон по каким-либо показателям не соответствует требованиям стандарта, состав смеси меняется.
При недостаточном коэффициенте внутреннего трения следует увеличить содержание крупного щебня или дробленых зерен в песчаной части смеси.
Для низкой адгезии при сдвиге и прочности на сжатие при 50°С необходимо увеличить содержание минерального порошка (в допустимых пределах) или использовать более вязкий битум. Для высоких показателей прочности при 0°С рекомендуется уменьшить содержание минерального порошка, уменьшить вязкость битума, использовать полимерно-битумное вяжущее или применять пластифицирующие добавки.
При недостаточной водонепроницаемости асфальтобетона целесообразно увеличить содержание минерального порошка или битума, но в пределах, обеспечивающих требуемые значения остаточной пористости и пористости минеральной части.Для повышения водостойкости эффективно использование поверхностно-активных веществ (ПАВ), активаторов и активированных минеральных порошков. Подбор состава асфальтобетонной смеси считается завершенным, если все показатели физико-механических свойств, полученные при испытаниях образцов асфальтобетона, соответствуют требованиям стандарта. Однако в рамках нормативных требований к асфальтобетону рекомендуется оптимизировать состав смеси в сторону повышения функциональных свойств и долговечности укладываемого слоя дорожной одежды.
До недавнего времени оптимизация состава смеси, предназначенной для устройства верхних слоев дорожных одежд, была связана с увеличением плотности асфальтобетона. Поэтому в дорожном строительстве разработаны три метода, которые используются при подборе зерновых составов плотных смесей. Первоначально они назывались:
.- - экспериментальный (немецкий) способ подбора густых смесей, заключающийся в постепенном заполнении одного материала другим;
- - метод кривых, заключающийся в подборе зернового состава, аналогичного математически определяемым "идеальным" кривым плотных смесей;
- - Метод американских стандартных смесей, основанный на проверенных смесях определенных материалов.
Эти методы были предложены около 100 лет назад и получили дальнейшее развитие.
Суть экспериментального метода подбора плотных смесей заключается в постепенном заполнении пор одного материала более крупными зернами и другого, более мелкого минерального материала. На практике смесь выбирают в следующем порядке.
К 100 массовым частям первого материала последовательно добавляют 10, 20, 30 и т. д. массовых частей второго, определяя среднюю плотность после смешения и концентрирования и подбирая смесь с минимальным количеством пустот в уплотненное состояние.
Если необходимо сделать смесь из трех компонентов, в густую смесь двух материалов постепенно добавляют третий материал, причем выбирают также наиболее плотную смесь. Хотя такой подбор плотного минерального основания трудоемок и не учитывает влияние содержания жидкой фазы и свойств битума на уплотнение смеси, он до сих пор используется в экспериментально-исследовательских работах.
Кроме того, экспериментальный метод подбора плотных смесей послужил основой для расчетных методов составления плотных бетонных смесей из сыпучих материалов различной крупности и получил дальнейшее развитие в методах планирования экспериментов.Принцип последовательного заполнения пустот используется в методике проектирования оптимальных составов дорожных асфальтобетонов, в которых используются щебень, гравий и песок любой зернистости.
По мнению авторов исследования, предложенная расчетно-экспериментальная методика позволяет оптимально управлять структурой, составом, свойствами и расходами асфальтобетона. В качестве переменных структурных и управляющих параметров используются:
- - коэффициенты расширения зерен щебня, гравия и песка;
- - объемная концентрация минерального порошка в битумном вяжущем;
- - критерий оптимальности состава, выраженный минимальными суммарными затратами ингредиентов на единицу продукции.
На основе принципа последовательного заполнения пустот в щебне, песке и минеральной муке рассчитан примерный состав смеси для асфальтобетона высокой плотности на основе жидкого асфальта.
Содержание компонентов в смеси рассчитано по результатам установленных значений фактической и насыпной плотности минеральных материалов. Окончательный состав уточняли экспериментально путем совместного дифференцирования содержания всех компонентов смеси с помощью математического планирования эксперимента на симплексе.Состав смеси считался оптимальным, обеспечивающим минимальную пористость скелета минерального асфальтобетона.
Второй способ подбора зернового состава асфальтобетона основан на подборе плотных минеральных смесей, зерновой состав которых близок к идеальным кривым Фуллера, Графа, Германа, Боломея, Талбота-Ричарда, Китта-Пеффа и другие авторы. В большинстве случаев эти кривые представляют собой степенную зависимость требуемого содержания зерен в смеси от их размера.Например, кривая распределения частиц по размерам Фуллера для густой смеси задается следующим уравнением:
D – наибольшая крупность зерна в смеси, мм.
Чтобы стандартизировать гранулометрический состав асфальтобетонной смеси, в современном американском методе проектирования «Superpave» также используются кривые размера зерен максимальной плотности, соответствующие степенному отношению с показателем степени 0,45.
Кроме того, кроме контрольных точек, ограничивающих диапазон зернистости, имеется еще и внутренняя зона ограничения, которая располагается вдоль гранулометрической кривой максимальной плотности между размерами зерен 2,36 и 0,3 мм.Считается, что смеси с гранулометрическим составом вдоль замкнутой зоны могут иметь проблемы с уплотнением и устойчивостью к сдвигу, поскольку они более чувствительны к содержанию битума и становятся пластичными при случайной передозировке органического вяжущего.
Следует отметить, что ГОСТ 9128-76 также определяет для кривых гранулометрического состава плотных смесей пограничную зону между граничными кривыми сплошного и прерывистого гранулометрического состава.На рис. 1 эта область заштрихована.
Рис. 1. - Зерновой состав тонкозернистой минеральной части: 90 202
90 380Однако в 1986 году, когда стандарт был переиздан, это ограничение было снято как неактуальное. Более того, в работе Ленинградского отделения Союза (АОСал) было показано, что так называемые «полупрерывистые» составы смесей, проходящие в ряде случаев через заштрихованную зону, предпочтительнее сплошных из-за меньшей пористости минерала. части асфальтобетона и прерывистых из-за большей устойчивости к расслаиванию.
Известные исследования В.В. Охотина, которые показали, что наиболее плотную смесь можно получить при условии, что диаметр частиц, составляющих материал, уменьшен в 1:16, а их масса 1:0,43. Однако, учитывая тенденцию к расслоению смесей, составленных с таким соотношением крупной и мелкой фракций, было предложено добавлять промежуточные фракции. В то же время масса фракций диаметром в 16 раз меньше не изменится вообще, если пустоты заполнить не только этими фракциями, но, например,фракции с диаметром зерна в 4 раза меньше.
Если при наполнении фракциями с диаметром зерна в 16 раз меньше их содержание по массе было равно 0,43, то при наполнении фракциями с диаметром зерна в 4 раза меньше их содержание должно быть k = 0,67. Если ввести еще одну промежуточную фракцию с диаметром, уменьшающимся в 2 раза, то отношение фракций должно быть k = 0,81. Таким образом, весовое число дробей, которое будет уменьшаться на одну и ту же величину, может быть математически выражено в виде ряда геометрической прогрессии:
.Y1 - количество первой фракции;
k — коэффициент убегания;
n – количество фракций в смеси.
Из полученной прогрессии выводится количественное значение первой дроби:
Таким образом, коэффициентом стекания обычно называют массовое соотношение фракций, размер частиц которых составляет 1:2, т.е. как отношение ближайшего размера ячейки в стандартном наборе сит.
Хотя теоретически самые плотные смеси рассчитываются с коэффициентом стока 0,81, на практике было обнаружено, что прерывистые смеси более плотные.
Это связано с тем, что в представленных теоретических расчетах составления плотных смесей по коэффициенту стекания не учитывается растекание крупных зерен материала более мелкими.Соответственно, П.В. Сахаров отмечал, что положительные результаты в плане увеличения плотности смеси получаются только при постепенном (прерывистом) отборе фракции.
При соотношении размеров смешанных фракций менее 1:2 или 1:3 мелкие частицы не заполняют зазор между крупными зернами, а раздвигают их.
Кривые гранулометрического состава минеральной части асфальтобетона с различными коэффициентами прогиба представлены на рис. 2.
Рис.2. - Гранулометрический состав минеральной части асфальтобетонных смесей с различными коэффициентами стекания: 90 202
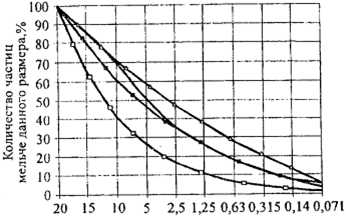
В дальнейшем было определено соотношение диаметров частиц соседних фракций, что исключает рассеяние крупных зерен в многофракционной минеральной смеси. По мнению П.И. Боженова, чтобы исключить растекание крупных зерен через мелкие, отношение диаметра мелкой фракции к диаметру крупной фракции не должно быть больше 0,225 (т.е. 1:4,44).С учетом проверенных на практике составов минеральных смесей Н.Н. Иванов предложил использовать для подбора смесей кривые гранулометрического состава с коэффициентом стекания от 0,65 до 0,90.
Гранулометрический состав плотных асфальтобетонных смесей, ориентированный на удобоукладываемость, был стандартизирован в СССР в 1932-1967 гг. Согласно этим нормам асфальтобетонные смеси содержали ограниченное количество щебня (26-45%) и повышенное количество минерального порошка (8-23%).Опыт применения таких смесей показал, что в дорожных покрытиях возникают волны, сдвиговые и другие пластические деформации, особенно на дорогах с интенсивным и интенсивным движением. В то же время шероховатость поверхности покрытий также была недостаточной для обеспечения высокого сцепления с колесами автомобиля, исходя из условий безопасности дорожного движения.
Существенные изменения в стандарт на асфальтобетонные смеси были внесены в 1967 г. В ГОСТ 9128-67 были включены новые смеси для каркасных асфальтобетонов с повышенным содержанием гравия (до 65%), которые стали предусматривать в проектах дорог с интенсивным движением.В асфальтобетонных смесях также снижено количество минерального порошка и битума, что обосновывалось необходимостью перехода с пластичных смесей на более жесткие.
Минеральный состав многих измельченных смесей был рассчитан с использованием уравнения кубической параболы, связанного с четырьмя контрольными размерами зерен: 20; 5; 1,25 и 0,071 мм.
При испытании и внедрении каркасного асфальтобетона большое значение придавалось повышению шероховатости дорожной одежды.Способы укладки асфальтобетонных покрытий с черновым покрытием нашли отражение в рекомендациях, разработанных в начале 1960-х годов и первоначально внедренных на объектах Главдорстроя Минтранса СССР. По замыслу разработчиков, созданию шероховатости должно было предшествовать формирование пространственного каркаса в асфальтобетоне. На практике это достигается уменьшением количества минеральной пыли в смеси, увеличением содержания крупного дробленого зерна и полным уплотнением смеси, в которой зерна щебеночной и крупной песчаной фракций контактируют друг с другом.Обеспечено производство асфальтобетона с каркасной конструкцией и шероховатой поверхностью с содержанием 50-65% по массе. зерна крупнее 5 (3) мм. в мелкозернистых смесях типа А и 33-55% зерен крупнее 1,25 мм. в песчаных смесях типа Г с ограниченным содержанием минеральной присыпки (4-8% в мелкозернистых смесях и 8-14% в песчаных смесях).
Рекомендации по сопротивлению сдвигу асфальтобетонных покрытий в результате применения каркасного асфальтобетона за счет увеличения внутреннего трения минерального каркаса также встречаются в зарубежных публикациях.
Например, дорожно-строительные компании Великобритании используют специально подобранные составы зерен при устройстве асфальтобетонных покрытий в тропических и субтропических странах по уравнению кубической параболы.
Устойчивость покрытий из таких смесей в основном обеспечивается за счет механического заклинивания угловатых частиц, которые должны представлять собой либо прочный щебень, либо щебень из гравия. Использование неизмельченного гравия в таких смесях не допускается.
Сопротивление деформации сдвигу покрытий может быть увеличено за счет увеличения размера заполнителя. Американский стандарт ASTM D 3515-96 предусматривает разделение асфальтобетонных смесей на девять классов в зависимости от максимального размера зерна от 1,18 до 50 мм.
Чем выше марка, тем крупнее щебень и меньше содержание минерального порошка в смеси. Кривые зернового состава, построенные по кубической параболе, обеспечивают жесткий крупнозернистый каркас при уплотнении покрытия, обеспечивающий основное сопротивление транспортным нагрузкам.
В большинстве случаев минеральную часть асфальтобетонной смеси выбирают из крупных, средних и мелких компонентов. Если фактическая плотность входящих в состав минеральных материалов существенно отличается, рекомендуется их содержание в смеси рассчитывать по объему.
Зерновой состав минеральной части асфальтобетонных смесей, проверенный на практике, нормируется во всех технически развитых странах с учетом сферы их применения.Эти композиции обычно согласуются друг с другом.
Принято считать, что наиболее разработанным элементом проектирования состава асфальтобетона является подбор гранулометрического состава минеральной части либо по кривым оптимальной плотности, либо по принципу последовательного заполнения пор. Ситуация осложняется выбором битумного вяжущего необходимого качества и обоснованием его оптимального содержания в смеси. До сих пор нет единого мнения о достоверности расчетных методов определения содержания битума в асфальтобетонной смеси.
Существующие экспериментальные методы подбора содержания вяжущего предполагают разные способы изготовления и испытания образцов асфальтобетона в лабораторных условиях, а главное, не позволяют достаточно достоверно прогнозировать долговечность и эксплуатационное состояние дорожных одежд в зависимости от условий эксплуатации .
П.В. Сахаров предложил проектировать состав асфальтобетона на основе заранее подобранного состава асфальтобетонного вяжущего. Количественное соотношение битума и минерального порошка в асфальтобетонном вяжущем подобрано экспериментально в зависимости от показателя пластической деформации (метод водостойкости) и предела прочности при растяжении образцов-восьмерок.Также учитывалась термическая стабильность битумного вяжущего путем сравнения показателей прочности при температурах 30, 15 и 0°С. На основании экспериментальных данных было рекомендовано придерживаться весового соотношения асфальта к минеральному порошку (Б/МП) в пределах от 0,5 до 0,2.
В результате асфальтобетонные композиции характеризовались повышенным содержанием минерального порошка. В дальнейших исследованиях И.А. Рыбьев показал, что рациональные значения Б/МП могут быть 0,8 и даже выше.На основании закона оптимальной прочности конструкции (правила выравнивания) рекомендован метод расчета состава асфальтобетона для заданных условий эксплуатации дорожной одежды. Установлено, что оптимальная структура асфальтобетона получается при переводе битума в пленочное состояние.
При этом показано, что оптимальное содержание битума в смеси зависит не только от количественного и качественного соотношения ингредиентов, но и от технологических факторов и способов уплотнения.
Поэтому научное обоснование требуемых эксплуатационных показателей асфальтобетона и рациональных путей их достижения остается основной задачей, связанной с повышением долговечности дорожных покрытий.
Существует несколько методов расчета содержания битума в асфальтобетонной смеси, как по толщине битумного слоя на поверхности минеральных зерен, так и по количеству пустот в уплотненной минеральной смеси.
Первые попытки их применения при расчете асфальтобетонных смесей часто оказывались безуспешными, что вынуждало совершенствовать расчетные методы определения содержания битума в смеси.Н.Н. Иванов предложил учитывать лучшее уплотнение горячей смеси асфальтобетона и определенный запас термического расширения битума, если расчет содержания битума производить исходя из пористости уплотняемой минеральной смеси:
Б - количество битума, %;
P – пористость минеральной уплотненной смеси, %;
с6 - фактическая плотность битума, г/см. молодой;
с - средняя плотность уплотненной сухой смеси, г/см. молодой;
0,85 — коэффициент снижения битума за счет лучшего уплотнения битумной смеси и коэффициента расширения битума, который принимается равным 0,0017.
Следует отметить, что расчет объемного содержания компонентов в уплотненном асфальтобетоне, в том числе объема пор воздуха или остаточной пористости, выполняется любым расчетным методом в виде нормирования объема фаз. В качестве примера на рис. 3 представлен объемный состав асфальтобетона типа А в виде круговой диаграммы.
Рис. 3. - Нормализация фазового объема в асфальтобетоне: 90 202
Согласно этой диаграмме содержание битума (% по объему) равно разнице между пористостью минерального ядра и остаточной пористостью уплотненного асфальтобетона.Так, М. Дюрье рекомендовал метод расчета содержания битума в горячей асфальтобетонной смеси по модулю насыщения. Модуль насыщения асфальтобетона вяжущим определен на основании опытно-производственных данных и характеризует процентное содержание вяжущего в минеральной смеси с удельной поверхностью 1 м2/кг.
Этот метод используется для определения минимального содержания битумного вяжущего в зависимости от гранулометрического состава минеральной части в методе расчета асфальтобетонной смеси LCPC.разработан Центральной лабораторией мостов и дорог Франции. Массовая доля асфальта по этому методу определяется по формуле:
к - модуль пропитки асфальтобетона вяжущим.
- S - частичный остаток на сите с размером отверстий 0,315 мм, %;
- с - частичный остаток на сите с отверстиями 0,08 мм, %;
Методика расчета содержания битума по толщине битумного слоя значительно усовершенствована И.В. Королев. На основании экспериментальных данных он дифференцировал удельную поверхность зерен стандартных фракций в зависимости от характера породы.Показано влияние вида каменного материала, размера зерен и вязкости асфальта на оптимальную толщину асфальтобетонного слоя в асфальтобетонной смеси.
Следующим этапом является дифференцированная оценка битумной емкости минеральных частиц размером менее 0,071 мм. В результате статистического прогноза зернового состава минерального порошка и битумной емкости фракции от 1 до 71 мкм в МАДИ (ГТУ) разработана методика, позволяющая получить расчетные данные, удовлетворительно соответствующие экспериментальному содержанию битума в асфальтобетонная смесь.
Другой подход к определению содержания битума в асфальтобетоне основан на зависимости между пористостью минерального скелета и зерновым составом минеральной части. На основе экспериментальных исследований смесей частиц разного размера японские специалисты предложили математическую модель пористости минерального ядра (ВМА). Значения коэффициентов с установленной корреляционной зависимостью определяли для битого асфальтобетона, уплотняемого на роторном катке (гираторе) при 300 оборотах формы.В работе предложен алгоритм расчета содержания битума, основанный на корреляции поровых свойств асфальтобетона с гранулометрическим составом смеси. По результатам обработки ряда данных, полученных при испытаниях плотных асфальтобетонов различных типов, для расчета оптимального содержания битума были установлены следующие корреляционные зависимости:
К – параметр размера частиц.
Dкр - минимальная крупность крупной фракции, более мелкой, чем содержащаяся в 69,1% массы смеси, мм;
D0 - размер частиц средней фракции, мельче которых содержится 38,1 мас.смеси, мм;
Dfine – максимальный размер зерна мелкой фракции, более мелкой, чем та, которая содержит 19,1 мас.%. смесь, мм.
Однако в любом случае расчетную дозу битума необходимо корректировать при приготовлении контрольных смесей в зависимости от результатов испытаний образцов литого асфальтобетона.
При выборе состава асфальтобетонных смесей учитывается следующее утверждение проф. Н.Н. Иванова: «Асфальта надо брать не больше, чем необходимо для получения достаточно прочной и устойчивой смеси, но асфальта надо брать как можно больше, и ни в коем случае не меньше».Экспериментальные методы подбора асфальтобетонных смесей обычно заключаются в приготовлении эталонных образцов с использованием конкретных методов уплотнения и их испытании в лабораторных условиях. Для каждого метода разработаны соответствующие критерии, устанавливающие в той или иной степени связь между результатами лабораторных испытаний уплотненных образцов и эксплуатационными характеристиками асфальтобетона в условиях эксплуатации.
В большинстве случаев эти критерии определены и стандартизированы национальными стандартами на асфальтобетон.
Распространены следующие схемы механических испытаний образцов асфальтобетона, представленные на рис. 4.
Рис. 4. - Схемы испытаний цилиндрических образцов при проектировании состава асфальтобетона: 90 202
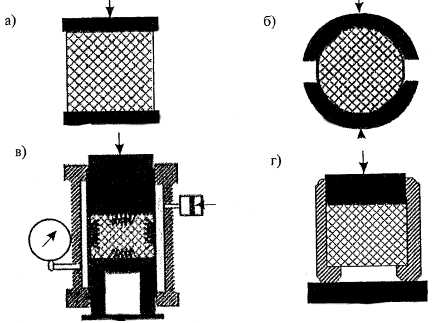
а - по Дюрье;
б - по Маршаллу;
с - по Хвиму;
д - по Хаббард Филду.
Анализ различных экспериментальных методик проектирования асфальтобетонных составов показывает схожий подход к заданию рецептуры и различие как в методах испытаний образцов, так и в критериях оцениваемых свойств.
Подобие методов расчета асфальтобетонной смеси основано на выборе такого объемного соотношения компонентов, которое обеспечивает заданные значения остаточной пористости и нормированные показатели механических свойств асфальтобетона.
В России при проектировании асфальтобетона испытывают стандартные цилиндрические образцы на одноосное сжатие (по схеме Дюрье), которые формируют в лабораторных условиях по ГОСТ 12801-98 в зависимости от содержания заполнителя в смеси либо методом статической нагрузкой 40 МПа или вибрацией с последующим дополнительным уплотнением нагрузкой 20 МПа.В зарубежной практике наибольшее распространение получил метод проектирования асфальтобетонных смесей по Маршаллу.
До недавнего времени в США использовались методы расчета асфальтобетонных смесей по Маршаллу, Хаббард-Филду и Хвиму. но в последнее время многие штаты вводят систему проектирования Superpave.
При разработке новых методов проектирования асфальтобетонных смесей за рубежом большое внимание уделялось совершенствованию методов уплотнения образцов. В настоящее время при конструировании смесей по Маршаллу предусматривают три степени уплотнения образцов: 35, 50 и 75 ударов с каждой стороны соответственно для условий движения легкового, среднего и тяжелого транспорта.Инженерный корпус США в результате обширных исследований усовершенствовал тесты Маршалла и распространил их на проектирование составов дорожного покрытия в аэропортах.
Проект Marshall Asphalt предполагает, что:
- - изначально определено соответствие исходных минеральных материалов и битума требованиям технических условий;
- - подобран гранулометрический состав смеси минеральных материалов, соответствующий проектным требованиям;
- - значения реальной плотности вязких битумно-минеральных материалов определены соответствующими методами испытаний;
- - Сушат и фракционируют достаточное количество каменного материала для приготовления лабораторных смесей с различным содержанием вяжущего.
Для испытаний по Маршаллу изготавливают стандартные цилиндрические образцы высотой 6,35 см и диаметром 10,2 см при уплотнении ударами падающего груза. Смеси готовятся с разным содержанием битума, обычно отличающимся друг от друга на 0,5%. Рекомендуется приготовить не менее двух смесей с содержанием битума выше «оптимального» и две смеси с содержанием битума ниже «оптимального».
Для более точного отнесения содержания асфальта к лабораторным испытаниям рекомендуется сначала установить приблизительное «оптимальное» содержание асфальта.
Под «оптимальным» понимается такое содержание битума в смеси, которое обеспечивает максимальную стабильность по Маршаллу формованным образцам. Для выбора необходимо примерно 22 материала южного камня и около 4 литров. битум.
Результаты испытаний асфальтобетона по методу Маршалла представлены на рис. 5,
На основании теста Маршалла образцов асфальтобетона обычно делаются следующие выводы:
- - Значение стабильности увеличивается с увеличением содержания связующего до определенного максимума, затем значение стабильности снижается;
- - Значение условной пластичности асфальтобетона увеличивается с увеличением содержания вяжущего;
- - Кривая плотность-битумосодержание аналогична кривой устойчивости, однако для нее чаще наблюдается максимум при несколько большем содержании битума;
- - Остаточная пористость асфальтобетона уменьшается с увеличением содержания битума, асимптотически приближаясь к минимальному значению;
- - Процент заполнения пор битумом увеличивается с увеличением содержания битума. 90 237
- - Marshall - 75 ударов с обеих сторон
- - "Суперпейв" - 100 оборотов в гироскопе на 1,25°;
- - MTQ - 80 оборотов в гироскопе на угол 1,25°;
- - LCPC - 60 оборотов эффективного уплотнителя под углом 1°С, получены вполне сопоставимые результаты для оптимального содержания битума.
- Так, для 1-3 климатических зон плотные и плотные АБ изготавливают из заполнителя, класс морозостойкости которого F50. Пористый и очень пористый – из камня класса F 15 и F25.
- Для зон 4 и 5 на основе щебня F 50.производится только горячий асфальт
- Итак, для плотного и плотного песка классов прочности 800 и 1000.В случае пористых она снижается до 400.
- Количество глинистых частиц - диаметром менее 0,16 мм также может регулироваться: для плотных частиц - 0,5%. Для пористых - 1%.
- повышает способность АБ к набуханию и снижает морозостойкость, поэтому этот фактор находится под особым контролем.
- компоненты, специально разработанные и изготовленные для повышения производительности – пластификаторы, стабилизаторы, средства против старения и т. д.
- отходы или вторсырье - сера, гранулированный каучук и так далее. Стоимость таких добавок, конечно, намного ниже.
- Зерновой состав минерала, камня, песка и порошка является основой толщины и шероховатости покрытия. Наиболее распространенным принципом является непрерывная гранулометрия, и только при отсутствии крупнозернистого песка - метод прерывистой гранулометрии. Гранулометрический состав – диаметры частиц и их правильное соотношение должны полностью соответствовать техническим условиям.
- Различные виды асфальта могут образовывать матричную и бескаркасную структуру минерала. В первом случае имеется достаточное количество щебня, чтобы камни соприкасались друг с другом и образовывали в готовом изделии четко выраженную асфальтобетонную структуру. Во втором случае камни и крупинки крупного песка не соприкасаются.Немного условной границей между обеими структурами является содержание щебня в пределах 40–45 %. При выборе следует учитывать этот нюанс.
- Максимальную прочность гарантирует щебень в форме куба или тетраэдра. Этот камень самый прочный.
- О шероховатости поверхности сообщает 50-60% сколов труднополируемых пород или песка из них. Такой камень сохраняет шероховатость своей естественной спайности, что важно для устойчивости асфальта к сдвигу.
- Как правило, асфальт на основе дробленого песка более устойчив к сдвигу, чем песок на основе карьерного песка из-за гладкой поверхности последнего. По тем же причинам долговечность и стойкость материалов на основе гравия, особенно морских, ниже.
- Чрезмерное измельчение извлеченного порошка приводит к увеличению пористости и, следовательно, к износу битума. Это свойство большинства промышленных отходов. Для снижения параметра минеральный порошок активируют – обрабатывают ПАВ и битумом.Эта модификация не только снижает содержание битума, но и повышает водо- и морозостойкость.
- При выборе асфальта учитывайте не только его абсолютную вязкость - чем она выше, тем выше плотность асфальта, но и погодные условия. Так, в засушливых регионах подбирается состав, обеспечивающий максимально низкую пористость. С другой стороны, в холодных смесях количество битума уменьшают на 10-15%, чтобы уменьшить степень слеживаемости.
- Оценка свойств полезных ископаемых и битумов.Это касается не только абсолютных показателей, но и их соответствия конечной цели;
- рассчитать такое соотношение камня, песка и порошка, чтобы эта часть асфальта приобрела максимально возможную плотность; №
- , наконец, рассчитывается количество битума: достаточное для обеспечения требуемых технических характеристик готового продукта на основе выбранных материалов.
- способность повышать резистентность и устойчивость к различным болезням и вредителям;
- повышающие морозо- и засухоустойчивость многолетних растений;
- Снижает вероятность обезвоживания из-за перепадов температуры или жары;
- улучшает качество готовой продукции, а именно вкус, цвет и запах спелых фруктов;
- с помощью калия продлевается срок хранения собранного урожая.
- зеленая окраска листьев становится красноватой или серо-коричневой;
- появляется пожелтение и начинается постепенное обесцвечивание по краям;
- на старых листьях появляются темно-коричневые точечные пятна;
- стебель истончается, перестает расти или наклоняется к земле;
- цветение и бутоны или формирование бутонов задерживаются или прекращаются.
- ГОСТ Р 53590-2009 Майонезы и соусы майонезные. Общие технические условия.
- ГОСТ Р 52141-2003 Кетчупы. Общие технические условия.
- ГОСТ 9159-71 Семена горчицы.
- выбор помещения, отвечающего санитарно-гигиеническим требованиям;
- покупка технологической линии;
- ищем опытного технолога.
- ванны длительной пастеризации с мешалками; (фото ванна) котел
- ; гомогенизатор
- ; (фотогомогенизатор) вакуумная установка
- ; (фото вакуумных установок)
- перекачивающий насос; 90 187 резервуаров для хранения сырья и готовой продукции; (фото накопительных баков)
- дозатор и упаковочный блок.(фото упаковщик) 90 193
- директор - 13 000 руб.;
- главный технолог - 12 000 руб.;
- лаборант - 11 000 руб.;
- закупка сырья и реализация готовой продукции - 9 000 руб.; 90 187 сотрудников 5 линии (по 5 000 руб.) - 25 000 руб.
- Фонд оплаты труда - 70 000 руб.; 90 187 коммунальные расходы - 7 000 руб.; 90 187 аренда производственного корпуса - 10 000 руб.; 90 187 транспортные расходы - 5 000 руб.;
- упаковка для упаковки - 4000 руб. 90 193
- масло растительное - 25% (30 руб. за 1 л) - 7,5 руб.; 90 187 яиц (яичный порошок) - 20% (30 руб. за 10 шт.) - 6 руб.;
- вода, сахар и соль - 46% (20 руб. за 1 кг) - 9,20 руб.;
- кислота уксусная - 3% (35 руб. за 1 л) - 1,05 руб.; 90 187 специй 6% - (80 руб. за 1 кг) - 4,80 руб. 90 193
- валовой доход - 231 000 руб.; 90 187 себестоимость - 43 967 руб.; 90 187 валовая прибыль - 187 033 руб.; 90 187 ежемесячных постоянных затрат - 96 000 руб./3 вида продукции = 32 000 руб.; 90 187 чистая прибыль (15%) - 131 778 руб.
- Рентабельность продаж - 57%.
- концентрат томатный концентрированный 28% (100 руб./кг) - 28 руб.;
- сахар 10% (30 руб./кг) - 3 руб.;
- вода 42% - 0 руб.; 90 187 сушеных овощей 9% (100 руб./кг) - 9 руб.; специи 90 187 - 4% (120 руб./кг) - 4,80 руб.; соль
- - 7% (10 руб/кг) - 0,70 руб. 90 193
- валовой доход - 214 500 руб.; 90 187 себестоимость - 75 075 руб.; 90 187 валовая прибыль - 139 425 руб.; 90 187 чистая прибыль (15%) - 123 539 руб.;
- Рентабельность продаж - 57%.
- вода 60% - 0 руб. 90 187 семян горчицы 15% (90 руб./кг) - 13,50 руб.;
- перец 2% (150 руб./кг) - 3 руб.;
- куркума 2% (125 руб./кг) - 2,50 руб.; соль
- 1% (10 руб./кг) - 0,10 руб.;
- белый уксус 20%. (160 руб./л) - 32 руб.
- валовой доход - 75 000 руб.; 90 187 себестоимость - 25 550 руб.; 90 187 валовая прибыль - 49 450 руб.; 90 187 ежемесячных постоянных затрат – 32 000 руб.; 90 187 чистая прибыль (15%) - 14 832 руб.
- Рентабельность продаж - 19%.
- скидка на товары, подлежащие самовывозу; 90 187 денежных премий дилерам (продавцам) за их усилия по продвижению изделий из теста.
- Портландцемент.
- Шлаковый цемент.
- Пуццолан.
- Белый тип цемента.
- Гидрофобный.
- Магнезиальный.
- Специальный (кислотостойкий, цветной).
- При возведении железобетонных изделий подземных, надземных и подводных сооружений.
- В промышленном и сельскохозяйственном строительстве.
- При производстве фундаментов, балок.
- М500 Д0 – смесь без примесей и добавок.Используется в промышленном строительстве.
- М500 Д20, в данном случае содержание присадок 20%. Этот вид цемента используется для ремонтно-строительных работ..
- Растворы кладочные.
- Штукатурный раствор.
- Строительные цементные растворы.
- Высокая водостойкость.
- Высокая морозостойкость.
- Высокопрочные индикаторы.
- При усадке скорость изменения деформации низкая.
- Высокая устойчивость к длительному воздействию низких температур.
- Водостойкость цемента показатель влияния воды на конкретную марку, каждый цемент впитывает влагу, для каждой марки существует определенный стандарт
- Твердение Время твердения каждого марка тоже бывает разная, она зависит от чистоты и качества глинистых пород, чем выше марка, тем быстрее идет процесс.
- Прочность цемента определяют с помощью готовых бетонных блоков обязательно одинакового объема на сжатие до их полного разрушения.От этого зависит, какую нагрузку выдержит бетон..
- В любом цементном порошке есть допустимое количество примесей по ГОСТу, это сделано с целью удешевления готовой продукции.
- Цемент также содержит опасные химические вещества, такие как хром, никель, бензол, этилбензол, формальдегид ..
Рис. 5. - Результаты (а, б, в, г) испытаний асфальтобетона по методу Маршалла: 90 202
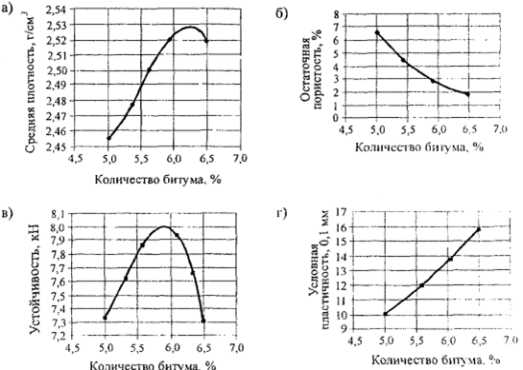
Рекомендуется определять оптимальное содержание битума как среднее из четырех значений, нанесенных на график относительно соответствующих проектных требований. Асфальтовая смесь с оптимальным содержанием битума должна соответствовать всем требованиям технических условий. При окончательном выборе состава асфальтобетонной смеси также могут учитываться технико-экономические показатели.Обычно рекомендуется выбирать смесь с самой высокой стабильностью по Маршаллу.
Однако следует помнить, что смеси со слишком высокими значениями стабильности по Маршаллу и низкой пластичностью нежелательны, поскольку покрытия из таких смесей будут чрезмерно твердыми и могут растрескиваться при движении большегрузных автомобилей, особенно при хрупких основаниях и больших прогибах. Метод расчета асфальта Маршалла часто подвергается критике в Западной Европе и США. Отмечено, что ударное уплотнение образцов по Маршаллу не имитирует уплотнение смеси в дорожной одежде, а устойчивость по Маршаллу не позволяет дать удовлетворительную оценку прочности асфальтобетона на сдвиг.
Критикуется также метод Хвеема, к недостаткам которого можно отнести довольно громоздкое и дорогое испытательное оборудование.
Кроме того, в этом методе не раскрываются должным образом некоторые важные показатели объема асфальтобетона, связанные с его долговечностью. По мнению американских инженеров, метод подбора содержания битума по Хвиму субъективен и может привести к хрупкости асфальтобетона из-за определения низкого содержания вяжущего в смеси.
Метод LCPC (Франция) основан на том факте, что горячую асфальтовую смесь необходимо проектировать и уплотнять до максимальной плотности во время строительства.
Поэтому были проведены специальные испытания расчетной производительности уплотнения, которая определялась как 16 проходов катка с пневматическими шинами, с нагрузкой на ось 3 тс при давлении в шинах 6 бар. На полноразмерном лабораторном стенде при уплотнении горячей асфальтобетонной смеси была обоснована нормативная толщина слоя, равная 5 максимальным размерам минеральных зерен. Для правильного уплотнения лабораторных образцов угол поворота на лабораторном компакторе (гираторе) был нормирован на 1° и вертикальное давление на уплотняемую смесь 600 кПа.При этом стандартное число оборотов гиратора должно быть равно толщине слоя уплотняемой смеси, выраженной в миллиметрах.
В американской системе проектирования Superpave принято уплотнять образцы асфальтобетона также в гираторе, но с углом поворота 1,25°. Работы по уплотнению образцов асфальтобетона нормируют в зависимости от расчетного значения общей транспортной нагрузки дорожной одежды, для устройства, на которое рассчитана смесь.Схема уплотнения образцов из асфальтобетонной смеси в роторном уплотнителе представлена на рис. 6,
Рис. 6. - Схема уплотнения образцов из асфальтобетонной смеси в роторном уплотняющем устройстве: 90 202
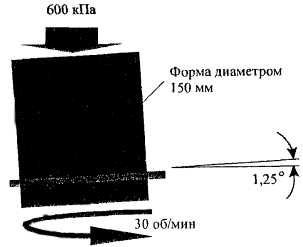
Метод проектирования асфальта MTQ (Министерство транспорта Квебека, Канада) использует роторный уплотнитель Superpave вместо гиратора LCPC. Расчетное число оборотов уплотнения принято для смесей с максимальным размером зерна 10 мм.равным 80, а для смесей с размером частиц 14 мм. - 100 оборотов вращения. Расчетное содержание воздушных отверстий в образце должно быть в пределах от 4 до 7%. Номинальный объем пор обычно составляет 5%. Эффективный объем асфальта определяется для каждого типа смеси аналогично методу LCPC.
Стоит отметить, что при расчете асфальтобетонных смесей из одних и тех же материалов методами Маршалла, методом LCPC (Франция), методом расчетной системы Superpave (США) и методом MTQ (Канада) получены примерно одинаковые результаты.
Несмотря на то, что каждый из четырех методов имел разные условия концентрирования образцов:
Таким образом, авторы исследования пришли к выводу, что важно иметь не «правильный» метод уплотнения лабораторных образцов, а систему влияния силы уплотнения на структуру асфальтобетона в образце и его производительность на асфальте.
Следует отметить, что роторные способы уплотнения образцов асфальтобетона также не лишены недостатков. При уплотнении горячей асфальтобетонной смеси в гираторе обнаружено значительное истирание каменного материала.
Поэтому при использовании каменных материалов с износом лос-анджелесского барабана более 30 % нормируемое число оборотов бетономешалки для приготовления образцов щебеночно-мастичных асфальтобетонных заполнителей устанавливается 75 вместо 100.
Во многом это зависит от свойств компонентов смеси и их пропорций.
Существует несколько видов асфальтобетона, состав которых сильно различается. В некоторых случаях состав и качество исходных ингредиентов связаны с методом производства.
О роли песка в асфальтобетоне поговорим ниже.
Песок
Добавляется во все виды АБ, но в некоторых является песчано-асфальтобетонным, выступает единственным минеральным компонентом. используется как естественным путем — из карьеров, так и полученным просеиванием при дроблении. Требования к материалам диктует ГОСТ 8736.
.Минеральный порошок
Эта часть вместе с битумом образует вяжущее. Порошок также заполняет поры между крупными каменными частицами, что снижает внутреннее трение.Размер зерна очень маленький - 0,074 мм. Их получают из системы обеспыливания.
По сути, минеральный порошок изготавливается из отходов цементных и металлургических заводов - это опудривание смесей цемента, золошлаков, отходов переработки металлургических шлаков. Состав зерна, количество водорастворимых соединений, водостойкость и др. регламентируются ГОСТ 16557.
.Дополнительные компоненты
В исходную смесь добавляют различные добавки для улучшения состава или придания определенных свойств.Они делятся на 2 основные группы:
Выбор и проектирование композиций асфальтобетона для дорог и аэропортов обсуждаются ниже.
На видео ниже показан отбор проб для оценки состава и качества асфальтобетона:
Дизайн
Состав устройства для асфальтобетонного покрытия подбирается в зависимости от назначения: улица в маленьком городе, скоростная магистраль и велосипедная дорожка требуют разного асфальта.Для наилучшего покрытия, но не переусердствуя с материалами, следуйте этим правилам выбора.
Основные принципы
Смесь подобрана таким образом, чтобы кривая находилась в пределах нормы и не учитывала трещины: последнее означает избыток или недостаток какой-либо фракции.
Выбор состава
Процедура выбора в основном такая же:
Сначала проводятся теоретические расчеты, затем лабораторные испытания. В первую очередь проверяется остаточная пористость, а затем соответствие всех остальных характеристик ожидаемым.Расчеты и испытания проводятся до получения смеси, полностью отвечающей поставленной задаче.
Как и любой сложный строительный материал, АБ не имеет четко выраженных свойств - плотности, удельного веса, прочности и т.д. Его параметры определяют состав и способ приготовления.
Обучающее видео ниже расскажет вам о проектировании склада асфальтобетона в США:
.Китай Производители и поставщики вертикальных сушилок - Заводское предложение
Краткое введение в вертикальную сушилку
Вертикальная сушилка - это своего рода сушильное оборудование для обработки брикетов различных типов, таких как угольный брикет, брикет из минерального порошка, брикет из железного порошка, флюорит порошок, брикеты из окалины и т. д. Важно оборудовать линию по производству брикетов, чтобы уменьшить содержание влаги в брикетах. Вертикальная сушилка характеризуется низкими инвестиционными затратами, небольшой площадью покрытия, высокой эффективностью сушки, а также простотой в эксплуатации и обслуживании.Материалы, обрабатываемые вертикальными сушилками, легко транспортировать. Вертикальная сушилка представляет собой энергосберегающее и экологически безопасное устройство, которое не только улучшает утилизацию отходов, снижает загрязнение окружающей среды, но и обеспечивает хорошие экономические и социальные преимущества.
В настоящее время вертикальная сушилка широко используется как в Китае, так и за рубежом. Вертикальная сушилка, которая является важным оборудованием линии по производству брикетов, в основном используется для сушки угольных брикетов, брикетов из минерального порошка, брикетов из железного порошка, брикетов из гипса, брикетов из прокатной окалины, брикетов из флюоритового порошка и т. д.Влажность после сушки может достигать 8% ниже (влажность регулируется системой управления). Например, плавильный завод Shandong Laiwu использует его для сушки брикетов из окалины, группа Shanxi Guangda Coking использует его для сушки угольных брикетов, плавильный завод Oman Sohar для сушки брикетов из железного порошка. Вертикальная сушилка имеет широкий спектр применения.
Вертикальная сушилка производства Zhengke прошла проверку Бюро по контролю качества провинции Хэнань, сертификацию международной системы менеджмента качества ISO9001, сертификат CE европейского стандарта, российский сертификат ГОСТ и т. д.Тем временем мы подали заявки на множество патентов на вертикальные сушилки в Государственное патентное ведомство, и они были хорошо известны в отрасли сушильного оборудования.
Особенности вертикальной сушилки Zhengke
1. Высокая эффективность сушки, хороший эффект сушки. Вертикальная сушилка представляет собой сушильное устройство непрерывного действия. Вертикальная сушилка, используемая для сушки материалов по методу «подача с одного конца и разгрузка с другого», характеризуется высокой эффективностью сушки.Мы смогли контролировать и регулировать конечную влажность в соответствии с пожеланиями заказчика».
2. Энергосбережение, защита окружающей среды, отсутствие загрязнения, отсутствие шума. Вертикальная сушилка Zhengke может сушить угольные брикеты, брикеты минерального порошка, гипсовые брикеты, а затем повторно использовать их. Это улучшает использование ресурсов и снижает загрязнение пылью. Благодаря особой конструкции механической конструкции и электрическому управлению вертикальная сушилка работает с малой мощностью.Кроме того, вертикальная сушилка оснащена многоступенчатым пылеулавливающим оборудованием в соответствии с национальными экологическими стандартами. Снизить загрязнение окружающей среды оборудованием; это своего рода хорошее энергосберегающее и экологическое оборудование. Наша вертикальная сушилка имеет закрытую конструкцию, не загрязняет воздух, и во время процесса сушки возникает шумовое загрязнение.
3. Широкий спектр применения, низкие требования к рабочей среде.Вертикальная сушилка Zhengke применима во всех странах мира. Мы можем внести некоторые коррективы в зависимости от ситуации в разных странах, таких как напряжение, требования к конструкции, географические условия и т. д. Что касается рабочей среды, вертикальная сушилка Zhengke может нормально работать при сильном морозе, высокой температуре, плато и т. д.
4 Простая установка . Вибрации на ходу нет. Также удобно переносить и транспортировать оборудование.
5. Мало рабочих, простота в эксплуатации, простота обслуживания.По запросу клиента Zhengke может предоставить полуавтоматические и полностью автоматизированные производственные линии. Требуется только регулярное обслуживание руководства. Его очень легко поддерживать.
6. Высокий уровень безопасности. Все части редуктора имеют закрытую или полузакрытую конструкцию в соответствии со стандартами безопасности оборудования, такие как приводной вал, двигатель, шкив и т. д. Это обеспечивает безопасность оборудования и рабочих.
Главный технический техник:
| мощность (кВт) | ||||||||||||||||
ZKWD-1800 | 3-6 | 22 | |||||||||||||||
-2800 ZKWD |
| 8-10 30 | |||||||||||||||
-3000 ZKWD |
| ZKWD -3200 | 15-20 | 37 | Вертикальная сушилка Процесс диаграммы 1, Сырье 2, Номинальный силос 3 Конвейер 3 5, впуск 6 、 Нагнетающий шнек питателя 7 、 Редуктор 8 、 Двигатель 9 、 Основание 10 Высокое давление Машина для брикетирования сухого порошка 11 、 Готовая продукция 12 、 Разгрузочный конвейер 13 、 Конвейер
Kehua Industrial является одним из ведущих производителей и поставщиков высококачественных и безопасных вертикальных сушилок в Китае.Наши вертикальные сушилки продаются по низким ценам, и на нашем заводе есть много товаров на складе. Приглашаем вас купить у нас энергосберегающее, экологичное и дешевое оборудование и ознакомиться с нашим предложением. Hot Tags: вертикальная сушилка, Китай, производители, поставщики, фабрика, предложение, купить, дешево, скидка, цена, в наличии .Калий хлористый в качестве удобрения: инструкция по применениюКалий хлористый или хлористый калий — минеральное удобрение, применяемое в агротехнике для нормализации роста и развития садовых культур и восстановления необходимого баланса питательных веществ. Используют как самостоятельно, так и в составе комплекса с другими азотными и фосфорными удобрениями. Основным действующим веществом добавки является калий, необходимый элемент для всех без исключения растений и почв, до 90% чистого калия.Выпускается в виде белых, серых или розово-коричневых гранул или кристаллов. Вещество получают лабораторным путем путем смешивания гидроксида калия с соляной кислотой. Сырьем для удобрения служат различные калийсодержащие соли. Подкормка этим средством незаменима на всех типах почв и благотворно влияет на плодородие садовых растений. На слабых, истощенных почвах применяется в комплексе с полезными азотно-фосфорными удобрениями, на более тяжелых и кислых почвах - как самостоятельная добавка. Из положительных свойств, которыми обладает калий на огородных культурах, можно выделить такие, как: Для положительного эффекта от внесения этого удобрения соблюдаются строго определенные дозы и сроки. Избыток хлористого калия в почве приводит к снижению плодородия и нарушениям вегетативной системы растений из-за присутствия в рецептуре натрия и хлора. Для защиты посевов от этих двух соединений удобрение вносят в межсезонье, при обильных и частых поливах или во время сильных дождей. Вода постепенно вымывает из почвы хлор, оставляя в ней только кристаллы калия, которые плодотворно поддерживают корневую систему в течение всего роста. Основные виды калия и их отличия по стандартам ГОСТКалий хлористый выпускается в виде мелких гранул и кристаллов с высокой растворимостью. В садоводстве более востребованы крупнозернистые, зернистые варианты, которые не вымываются и дольше остаются в почве. Внешний вид, содержание дополнительных примесей и соединений регламентируются стандартами ГОСТ. В сельском хозяйстве чаще всего применяют калий с обозначением 4234-77 или 4568-95. Между собой эти продукты отличаются процентным содержанием хлора, натрия, калия и других элементов и химических веществ.. Согласно нормативам массовая доля свободных кислот, сульфатов, фосфатов, различных оснований, нитратов и др. В химическом составе KCl ГОСТ-4234-77 не должна превышать 2%. Все остальное – чистый хлористый калий в виде сыпучих белых кристаллов с крупной фракцией. Применение такого вещества особенно распространено в пищевой и фармацевтической промышленности, в сельском хозяйстве его применяют в качестве подкормки только в сочетании с азотно-фосфорными удобрениями в составе комплекса. В чистом виде для полей, садов и дач применяют гранулированные и мелкодисперсные порошки калия хлористого с обозначением ГОСТ-4568-95. Он бывает двух видов, отличающихся химическим составом (40 или 60% активного вещества в составе), а также внешним видом (серые, белые или розовые гранулы или порошок). Инструкция по применению и меры предосторожностиКалий хлорный как удобрение относится к группе веществ, умеренно опасных для человека.При попадании внутрь может вызывать некоторое раздражение кожи и слизистых оболочек, тормозит заживление ран и способствует воспалительным процессам. Во время работы рекомендуется носить перчатки и другую защитную одежду. В воздухе хлоркалий не опасен и не выделяет никаких вредных веществ или соединений, которые могут негативно воздействовать на людей или здоровые растения в данной местности. Калий хлористый хранится согласно инструкции 6 месяцев со дня изготовления.Благодаря высокому показателю гигроскопичности удобрение хранят в помещениях с пониженной влажностью воздуха в плотно закрытых полиэтиленовых пакетах или пластиковой таре По истечении рекомендованного срока годности при соблюдении всех требований к упаковке и месту практически не теряет своих химических свойств но становится более ломкой и меняет цвет. В садоводстве категорически не рекомендуется использовать хлористый калий в сочетании с доломитовой мукой, всеми остальными видами извести или мела.Кроме того, он полностью совместим с популярными азотно-фосфорными и органическими комплексами. Опасность недостатка или избытка калия в организме растенийНедостаток или избыток калия отрицательно сказывается на росте и развитии всех без исключения садовых растений. Они плохо усваивают такие полезные элементы, как азот, фосфор, магний, кальций или цинк, замедляется рост, постепенно отмирают листья и побеги, изменяются параметры плодов и клубней. Заключить, что растение остро нуждается в калийных удобрениях, в том числе хлористом калии, можно по следующим признакам: Дефицит калия чаще всего наблюдается у сельскохозяйственных культур, произрастающих на относительно истощенных, бедных почвах, особенно на песчаных, заболоченных или торфянистых участках. Своевременное и правильное внесение хлористого калия и других удобрений с высоким содержанием калия позволяет улучшить развитие растений на всех стадиях роста. Рекомендуемое удобрение в садуРазличные корнеплоды лучше всего реагируют на калий, включая свеклу, редис, морковь и картофель.Этот микроэлемент положительно влияет на формирование большинства злаков, огурцов, кабачков, винограда, томатов и баклажанов. Содержание хлора в действующем веществе может повредить некоторые растения, особенно большинство ягодных кустарников, а также бобовые и табак. В случае негативной реакции растений на хлор рекомендуется прекратить подкормку участка этим видом удобрений и заменить его более «лояльными» калийными смесями, например сульфатом калия или сульфатом калия-магния. Для нейтрализации хлорного эффекта KCl вносят в основном осенью при перекопке или вспашке земли. В начале вегетации все вредные вещества, в том числе и хлор, вымываются из почвы, оставляя в ней только полезный калий. Весной удобрение вносят только на почву с повышенной влажностью или во время сильных дождей или таяния снега. Весеннюю подкормку проводят также на легких супесчаных почвах с близким расположением грунтовых вод.Общая норма расхода препарата составляет 10-20 грамм на 1 кв.м. квадратных метров осенью или в два раза больше весеннего внесения удобрений. Для улучшения проникающих свойств хлористый калий лучше вносить после обильного полива и в виде жидкого раствора, который готовят из расчета 25-30 г вещества на 10 л теплой воды. Внесение удобрения под популярные огородные растенияКартофель удобряют калийной подкормкой только совместно с другими азотно-фосфорными комплексами. Хлор отрицательно влияет на клубнеобразование и снижает количество полезного крахмала. KCl вносят строго 1 раз в течение сезона, осенью под перекопку в пропорции 80-100 г на 10 м2. метров посадок. Для поздних сортов картофеля лучше вносить калимагний или присыпать рядки цементной пылью. Весной томаты подкармливают только сульфатом калия, осенью можно удобрить почву небольшим количеством хлористого калия из расчета 50-60 грамм на 10 м2.м площади и всегда в жидком виде. Но огурцы нуждаются в калии больше, чем любое другое плодородное растение. Непосредственно влияет на формирование вкусовых свойств, так что овощи, лишенные этого элемента, становятся вялыми, горькими или безвкусными.. Однако необходимо осторожно вносить хлоридный материал под огурцы и кабачки. Избыток еще хуже влияет на формирование плодов. Сначала рекомендуется выборочно подкормить 1-2 куста на участке. Готовят маточный раствор 0,5-1 л на 1 растение и через неделю-две смотрят на внешний вид кустов, если листья не изменили окраску, завязи в порядке, то проводят комплексную кормление всеми овощами. Нормы внесения для винограда, фруктовых деревьев и цветовДля винограда хлорид калия не используется, но ограничивается другими минеральными удобрениями или сульфатом калия. Плодовые деревья, особенно груши и яблони, требуют систематического внесения этого вещества несколько раз в сезон как до, так и после цветения.120-150 г кристаллов или гранул подкладывают под большое дерево или выливают в виде раствора по окружности приствольного круга, а затем обильно поливают 2-3 ведрами воды. Хлорированное калийное удобрение также используется для подкормки декоративных растений и цветов. Розы и все сорта семейства подкармливают 2 раза за сезон 10 г порошка, который растворяют в 10 л теплой воды. Пионы и тюльпаны подкармливают не более 1 раза минимальным количеством (5-7 г сухого веса), очень плохо реагируют на хлор.В случае с клубневыми и плетистыми сортами дозу калия увеличивают до 20-25 г. Хлористый калий не рекомендуется применять для комнатных растений, так как хлор невозможно вымыть из почвы, что может затормозить их развитие в неестественных условиях. . Технология производства горчичных растений. Предлагаем вам ознакомиться с аннотациейИзобретение относится к пищевой промышленности... При производстве горчичного порошка Семена горчицы очищают, кондиционируют по влажности и размеру семян, привозят, оболочки отделяют от ядра. Зерно дробят до следующего фракционного состава, мас.%: полузерна не более 15, проходящие через миллиметровое сито не менее 85, цельных зерен нет.Гигротермическую обработку проводят свежим паром до влажности 10 %, затем сушат до влажности 4-5 %, доводя температуру мезги до 100-115 о С. Прессование, кек измельчают, при измельчении дополнительно 5-7 % семян добавляют белой горчицы или 5-7% желтой горчицы или 5-10% смеси белой и желтой горчицы в соотношении 1:1 от массы горчицы и просеивают. При этом получается горчичный порошок с контролируемой резкостью. 1 таб. Изобретение относится к масложировой промышленности и касается процессов приготовления горчичного порошка.Известный технологический процесс получения горчичного порошка включает следующие операции: очистку семян горчицы, кондиционирование семян по влажности и крупности, шелушение, отделение шелухи от ядра, дробление, обработку влагой, прессование, измельчение теста и просеивание до раздельный порошок (см. Руководство по приготовлению и технологии калибровки) Переработка растительных масел и жиров. Л., 1960, т. I, с. 256, 265), взятый за прототип. Однако горчичный порошок, полученный этим способом, быстро теряет свои свойства: характерный острый вкус и остроту, необходимые при производстве готовых пищевых горчичников и горчичников, т.к.При высоких температурах прессование и прессование масла инактивирует фермент мирозиназу, что способствует гидролизу синигрина и образованию аллилизотиоцианата (АИТЦ), придающего горчице ее специфические свойства. Задача, решаемая при разработке изобретения, заключается в получении горчичного порошка с заданными свойствами. Технический результат - получение горчичного порошка с регулируемой жесткостью, т.е. с регулируемым содержанием аллилизотиоцианата. Конкретный технический результат при реализации изобретения достигается за счет того, что в известном способе получения горчичного порошка измельчение ядра приводит к фракционному составу, мас.%.: Половинки ядра - не более 15 Пропустить через сито 1 мм - не более 85 Целые ядра - нет Влаготермическую обработку зерна проводят свежим паром до влажности 10%, затем сушат до влажности 4-5%, доводя температуру мезги до 100-115 o C, а при измельчении жмыха добавляют 5-7% семян горчицы белой или 5-7% семян горчицы желтой или 5-10% семян горчицы белой. добавляют и желтки в массовом соотношении 1:1 теста.Измельчение ядра до определенного фракционного состава позволяет добиться максимально полного разрушения клеточной структуры ядра, что способствует лучшему извлечению масла при прессовании. Семена горчицы содержат тиоглюкозид синигрина и фермент мирозиназу, в присутствии воды происходит гидролиз синигрина и образуется аллилгорчичное масло, что и определяет острый вкус горчицы. При обработке ядер семян острым паром и повышении температуры до 100-115 o C выход жирного масла увеличивается на 2-3% за счет более полного раскрытия клеток семян и снижения вязкости масла.Но при этом фермент мирозиназа инактивируется, и гидролиз синигрина с выделением аллилизотиоцианата не идет полностью, в результате чего горчичный порошок теряет характерные свойства: терпкий и острый вкус. Введение в жмых цельных зерен горчицы на стадии помола в количестве 5-10 % от массы жмыха, в которых фермент мирозиназа сохраняется в нативном состоянии, позволяет осуществить более полный гидролиз синигрина и получить указанное количество AITC и соответственно контролирует степень остроты конечного продукта, т.е.Пудра. В заявляемом способе можно получить содержание АИТЦ от 0,67 до 1,20% в абсолютном выражении на сухое вещество... Способ осуществляют следующим образом. Семена горчицы в сепараторах очищаются от посторонних примесей и минеральных остатков, металлические загрязнения удаляются магнитами, установленными перед и за сепараторами. Влажность семян, вводимых в производство, должна быть 6,5 - 7,0%. После очистки семена калибруют по крупности на ситах или сепараторах.Шелушение семян горчицы производят на вальцовых машинах, после чего зерно от шелухи отделяют на аспирационной крупе. Для нормальной подготовки к прессованию ядра семян измельчают на четырехвалковых вальцах по фракционному составу, мас.%: Половина бобов - не более 15 Целые ядра - нет Измельченные бобы идут в первую жарочный чан, где они варятся свежим паром, чтобы довести влажность до 10%. Происходит частичный гидролиз синигрина.Во 2-х нижних чанах печи мезгу высушивают до влажности 4-5% и нагревают до температуры 115 o C, фермент мирозиназа инактивирует. После прессования горчичный жмых с частично прореагировавшим синигрином и частично инактивированной мирозиназой направляют на измельчение на пятивалковых машинах ВС-5 с последующим отделением порошка на ситах. Частичную инактивацию фермента мирозиназы завершают добавлением в тесто на стадии помола 5-7% семян горчицы белой или желтой или 5-10% смеси семян горчицы белой и желтой в массе 1:1 к тесту. .Варьируя количество подаваемых целых семян, можно контролировать содержание аллилизотиоцианата в порошке. Результаты испытаний сведены в таблицу. ЗАКОНСпособ производства горчичного порошка, включающий очистку семян горчицы, кондиционирование в зависимости от влажности и размера семян, дробление их, отделение шелухи от ядра, дробление, тепловлажностную обработку, прессование, дробление теста и грохочение, отличающееся тем, что дробление зерна приводит к фракционному составу, мас.%:Половинки зерен - не более 15 Прохождение через сито 1 мм - не менее 85 Зерна целые - нет Гигротермическую обработку проводят свежим паром до влажности 10%, затем подсушивают до влажности 4 - 5 %, доводя температуру мезги до 100 - 115 o С, и при измельчении жмыха добавляют 5 - 7 % семян горчицы белой или 5 - 7 % семян горчицы желтой, горчицы дополнительно семян, или 5 - 10% смесь семян белой и желтой горчицы в соотношении 1:1 по массепирог. Потребление кетчупа, горчицы и майонеза превышает три килограмма на человека в год, поэтому пастообразные соусы и специи всегда будут востребованы. Организация пищевой промышленностиНеобходимо зарегистрировать ООО будущего мини-завода и определиться со стратегическими партнерами по реализации продукции (оптовики, базы). Супермаркеты, которые предпочитают иметь дело с проверенными производителями, особенно важны, потому что они обеспечивают максимальные продажи. Нормативная проработка и ГОСТ ГОСТ 9159-71, ГОСТ Р 53590-2009 и ГОСТ Р 52141-2003 . Выбрано помещение, соответствующее санитарно-гигиеническим нормам, и приобретена технологическая линия по производству кондитерских изделий. Создается бизнес-план (в котором должны быть указаны - дневной объем производства, все затраты и чистая прибыль). Рентабельность продаж является ключевой и должна составлять 90 043 на 55% 90 044 для годового дохода. Для подтверждения качества всех видов пастообразных изделий необходима сертификация с соответствующим пакетом документов, по которым будет производиться продукция.Это могут быть ГОСТы (категория «Экстра» без искусственных консервантов) или фирменные технические условия (ТУ) для других категорий. Технология производства майонезаСостав майонеза не регламентируется ГОСТ. Основные ингредиенты: растительное масло (более 30%), яйца, сахар (ксилит), соль, молоко. В цеху необходимо иметь три чана (для жидких яиц, масел и паст). Яйца пастеризуют и перекачивают в охлаждающую ванну. Затем добавляют соевое масло и разводят специи в яблочном уксусе.Машина перемешивает смесь при комнатной температуре в течение шести минут до получения однородной массы и майонезной пасты. После выборочного лабораторного контроля качества майонеза по цвету, запаху, вязкости и другим параметрам его разливают в тару с дозатором (одноразовые двухслойные полиэтиленовые пакеты). Технология приготовления кетчупаТоматная паста разбавляется водой, смешивается в котелке с сахаром (сорбитом), солью, фруктовыми пюре, крахмалом, стабилизаторами, красителем.Перед розливом в банки, пакеты и пластиковые стаканчики их проверяют в лаборатории рефрактометром на массовое содержание томатного сухого вещества и по другим параметрам (аромат, консистенция). Горячее литье (80 градусов) обеспечивает оптимальное качество. Производство горчицы Измельченные семена (17%) добавляют к смеси перца, куркумы, соли, уксуса, воды (до 60%) и перемешивают около часа до разламывания ядер. Масса переливается в контролируемую кофемолку, где зерна перемалываются кремовыми камнями при температуре 60 градусов.Параметры приправы проверяются и разливаются в банки. Для обслуживания линии по производству кетчупа, майонеза и горчицы достаточно пяти человек. Для стимулирования темпов продаж рекомендуется предоставлять скидки оптовикам, дополнять продукцию рекламными проспектами, проводить акции по скидкам. Работа напрямую с супермаркетами дает вам максимальную отдачу, а качество вашего продукта будет работать само собой.Продажи жирного майонеза превышают объемы продаж низкокалорийного майонеза, поскольку потребителей интересует качество, а не цена. А если учесть, что рынок еще не насыщен печеньем (тенденция к росту составляет более 2%), то производство кетчупа, горчицы и майонеза гарантирует стабильную прибыль. Соусов много разных... Один из любимых соусов - простой горчичный. Она имеет разные вкусы и уже давно присутствует на наших столах, практически в каждой семье. Если вы хотите организовать свой прибыльный бизнес, то можете рассмотреть этот вариант открытие цеха по производству горчицы ... При этом стоимость такого производства будет минимальной. Вам не придется закупать сырье по высокой цене и устанавливать дорогостоящее оборудование. Поэтому открыть цех по производству горчицы под силу даже мелким предпринимателям. При правильном подходе к подробному бизнес-плану ваше производство окупится в короткие сроки. Помещения Для горчичного цеха требуется помещение высотой не менее трех метров, подключенное к водо- и электроснабжению, с вентиляцией и естественным освещением.В таком помещении надо будет сделать ремонт с учетом всех требований СЭС... Или попробовать снять помещение на пищевом предприятии. В вашем помещении должно быть несколько дополнительных помещений – гардеробная для персонала, для хранения – сырья, тары и конечного продукта. Сырье. Для приготовления горчицы вам потребуется: Горчичный порошок Инвентарь. Перед покупкой оборудования решите, будете ли вы производить только горчицу или дополнительно будете производить и другие соусы. Ведь горчица, как правило, продукт сезонный, и пик ее реализации приходится на зиму. Так что давайте рассмотрим вопрос о выпуске дополнительных соусов, таких как кетчуп и майонез. Таким образом, вы стабилизируете свой доход в течение года. Но тогда придется вкладываться на порядок больше. Но решение за вами. Если вы будете производить только горчицу, наша промышленность предлагает готовые производственные линии для этих продуктов.Монтаж оборудования и обучение персонала входят в стоимость готовой линии. Готовая линия включает в себя: Варочный котел Производительность такой линии 250 кг в рабочую смену, стоимость около 220 тыс. руб. Теоретическая рентабельность такого производства составляет 50 тысяч рублей при постоянном рынке сбыта. Для производства нескольких соусов придется приобрести более дорогой производственный комплекс. Включает в себя: Баня для длительной пастеризации Сразу определитесь с упаковкой. Потому что необходимо правильно подобрать упаковочное оборудование. Преимущественно, пластиковая упаковка намного дешевле, чем стеклянная тара, что снижает производственные затраты.
Для фасовки в пластиковую тару вам потребуется: Дозатор для липкого и жидкого продукта Даже если вы откроете цех по производству только горчицы, со временем вы сможете докупить дополнительное оборудование и увеличить диапазон. Персонал. Обязательно наймите опытного технолога, а количество сотрудников будет зависеть от размера вашего производства (в начале их может быть два) и менеджера по продажам, который будет заниматься непосредственно реализацией готовой продукции. Бухгалтер может приехать. Для реализации рассмотрим всевозможные варианты - контракты с супермаркетами, небольшими магазинами, небольшими киосками быстрого питания и т.д. Затраты и доходы. Стоимость 1 кг горчичного порошка около 52 руб. За месяц вы произвели 500 кг продукта — это 2500 упаковок по 200 г), значит, стоимость всей произведенной продукции составит около 26 тыс. руб. Выручка за весь продукт примерно 76 тысяч рублей при условии полной реализации. Расходы на аренду, сырье, заработную плату и т.д. составят около 32 тысяч рублей. Прибыль после уплаты налогов составит около 15 тысяч рублей. Изобретение относится к масложировой промышленности.При переработке семян горчицы 25-30 мас.% добавляют к измельченным семенам перед прессованием. вода. Смесь нагревают до 35-45°С и выдерживают 15-20 минут. Затем снова сушат при 80-110°С до влажности 5-6% по массе. Это позволяет получить масло с запахом и вкусом горчицы, а благодаря наличию горчичного масла продлить срок годности с 6 до 12 месяцев. 1 таб. Изобретение относится к пищевой промышленности и может быть использовано для производства пищевого ароматного горчичного масла, содержащего вещества столовой горчицы.Известный технологический процесс переработки семян горчицы включает следующие операции: очистку семян от механических примесей, кондиционирование их по влажности и крупности, шелушение семян и отделение шелухи (шелухи) от зерна, дробление зерна, прессование, фильтрацию. масло (Руководство по технологии получения и переработки масел и растительных жиров В настоящее время ароматические растительные масла, которые используются в производстве соусов, майонезов и других специй.Поставленная задача достигается добавлением 25-30 мас.% к молотым семенам горчицы перед прессованием. воды, смесь нагревают до температуры 35-45 o C и выдерживают при этой температуре 15-20 минут, т.е. проводят реакцию гидролиза с природным веществом синигрином, входящим в состав семян горчицы, в результате чего получают горчицу эфирное масло, придающее жирному пищевому горчичному маслу специфический аромат и вкус столовой горчицы. Кроме того, наличие горчичного масла значительно замедляет процессы окисления, происходящие в масле при хранении, что продлевает срок годности масла с 6 до 12 месяцев.Пример. Взять 100 кг горчицы без механических примесей, кондиционировать ее по крупности, растолочь, отделить оболочку (шелуху) от ядра, размолоть зерна и добавить 25-30 кг воды (25-30% по массе). смесь нагревают до 35-45°С и выдерживают при этой температуре 15-20 мин. Затем массу повторно нагревают до температуры 80-110°С, сушат до остаточной влажности 5-6% по массе. водным и прессованным известными способами... Горчичное масло, полученное предлагаемым способом, имеет специфический аромат и вкус, характерные для столовой горчицы, а срок его хранения продлевается до 12 месяцев.В таблице приведены показатели качества пищевого ароматного горчичного масла, полученного по известной технологии и предлагаемому способу, при его хранении. Из данных таблиц видно, что пищевое ароматическое горчичное масло, полученное по предлагаемому способу, имеет более низкие кислотность и перекисные числа, чем масло, полученное по известной технологии, за счет этого срок годности масла увеличивается с 6 месяцев по ГОСТ 8807-94 до 12 и более. Таким образом, предлагаемый способ позволяет получить ароматизированное пищевое горчичное масло и продлить срок его хранения. Закон Способ переработки семян горчицы, включающий очистку семян от механических примесей, кондиционирование их по размеру, шелушение, отделение оболочки (шелухи) от ядра, измельчение, прессование, фильтрацию масла, характеризующийся тем, что что перед прессованием 25-30% вес. воды, смесь нагревают до 35-45°С и выдерживают при этой температуре 15-20 мин, затем повторно нагревают до 80-110°С и сушат до остаточной влажности 5-6% по массе. вода. В этой статье: Производство майонеза и кетчупа по праву считается одним из самых прибыльных.Производство горчицы несколько уступает в экономическом отношении, поэтому ее рекомендуется рассматривать как вспомогательный продукт. Возрос интерес населения к мелкосерийному производству, отклоняющемуся от стандартов массового производства. Этот тренд может быть очень полезен для начинающего трейдера. В среднем население потребляет около 3,5 кг пастообразных продуктов (майонеза, горчицы и кетчупа) в год. Таким образом, товар будет востребован, а его производство будет экономически выгодно. Организационные нюансы пищевой промышленности1. Определить организационную форму управленияДля работы мини-завода по производству пастообразных продуктов рекомендуется зарегистрировать ООО в системе общего налогообложения. Стратегическими партнерами являются оптовики, оптовики продуктов питания и супермаркеты, которые часто предпочитают сотрудничество с надежной компанией. Для составления периодических отчетов экономичнее будет воспользоваться услугами аутсорсинговой компании. В процессе регистрации начинающему предпринимателю потребуется следующий код ОКВЭД: 15.87 Производство специй и приправ 2. Изучаем регламентПеред выдачей первой партии пастообразных продуктов рекомендуется изучить государственные стандарты: 3. Сертификация продукцииДля организации производства всех видов соусов в обязательном порядке необходимо пройти сертификацию и получить на руки необходимый пакет документов, которые подтвердят качество продукции. Нормативными документами могут быть указанные выше ГОСТ или ТУ (технические условия), разработанные ими самими. Технология производства майонезарецептуры майонезов разные, но основные ингредиенты остаются неизменными - яйца и растительное (соевое) масло.Из яиц берут только желтки, только белки или и то, и другое. Яйца должны быть пастеризованы, чтобы убить сальмонеллу и другие бактерии. Яйца доставляются на крупные предприятия в жидкометаллических цистернах. Яйца перекачиваются по шлангу в охлаждающую емкость. Вторым основным ингредиентом является соевое масло. Все резервуары или другие емкости, предоставляемые поставщиком, должны быть герметично закрыты и не открываться до прибытия на мини-завод.Насос также перекачивает масло в резервуары для хранения. Затем взвешиваются дополнительные ингредиенты — специи, которые нужно добавить в секретный рецепт компаний. Полученная смесь выливается в бак. комнатной температуры... Результатом смешивания всех ингредиентов является майонезная паста. Тем временем сырые яйца были вылиты в большой холодильный бак. И так, в производственном зале 3 емкости: с лапшой, яйцами и соевым маслом... Более того, в определенном соотношении (согласно рецепту компании) все ингредиенты отправляются в смесительный чан. Через 5 минут работы яйца, паста и масло смешиваются в однородную массу - майонез . Периодически образцы продукции мини-завода отправляются в лабораторию для контроля качества. Лаборанты оценивают такие параметры, как цвет, консистенция и запах.После проверки готового продукта на качество, упаковочная машина выливает его в пластиковую тару. Фольгу рекомендуется помещать внутрь крышки, фиксируемой индукционным нагревом. Именно она защитит майонез от нагревания, а также укажет на то, что банка не вскрывалась после отправки с завода. Лаборатория контроля качества проводит еще одну проверку - измеряется консистенция продукта. Технология производства кетчупаПроизводство кетчупа начинается с добавления смеси сахара и соли в гигантский котел с водой.Ингредиенты тщательно перемешиваются. В качестве основного сырья на фабриках часто используют готовую концентрированную томатную пасту, которую перекачивают в большую камеру ферментации. Поместите туда раствор сахара и соли. Варочный котел Смесь тщательно перемешивается в гигантском котле. Между внутренней и внешней стенками устройства подается пар, препятствующий пригоранию массы. Мешалки постоянно вращаются и делают кетчуп однородным, т.е.смесь гомогенизируется. Варка для кастрюли Готовый заводской соус отправляется на лабораторные испытания, где рефрактометром измеряют массовую долю растворимых сухих веществ - т.е. выясняют, достаточно ли томатов в кетчупе. Если эксперта устраивают все параметры (консистенция, аромат, цвет и т.д.), партия отгружается в бутылях. Контейнеры можно изготовить в местной мастерской.В их основе гранулы ПВХ, из которых состоят многие пластмассовые изделия. Затем добавляется краситель, благодаря которому емкость приобретет заметный красный цвет. Гранулы нагревают и измельчают в устройстве, похожем на мясорубку - экструдере. Горячие красные «колбаски» с двух сторон прижаты стенками форм. Шприц вводит порцию воздуха в пластиковую заготовку, и заготовка становится «горшочком». Примечателен тот факт, что стандартная бутылка кетчупа весит всего 42 грамма, идет на розлив прямо с конвейера, едва охлажденной. При этом кетчуп разливают по горячей технологии, когда температура готового продукта должна быть не ниже 80 градусов. В этом случае предотвращается появление и рост бактерий в соусе. Затем бутылки доставляются с крышками, этикетками и упаковываются в коробки. Технология производства семян горчицыИсходными ингредиентами для производства продукта являются: семена горчицы, перец и куркума, соль, вода и белый уксус...Измельченные ингредиенты высыпают в миксер с водой и уксусом. Ориентировочные пропорции для производства желтой горчицы следующие: 60% воды, 20% уксуса, 15% семян и 5% специй. Семена горчицы добавляются последними. Огромный роторный миксер смешивает все ингредиенты около часа на скорости разбивания зерен (до 265 км/ч). Вращающийся миксер Содержимое переливается в измельчитель из нержавеющей стали. Внутри машины 2 искусственных шлифовальных камня (жернова). В процессе помола смесь нагревается до 60 градусов, в результате чего превращается в светло-желтую горчицу кремообразной консистенции. Перед наполнением бутылок проверьте готовый продукт на однородность. Если частицы крупнее четверти миллиметра, специалисты адаптируют жернова под программу более тонкого помола. Организуем мини-завод - перечень обязательных этаповНачальный этап выпуска первой партии готовой продукции это: Этап закупки оборудования неразрывно связан с планируемым объемом производства. Практически все технологические линии имеют аналогичную конфигурацию. Отличие заключается в конструкции гомогенизатора — аппарата, отвечающего за дробление на микроскопические капли. Основными факторами, влияющими на выбор будущего предпринимателя, являются стоимость технологической линии и степень автоматизации технологического процесса. Вы также должны выбрать метод упаковки.Для майонеза наиболее предпочтительными вариантами являются тубы (пластиковые одноразовые пакеты) или пластиковые контейнеры. Оборудование для этого вида упаковки дешевое. При розливе в стеклянные банки готовый продукт будет иметь максимальный срок хранения, а процесс производства отличается интенсивностью труда. Поэтому первый способ упаковки пастообразных продуктов (майонеза, кетчупа и горчицы) является наиболее предпочтительным, так как можно будет добиться минимальных затрат на хранение и транспортировку. Приобретаем технологическую линию для производства пастообразных изделий, состоящую из следующих узлов: Стоимость технологической линии 3 000 000 руб. Планируется, что продукция мини-завода будет в среднем ценовом сегменте. Планируется производство майонеза, кетчупа и горчицы. Экономическая целесообразность производственного процессаДля работы мини-завода по производству кондитерских изделий достаточно 9 человек: Общий месячный фонд оплаты труда составляет 70 000 руб. Ежемесячные постоянные расходы будут разделены на следующие разделы: Итого: 96 000 руб. Бизнес-план производства майонезаУказать стоимость 1 килограмма майонеза (2 банки по 500 грамм). Исходные ингредиенты для производства готового продукта: Итого: 28,55 руб. Планируемое суточное производство майонеза 70 кг (140 пластиковых банок или 350 туб). Таким образом, месячное производство с учетом 22 рабочих дней составит 1540 кг (3080 упаковок готовой продукции в пластиковой таре или 7700 штук готовой продукции в тубах). Итого себестоимость = Месячная выработка х Себестоимость 1 кг майонеза = 1540 кг х 28,55 руб. = 43 967,00 руб. Валовой доход = месячное производство х розничная стоимость 1 кг майонеза = 1540 кг х 150 руб.= 231 000 руб. Финансовые показатели мини-завода за первый месяц работы предприятия будут представлены в следующем виде: Бизнес-план производства кетчупаРассчитаем себестоимость 1 кг кетчупа (2 банки по 500 грамм).Исходными ингредиентами для производства готового продукта являются: Итого: 45,50 руб. Ежемесячное производство готовой продукции составит 1650 кг или 5500 упаковок по 300 грамм. Итого себестоимость = Месячная выработка х Себестоимость 1 кг кетчупа = 1650 кг х 45,50 руб. = 75 075,00 руб. Валовой доход = месячное производство х розничная стоимость 1 кг кетчупа = 1650 кг х 130 руб. = 214 500 руб. Мини-завод завершит первый месяц работы по реализации кетчупа со следующими финансовыми показателями: Бизнес-план производства горчицыРассчитаем себестоимость 1 кг горчицы. Для его производства необходимы следующие ингредиенты: Итого: 51,10 руб. Ежемесячный выпуск готовой продукции составит 500 кг или 2500 банок по 200 грамм. Итого себестоимость = Месячная выработка х Себестоимость 1 кг горчицы = 500 кг х 51,10 руб. = 25 550 руб. Валовой доход = месячное производство х розничная стоимость 1 кг горчицы = 500 кг х 150 руб. = 75 000 руб. При условии реализации 100% готовой продукции мини-завод завершит первый месяц работы со следующими показателями: Итак, производство майонеза, кетчупа и горчицы является экономически выгодным делом... Общая чистая прибыль составляет 271 935 рублей, а средняя рентабельность продаж составляет 45%. Финансовые вложения полностью окупятся за 1,5 года. Продажа мучных изделийОсновной задачей менеджера по продажам должно быть заключение договоров с оптовиками, продовольственными магазинами и супермаркетами. В начале, чтобы стимулировать стратегических партнеров, стоит использовать несколько простых приемов: количество пакетов; В целях повышения узнаваемости продукта производитель может сделать подарки с логотипом компании (ручки, календари, блокноты и т.д.) и сделать их общедоступными бесплатно. Также будет целесообразно провести акцию по продаже упаковки по сниженной цене. Стимулировать краткосрочный рост продаж можно при реализации 2-3 сопутствующих товаров (майонеза, кетчупа и горчицы) по более низкой себестоимости. В первые месяцы работы мини-фабрики вложения в рекламу не будут отличаться внушительными размерами.Особенно это касается планов работы исключительно для вашего региона, а также сотрудничества с мелкими оптовиками и напрямую с супермаркетами. В этом случае вкусовые качества изготовляемой продукции будут работать сами на себя. Однако в случае увеличения ассортимента необходимо будет правильно продвигать товар. Понятная упаковка, креативный слоган, участие в международных конкурсах и получение наград будут способствовать росту потребительского спроса. Да, это последний день года и пора представить вина, от которых моя кровь взволновалась больше всего, глаза задрожали и слезились. На бумаге они не всегда могут быть самыми большими бутылками, но они затронули мои самые чувствительные струны, поэтому я обязан им несколькими абзацами. Несмотря на то, что 2021 год в целом был не очень приятным, он был чрезвычайно щедрым в плане вина. Я отметил несколько пунктов из списка мечты (два-три конкурса и два-три энтузиаста), несколько раз судьба удивляла сама себя.В целом получилось очень хорошо. Сегодняшний список не имеет никакого порядка, кроме хронологического - иду по хронологии записей в своем гугл листе с пометками и возвращаюсь с душой (есть ли она?) и памятью к мгновениям приподнятого настроения за бокалом вина. Приглашаю вас в свой субъективный топ-10 вин (эта круглая цифра вышла случайно, но вы, наверное, все равно не поверите), которыми я облила губы бисером. Peter Wetzer Silberberg Kekfrankos Sopron 2018 абсолютный шедевр австрийского гаража, который выжимает свои вина в Шопроне, Венгрия, с минимальным вмешательством в процесс.Прекрасные ароматы цветов, вишни и ее семян, хвои, влажной земли, сливы, дыма, перца, чернил и молочных ноток - бывает очень много. Вкус густой, концентрированный, а тело окутано вишневой кислинкой, эссенция вишни во вкусе, хорошо дозированная кислота и много жизни и радости. Послевкусие долгое, вишнево-пряное, минеральное. Красивое, чистое и точное вино, отражающее эмоции винодела. Импортер: Рымарчик и Бялоброкки . Оценка: 94 балла . ![]() Маркус Хубер Грюнер Вельтлинер Metamorphosis Niederösterreich 2019 4 месяца на кожуре, 10 месяцев на осадке и яблочно-молочное брожение привели к созданию красивого, сложного, но в то же время удивительно дружелюбного и доступного вина.Есть мандарин, чай из каркаде, корица, кардамон, молоко с медом, гвоздика, немного черствая балансовая древесина... отличный нос! Во рту он мягкий, плотный, сытный, с бульонной соленостью, легкой горчинкой, отличной свежестью, придающей живость; есть дикие яблоки, мирабель и меловая минерализация. Долгий, чуть согревающий, с пряностями и просто замечательный. Импортер: Danubia Fine Wines . Цена: 150 злотых. Оценка: 94 балла . Niepoort Voyeur Douro DOC 2018 или Дору заново, в легкой и свежей версии, выдержанной в глиняных амфорах.У нас чудесное свежее вино, благоухающее эссенцией красных фруктов, глиняный горшок – все светло, просторно и радостно. Во рту воздушное, воздушное, вишнево-малиновое, дополненное лесными ягодами, крохотной танинностью и необычайной сочностью. Ультравкусное вино, удивительно вкусное. Ему не нужно напрягать мышцы, чтобы получить удовольствие. Импортер: Вининова . Цена: 99 злотых. Оценка: 93 балла . Silva Daskalaki Grifos Kotsifali Rosé 2018 Критская роза, которая созревала в течение 5 месяцев в 300-литровых глиняных амфорах.Толкает красную смородину, арбуз, соль, горшок и сушеные травы. Во рту довольно сильная структура, но в то же время много свежести красной смородины и граната, соленый и крошечный, кирпичный танин, который поднимает и без того долгое послевкусие. Одно из открытий этого года. Импортер: в Польше нет. Цена: 24 евро. Оценка: 92 балла . ![]() Wieninger Ried Rosengartel 1ÖTW Nussberg Wiener Gemischter Satz DAC 2019 Длинное имя, но и отличное вино.Прекрасный Gemischter Satz, микс сортов с одного участка, который интенсивно пахнет дымом, перцем, розовым джемом, сухоцветами, абрикосами, ананасом, манго - так же восхитительно, как прогулка в цветущем саду. Во рту густые, массивные, но в то же время удивительно изящные яблоки, абрикосы, грейпфруты в сочетании с кардамоном с прекрасной размеренной кислинкой растворялись в этой материи. Отличное вино без сомнения. Импортер: Мельжиньски . Цена: это вино не предлагается импортером, цена в Австрии - 32 евро.Оценка: 95 баллов . Yalumba The Signature Cabernet Sauvignon & Shiraz Barossa 2016 прекрасное вино из антиподов, с интенсивными ароматами сливы, вишни, черносмородинового крема, эвкалипта, темного шоколада, мокко, цветов, запеченного бекона, сосновых иголок, с деликатным оттенком паприки. . Крепкое во рту, еще очень танинное и, кроме того, невероятно концентрированное, но без преувеличения или излишнего мышечного напряжения — мощное, но не выдержанное вино с идеальным послевкусием кедра и черной смородины.Рассвет! Импортер: этикетка недоступна в Польше, но другие вина Yalumba доступны в AMKA. Цена: около 50 евро. Рейтинг: 93 балла. Thierry Germain Domaine Roches Neuves Saumur Champigny 2016 бутылка, которая была днем лошади во время питья. С самого начала - мурашки по коже. Красиво интегрированные, ягоды черной смородины, сливы сочетаются с кофейными нотками в красивом, точном потоке винного сознания — здесь все чисто, красиво прорисовано пером.Во рту кристальная эссенция черной смородины, интегрированный танин, щепотка земли - точность была достигнута. Какая-то необыкновенная космическая энергия течет в этом вине. Превосходно! Импортер: Винотека 13 . Цена: 145 злотых. Оценка: 94 балла . Thymiopoulos Rosé de Xinomavro 2007 Последнее воплощение розового. Полноценное вино, невероятно сложное и все еще живое, несмотря на годы. Розовое варенье, пряности, гибискус, ройбуш, легкая аптечная смесь, карамель, запеченная петрушка, молоко, анис, кожа - все это в носу.Во рту чудесно свежий, спелый, но полный энергии, отличная кислотность клюквы, плюс ройбуш, немного розового варенья, рябины, пряных специй. Красивое вино, у которого еще есть время. Импортер: недоступно в Польше. Цена: около 35 евро. Оценка: 96 баллов . Quinta do Vesuvio Vintage Port 2018 идеальный портвейн из одной квинты. Пахнет джемом из темных фруктов, кремом из черной смородины, малиновым соком, черными оливками, свежемолотым черным перцем, лавровым листом, душистым перцем. Густой во рту, с удивительными перечными танинами и, несмотря на 100 граммов сахара, на вкус почти как сухой. вино.Красивый, долгоживущий - прятаться лет 20-30. Он имеет большую вековую традицию. Импортер: недоступно в Польше. Цена: около 80 евро. Оценка: 96 баллов . Пенфолдс Бин 707 Каберне Совиньон 2012 Впечатляющее вино со спокойствием и культурой, с очень классическим, концентрированным ароматом, с большим количеством черносмородинового ликера, жареного и сладкого перца, эвкалипта. Густое, с шелковистой текстурой во рту, с идеальными, сочными, слегка меловыми танинами; прекрасно проведенная кислинка, вкус сливок черной смородины, черной смородины и оттенком паприки, кофе, молочного шоколада.Красивый, сочный финиш, который длился вечно. Вино, восхитительное по дизайну и мастерству. Близко к идеалу. Импортер: CEDC. Цена: более 2000 злотых. Оценка: 98 баллов . Конечно, эта подборка не охватывает всех замечательных вин, которые я пробовал в этом году. Были некоторые из них, за что я безмерно благодарен. Как видите, стилистический диапазон очень широк, и в вине это здорово. А что покорило ваши сердца и вкусы в 2021 году? Заглавное фото: Пьер Демартен на Unsplash .Рецепт водки в домашних условиях - Камогоноварение 2022Для приготовления водки недостаточно смешать спирт с водой, полученная смесь лишь отдаленно напоминает хорошие магазинные аналоги. Производство водки представляет собой технологический цикл, состоящий из нескольких этапов, каждый из которых по-своему важен и требует решения. Для начала советую обзавестись хотя бы простейшим спиртометром - прибором Определение крепости спиртовой смеси. Без замеров получить водку до заданного числа оборотов сложно, потому что заявленная крепость спирта не всегда соответствует реальной необходимости добавления ингредиентов «на глаз», что не очень хорошо. Технология производства домашней водки1. Алкоголь на выбор. Во-первых, вам нужно купить или получить алкоголь, еду или медицинские препараты. От качества зависит вкус и безопасность водки. Если надежность поставщика вызывает сомнения, следует проверить образец метилового спирта несколькими способами. Смертельным является технический (метиловый спирт), который не отличается от этанола по вкусу, цвету и запаху. Это чрезвычайно важно!Согласно ГОСТу спирт следующих сортов используют для производства ликероводочной продукции при наиболее дополнительной и лучшей базовой очистке альфа.Наивысшее качество альфа – это спирт, полученный из пшеницы, ржи или смеси трав. Степень основы и роскошные добавки изготавливаются из смеси зерна и картофеля в разных пропорциях (чем меньше картофеля, тем лучше), по качеству немного уступает. Для производства спирта высшей очистки используют крахмалистое сырье (свеклу, патоку, картофель и др.), являющееся основой для получения самой дешевой водки. Теоретически из двойной перегонки можно сделать крепкий самогон, но это будет нарушением традиционной технологии, поэтому водку следует использовать в крайнем случае. 2. Отбор воды. Именно вода влияет на вкус, чистоту и мягкость водки. Обыкновенный водопроводный или минеральный – неверное решение. Для разбавления спиртом нужна вода, содержащая минимальное количество солей и минералов, причем дистиллировать или кипятить воду нельзя, иначе она будет плохо смешиваться со спиртом. Лучше покупать минеральную воду. При выборе магазина обратите внимание на количество соли и минералов, концентрация этих веществ должна быть минимальной.Для того чтобы приготовить подходящую водку, очищенную воду, детское питание продается в отделах. Вода детская самая мягкая3. Производство прочих ингредиентов. Спирт разбавляется водой, а вкус резкий и сушит кончики языка. Для снятия этого эффекта сделайте мягкий выбор водки, добавив в состав: глицерин (до 5 мг на 1 л водки), аптечную глюкозу (10-20 мл на 1 л) или декстрозу (4,1 г на л). , сахар (одна столовая ложка на литр). Дорогая водка с использованием порошка декстрозы (глюкозы) — лучший вариант. Дополнительно можно смягчить ароматизированную водку лимонным соком. На 1 л напитка достаточно 30 мл свежевыжатого сока, лимон некрупный. 4. смешивание. В России крепость водки должна быть 40-56% от минимальной крепости ЕС - 37,5%. Эти коэффициенты необходимо учитывать для расчета коэффициента разбавления. Лично мне нравится водка крепостью 45%, но могут быть разные предпочтения. Приведенный ниже сервис, взятый из нашего калькулятора самогонщика, поможет вам правильно рассчитать количество воды.Остальные ингредиенты не учитываются. объем спирта: литраВведены неверные данные спирт Процентное содержание: %Введены неверные данные Процент после: %Введены неверные данные Рассчитать... Введите базовые данные осталосьвместо После разбавления необходимо добавить воды Последовательность перемешивания: подготовить емкость для заполнения необходимым количеством воды, добавить смягчители вкуса (глюкоза, сахар, глицерин, лимонный сок), хорошо перемешать.Тонкой струйкой вливайте спирт в воду (наоборот делать нельзя). Накройте крышкой и перемешивайте раствор в течение 1-2 минут при энергичном встряхивании. Оставить возможность стоять в течение 2-3 часов. 5. Фильтрация. Необязательный этап, на котором водка немного окисляется, дополнительно очищается воздух внутри угля с некачественным сырьем. В домашних условиях проще всего провести очищение, пропустив 1-2 раза через напиток новый фильтр для очистки воды, например, «БРИТА», «Барьер» или «Аквафор». Альтернатива - наполнение ватной воронки, положить березовый уголь или активированный уголь в несколько таблеток. Фильтр не очень эффективен, но если спирт и вода хорошего качества, то этого будет достаточно. Самый простой фильтр6. Подпорно-герметичный. Для улучшения вкусовых качеств готовую водку перед употреблением выдерживают 3-10 дней в холодильнике (закрытом) до полного растворения спирта, реакционной смеси, воды и других ингредиентов. Водка спиртовая альфа. Чем отличается цемент М400 от описания и отличия М500 (Ремонт и строительство)Без цемента не обходится абсолютно ни одна строительная площадка. Это важный фактор на всех этапах строительного процесса. Материал по своей сути уникален тем, что его аналоги еще не обнаружены. Определение и состав цементаЭтот строительный материал представляет собой клинкерный порошок , в который введены модифицирующие добавки и наполнители. Проще говоря, цемент – самый популярный строительный материал, который используется для возведения конструкций различного типа и производства высокопрочных изделий.При этом внешне цемент выглядит как порошок серого цвета, состоящий из мелких крупинок. Зерна в сочетании с водой превращаются в однородную смесь.
Виды цементаЦемент делится на несколько видов:
Основным техническим признаком любого вида цемента является марка .Марка цемента традиционно маркируется буквой «М» и цифровым индексом. В свою очередь цифры обозначают максимальную цифровую нагрузку в килограммах на определенный объем затвердевшего цемента, то есть его прочность на сжатие. Другими словами, на практике это означает вес, который цемент может выдержать, не разрушившись. Например, известный цемент марки М400 может перевозить 400 кг соответственно, а М500 соответственно 500 кг. В чем разница, кроме весовой категории, между двумя марками цемента М400 и М500?! Цемент марки М400Цемент этой марки обладает достаточно высокими прочностными и антикоррозионными свойствами .Эта марка считается одной из самых распространенных, как в промышленном, так и в бытовом строительстве. Цемент М400 используется в качестве основы для строительства из бетона или бетонного раствора. Кроме того, прочность этого цемента позволяет использовать его в строительстве ЖБИ. Данная марка цемента нашла применение в следующих отраслях строительных работ:
Основным и первым базовым фактором этого цемента являются низкие требования к твердению и строительные нормы . Кроме того, отсутствие трещин при некоторых отклонениях от технологии, что является еще одним преимуществом цемента этой марки. И конечно это неоспоримый факт, как и цена. Цемент этой марки значительно дешевле высоких марок, что позволит значительно сэкономить бюджет. Также стоит упомянуть о таком преимуществе, как морозостойкость.. Единственным недостатком цемента марки М400 является прочность , а именно эта марка цемента не подходит для строительства высотных зданий.Цемент марки М500Цемент этой марки является быстросхватывающимся строительным материалом. Этот цемент способен выдерживать нагрузку до 500 кг на см. Благодаря своим быстротвердеющим свойствам этот цемент используется в ремонтных работах и аварийном ремонте. Существует два вида цемента этой марки, это:
Эта марка нашла применение в производстве различных бетонных и железобетонных конструкций. С применением этого цемента изготавливают сборные железобетонные элементы, фундаменты, балки и готовят растворы следующих видов: Безусловно, говоря о цементе такой марки, следует сказать о в основном имеющихся достоинствах, а именно: Кроме вышеперечисленного, благодаря наличию в цементной смеси активных минеральных добавок, следует сказать о повышенных антикоррозионных качествах.
Различия между М400 и М500Рассматривая два варианта, становится ясно, что у М500 есть преимущества, так как, помимо производства тротуарной плитки и брусчатки, она также применяется при строительстве многоэтажных монолитных жилые дома. Прочность также относится к отличительной черте этих двух видов цемента.
|